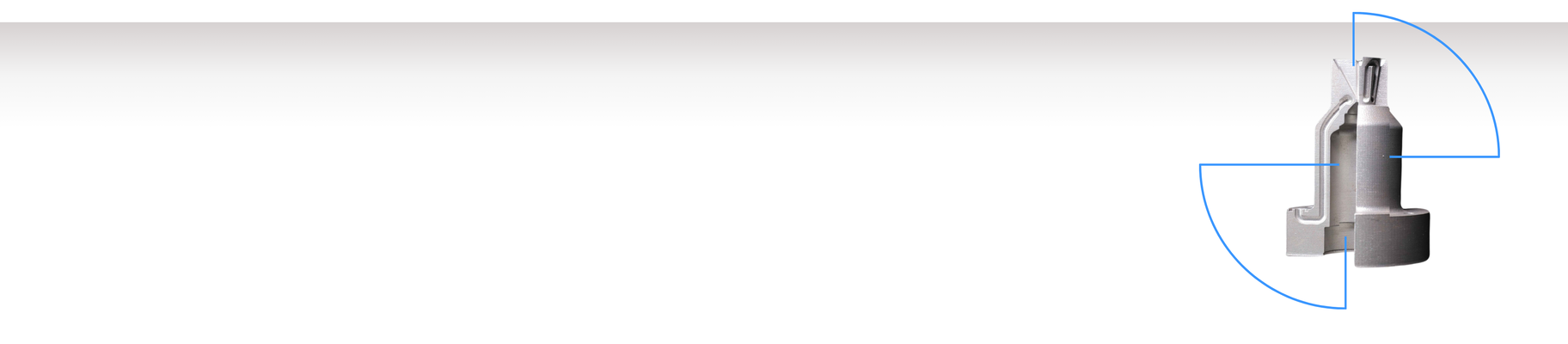
Tooling
3D Printing Solutions for Tooling
Reduce Cycle Times & Increase Cost-Efficiency
Why using additive manufacturing to produce 3D-printed molds and tools? As an industrial production method, additive manufacturing offers unparalleled design and manufacturing freedom. Even the most complex shapes can be designed and produced with the highest quality - quickly and cost-efficiently, even for small batch sizes. This makes 3D printing a powerful solution to a common challenge faced by tool and mold makers. In many industries, producing specialized tools and parts is one of the most resource-intensive manufacturing processes. Conventional methods are typically expensive, time-consuming, and technically demanding. The metal 3D printing process with EOS metal materials is the answer.
Die Casting and Injection Molding with Additive Manufacturing
Our metal 3D printing solutions enable the integration of temperature control and cooling channels directly into your tools and tool inserts using DMLS technology. Conventionally, these channels can only be drilled in straight lines. However, with additive manufacturing, even highly complex cooling geometries are possible, as the 3D-printed tool is built layer by layer from CAD data. This allows for more uniform and efficient heat dissipation, enabling targeted cooling around hotspots.
Advantages of 3D Printing in Tooling:
- Design Freedom: Complex geometries and optimized, lightweight tools offer unparalleled design freedom.
- Optimized Thermal Management: Conformal cooling optimizes thermal management, improving cooling speed and part quality.
- High-Performance Materials: Provide superior properties, uniform quality and validated EOS processes.
- Cost Savings: Tools reduce costs by minimizing waste, lowering maintenance and boosting efficiency.
- Digital Inventory: Faster lead times, efficient prototyping and quick transitions from design to finished mold streamline production.
Our Expertise Supporting the Tooling Sector
Innomia
Innomia uses EOS 3D printers for optimizing the production process for injection molded plastic parts. This involved a revision of the cooling process. The case concerns the manufacture of the armrest situated between the front seats.

AarKel Tool and Die Inc.
AM solves tooling challenges like long lead times and complex designs, offering faster production, improved performance, and cost-effective iterations. EOS’s systems provide high-quality, durable tooling solutions.

AarKel Tool and Die Inc.
AarKel’s journey into AM began about six years ago, driven by the company’s commitment to staying at the forefront of new technology. Focused on traditional tool and die manufacturing, AarKel began exploring metal 3D printing.

Exco Engineering
Exco Engineering is using AM to improve high-pressure die casting processes and overcome challenges such as complex geometries and thermal conditions. The company's innovative use of AM to create specialised inserts and custom manifolds demonstrates its potential to revolutionise the die casting industry.
