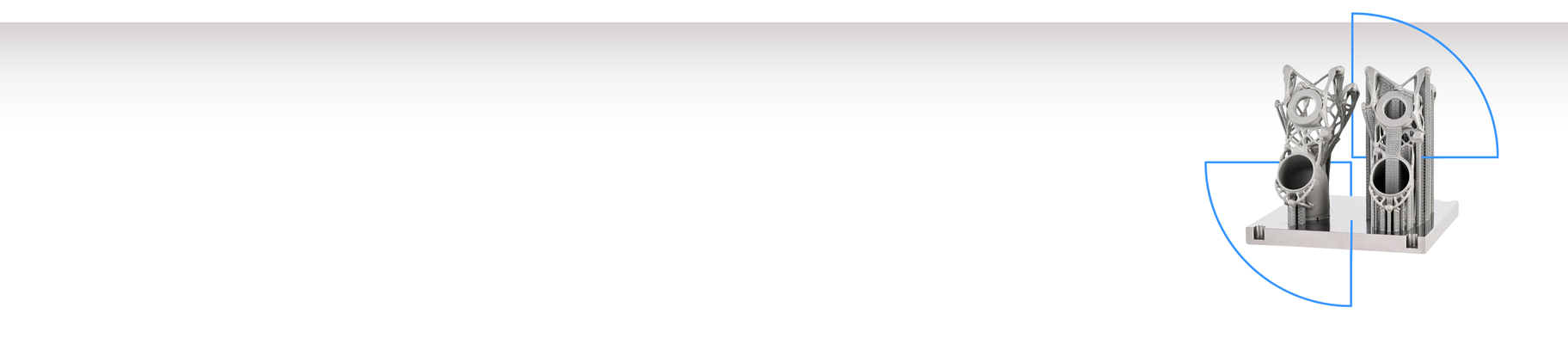
Meno supporto -
AM per la sostenibilità
16 SETTEMBRE 2021 | Tempo di lettura: 5 min | Autore: Ho Kei-Leong
La produzione additiva (AM), nota anche come stampa 3D industriale, è spesso considerata sostenibile per l'efficienza dei materiali, la riduzione del consumo energetico, la produzione localizzata, la personalizzazione e l'ottimizzazione della progettazione, la riciclabilità e la riduzione dei requisiti di attrezzaggio. Sebbene l'AM abbia intrinsecamente questi vantaggi in termini di sostenibilità, rimangono molte sfide da affrontare.
Nel mondo del DMLS ("Direct Metal Laser Melting"), la necessità di strutture di supporto durante il processo di stampa rimane una delle maggiori sfide. Con l'aiuto di una gestione termica avanzata, è possibile ridurre le strutture di supporto regolando la potenza del laser. Le strutture di supporto sono essenziali per evitare che elementi sporgenti o intricati si deformino o collassino durante l'applicazione degli strati metallici. Se da un lato le strutture di supporto sono fondamentali per il successo del processo di stampa, dall'altro comportano inefficienze e sprechi sotto forma di materiale, post-elaborazione e aumento del consumo energetico.
Per affrontare queste sfide, ricercatori e produttori stanno lavorando per sviluppare strutture di supporto più efficienti per ottimizzare il processo di stampa complessivo. Uno degli approcci più efficienti e innovativi è l'implementazione di sistemi di monitoraggio e controllo in tempo reale per aiutare a identificare e risolvere i problemi durante il processo di stampa, creando così un sistema ad anello chiuso per le regolazioni in tempo reale.
EOS Smart Fusion
EOS Smart Fusion è una soluzione di controllo a retroazione ad anello chiuso assistita da un monitoraggio in tempo reale e da regolazioni adattive del processo per favorire la stampa di parti con supporti minimi. È stato sviluppato come metodo di gestione termica intelligente, su misura per i produttori, per consentire la stampa di componenti con supporti minimi. Ciò comporta una riduzione dei tempi di costruzione, dei tempi di post-elaborazione e dello spreco di materiale. Basato su un'accoppiata di hardware e software per la tomografia ottica, che consente di comprendere il processo attraverso una telecamera ad alta risoluzione nel vicino infrarosso, Smart Fusion registra e misura l'energia immessa in tempo reale per facilitare un'analisi più accurata dei singoli strati di costruzione.
