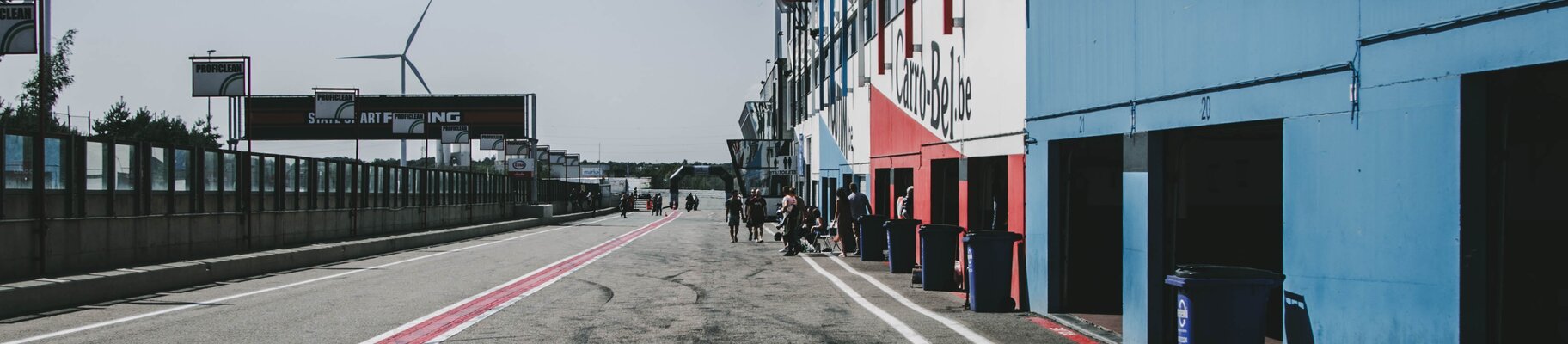
포뮬러 학생 팀, 배터리 하우징의 3D 프린팅 공기 흐름에 EOS P 396 사용
DHBW 엔지니어링 슈투트가르트 | 성공 사례
-
안전 관련 부품의 신속한 정비가 가능한 설계
-
구성 요소 무게를 80% 줄여 77g으로 줄였습니다.
-
전년도 차량과 비교했을 때 냉각 성능이 두 배 이상 향상되었습니다.
"EOS의 전문 지식과 기술 덕분에 전기 구동 경주용 자동차 eSleek14를 트랙에 투입하고 좋은 기록을 세우는 데 큰 도움이 되었습니다. 적층 제조의 장점은 부품 경량화, 아이디어의 빠른 실현, 그리고 이 모든 것이 극소량의 부품으로 가능하다는 점입니다. 사용 가능한 재료는 안전이 결코 타협되지 않는다는 것을 의미합니다. EOS에서 받은 교육 덕분에 우리는 프로세스를 최대한 활용할 수 있었고, 트랙에서 이를 증명할 수 있었습니다."
데이비드 쾰러 | 2013/2014 레이스 팀 배터리 개발 부책임자
강력한 파워: 적층 가공으로 제작된 포뮬러 학생 경주용 자동차의 냉각 시스템
DHBW 엔지니어링 슈투트가르트 팀에 속한 eSleek14에는 각각 60마력의 전기 모터 두 개가 장착되어 있습니다. 이 스피드 머신에 공급되는 전기는 차량 내부 측면에 고정된 배터리에서 공급됩니다. 공기 냉각 시스템의 구축은 적층 제조 전문가로서 EOS의 지원을 받았습니다.
배터리 컨테이너 개발 과정에서 개별 모듈 사이의 냉각 채널뿐만 아니라 컨테이너 끝에서 가장 효율적인 방식으로 공기를 외부로 배출하는 냉각 덕트도 구현할 수 있었습니다. 부품 무게에 대한 엄격한 사양을 충족하기 위해 제작팀은 경량 미세 폴리아미드 PA 2200을 선택했습니다. 이 소재는 높은 강성과 우수한 열전도율이 특징이며 모터스포츠 분야에 완벽한 특성을 가지고 있습니다.
공기 덕트는 레이저 빔이 분말 소재를 층층이 녹여 최종 부품을 형성하는 EOS P 396 을 사용하여 제작되었으며, 다음 단계는 부품을 차량에 성공적으로 통합하는 것입니다. 무게도 원하는 기준을 충족했습니다. 냉각 덕트 구성품의 무게는 77g에 불과했습니다.

"우리는 냉각 덕트를 적층 제조하기로 결정했고 EOS의 기술 덕분에 설계를 완전히 자유롭게 할 수 있었습니다. 수량이 워낙 적었기 때문에 사출 성형은 적합하지 않았고, 어쨌든 시공 설계를 변경해야 했을 것입니다."
데이비드 쾰러 | 2013/2014 레이스 팀 배터리 개발 부책임자
한 눈에 보는 결과
- -80% 무게 감소
- 100% 성능 향상
EOS 성공 사례
EOS와 함께 30년 동안 3D 프린팅의 우수성을 개척해 온 과정을 살펴보세요.