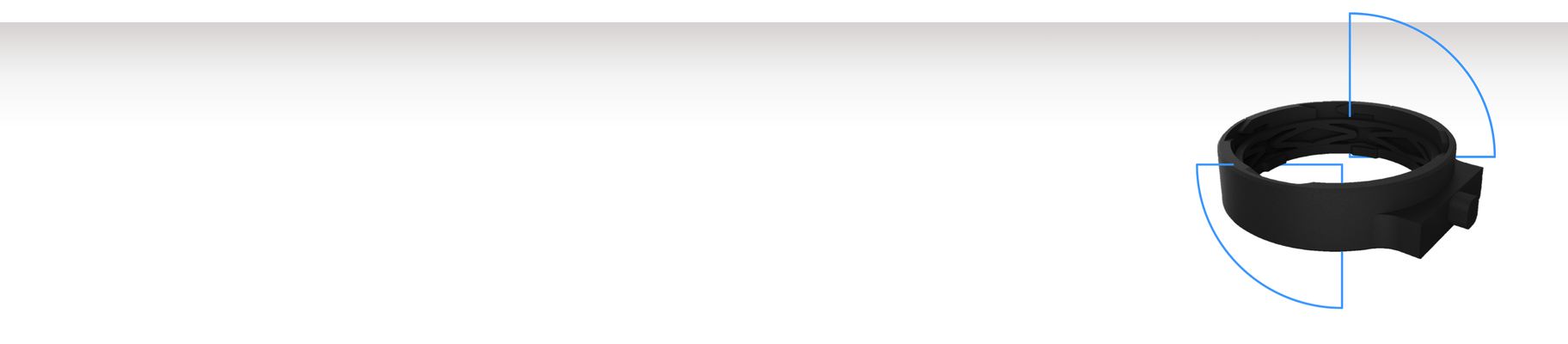
Carcasas
Diseño complejo y producción flexible
Una carcasa estable protege el interior. Las carcasas robustas suelen ser esenciales, sobre todo para los componentes electrónicos delicados. Tienen que ser resistentes y estar bien selladas, además de ajustarse al máximo, y deben fabricarse con la suficiente rapidez para lograr ciclos de producción cortos. Sin embargo, con el proceso de moldeo por inyección, la fabricación de carcasas con estas propiedades sólo es viable en producciones en serie muy grandes.
La impresión 3D industrial ofrece una alternativa rentable para la producción en series pequeñas y medianas de carcasas de plástico. Ya sea con materiales con propiedades aislantes o de disipación especialmente favorables, la fabricación aditiva de carcasas se caracteriza por su rentabilidad, libertad de diseño y potencial de integración funcional.
Tanto si desea fabricar prototipos como series piloto o pequeñas series de carcasas, la fabricación aditiva abre un gran abanico de posibilidades, entre las que destaca la reducción de los costes de producción.
Ventajas de las carcasas impresas en 3D
- Integrar funcionalidades para reducir el número de componentes
- Reducción del plazo de comercialización
- Proceso de fabricación económicamente atractivo
- Producir componentes de uso final estables
Carcasa de cámara impresa en 3D para exteriores
El reto consistía en fabricar un número reducido de unidades de un robusto soporte para cámaras con un diseño complejo. La carcasa debía ser lo bastante flexible para albergar seis cámaras. Al mismo tiempo, el proceso de producción debía ser abierto para admitir iteraciones posteriores del diseño sin causar problemas.
Gracias a la tecnología EOS, se pudo realizar con éxito un diseño de producto que antes habría sido imposible.
La colaboración con Freedom360 permitió realizar cambios en el diseño con rapidez. Midwest Prototyping pudo implementar una producción rentable en pequeñas cantidades.
Canto
La lámpara subacuática desarrollada es más pequeña, ligera y robusta que cualquier otra del mercado. Canto consiguió resolver este reto con un FORMIGA P 110 Velocis utilizando material PA 2200.
El sistema interno de la conexión de la lámpara fabricada por aditivos, que cuenta con un mecanismo de enclavamiento por resorte, se produce en una sola pieza. Esto ha permitido reducir el número de piezas de montaje de 3 a 1. Con un peso de sólo 580 gramos, la lámpara establece nuevos estándares. Además, Canto Ing. GmbH se ahorró la necesidad de fabricar una costosa herramienta de moldeo por inyección, que habría costado hasta 35.000 euros.