Per verificare le premesse di Smart Fusion rispetto alla nostra struttura di base e a un altro software di terze parti disponibile sul mercato, è stato intrapreso uno studio con il nostro partner di ricerca, l'Advanced Remanufacturing and Technology Center (ARTC) di A*STAR, con sede a Singapore. L'obiettivo era fornire dati conclusivi per quantificare i miglioramenti apportati. La convalida dell'impatto sulla sostenibilità e l'etichettatura della manifattura additiva come futuro della produzione possono essere raggiunti solo attraverso dati empirici.

La metodologia inizia con lo scouting tecnologico e la ricerca sul mercato dei vari software di stampa senza supporto. Per questo studio è stato scelto l'acciaio inox 316L, materiale che notoriamente richiede strutture di supporto robuste per stampare con successo i componenti.* Sono stati quindi costruiti dei coupon angolati e una girante chiusa dimostrativa, che sono stati confrontati con vari approcci, compresa la quantificazione della precisione dimensionale. La girante è stata sezionata per acquisire micrografie della sporgenza, mentre i coupon angolari sono stati sezionati per valutare la rugosità e la porosità della superficie. Infine, è stata eseguita un'analisi comparativa delle emissioni di carbonio utilizzando l'EOS Carbon Calculator per esaminare le differenze tra i diversi approcci. Tutti i risultati sono evidenziati nella tabella e nell'illustrazione seguenti.
EOS Standard |
EOS con Smart Fusion |
OEM con Software A |
|
---|---|---|---|
Sporgenza angolare della cedola | xx | xxx | x |
Precisione dimensionale | xx | xxx | x |
Ruvidità della superficie | xx | xxx | x |
Porosità # | xx | xxx | x |
Impronta di carbonio | x | xxx | Nessun dato |
Tempo di stampa | x | xxx | xx |
Volume di supporto | x | xxx | xx |
Il modello EOS M 290 è stato utilizzato come base per confrontare e valutare tre diversi approcci: una stampa standard, una stampa standard con Smart Fusion e una macchina OEM diversa integrata con un software di terze parti per la riduzione del supporto disponibile in commercio, denominato "software A" in questo studio. Smart Fusion supera sia il software disponibile in commercio sia la girante stampata in modo convenzionale per quanto riguarda l'utilizzo del volume di supporto, costruendo con successo il pezzo giusto al primo tentativo.
La stampa basata sul software A ha richiesto più tentativi, con almeno 4 prove prima di ottenere il successo nella stampa della girante. Con Smart Fusion il pezzo è stato costruito in un tempo di lavorazione complessivo significativamente più breve, richiedendo un volume minimo di supporti e una precisione dimensionale superiore (vedere Figura X). Il confronto dei coupon angolati costruiti con Smart Fusion ha mostrato una migliore rugosità superficiale e una ridotta porosità (vedi Figura Y). In particolare, Smart Fusion ha permesso di ottenere l'angolo di sporgenza più basso che corrispondeva fedelmente al modello CAD della cedola.
Il risultato della valutazione comparativa quantifica ed evidenzia i notevoli vantaggi di EOS Smart Fusion. Rispetto alla stampa metallica convenzionale, si registra una riduzione del 38% del volume di supporto e un'enorme riduzione del 62% del tempo di stampa, pari a quasi un'intera giornata. Il costo di produzione di ogni pezzo si riduce quindi del 76%! Inoltre, Smart Fusion risponde alla richiesta di sostenibilità e riduzione dell'impronta di carbonio con una riduzione del 62% delle emissioni di CO2 durante la stampa (da 29 a 11 kgCO2-eq) e una sostanziale riduzione dell'84% delle emissioni durante la post-elaborazione (da 187 a 30 kgCO2-eq).
Con la sua gestione intelligente del calore, Smart Fusion offre un software che consente di modificare lo stress residuo AM dei metalli. Riducendo al minimo la perdita di materiale e accorciando i tempi di lavorazione, è possibile ottenere risparmi sui costi e rendere la produzione più sostenibile. Il nostro obiettivo è collaborare con i nostri clienti e partner per testare, implementare e ottimizzare questa soluzione, fornendo loro un vantaggio competitivo per sfruttare appieno i vantaggi dell'AM.
Con la continua evoluzione della tecnologia e la crescente adozione, EOS continuerà a sviluppare soluzioni AM all'avanguardia con la sostenibilità come obiettivo principale, adattate alle esigenze del mercato per plasmare il futuro della produzione.
Siete interessati a saperne di più? Non esitate a contattarci per una discussione approfondita su come EOS e Smart Fusion possono permettervi di realizzare una produzione sostenibile attraverso la produzione additiva!
* L'acciaio inox 316L è attualmente in fase di test con Smart Fusion. Di conseguenza, non è attualmente disponibile un processo standardizzato.
