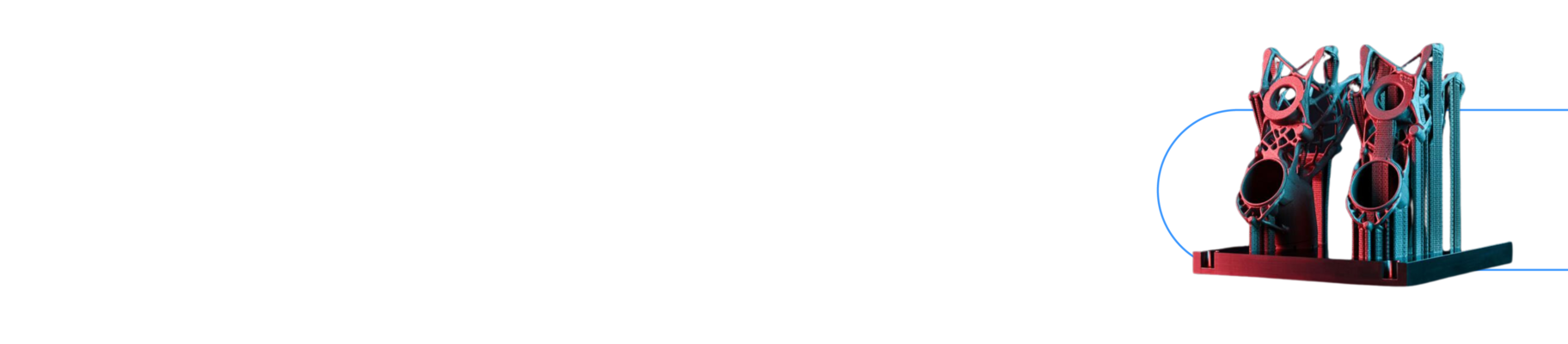
Revolutionizing Metal 3D Printing
with EOS Smart Fusion
Precision. Efficiency. Sustainability.
EOS Smart Fusion is our software innovation to significantly reduce cost, increase efficiency and quality in metal 3D printing. It is available with the EOS Smart Monitoring software plan and requires an OT camera system to enable advanced thermal management. This not only accelerates the additive manufacturing process of metal components, but also optimizes it by reducing support structures.
Key benefits of EOS Smart Fusion:
How EOS Smart Fusion works
In general, the Smart Fusion software optimizes the laser power of the metal EOS system in real-time to efficiently overcome manufacturing challenges. It measures the local thermal conditions and adjusts the laser power based on algorithms and OT data.
In detail, Smart Fusion enhances the traditional DMLS process through its real-time monitoring and closed-loop feedback system. It constantly monitors thermal emissions produced by the melt pool and the part through advanced sensors and imaging systems and analyzes the gray values. Leveraging this data, it dynamically determines the ideal laser power depending on the part geometry. First time right – Smart Fusion reduces the number of trials to 1 This process is repeated layer by layer with a high optical resolution of approx. 100 μm. The number of iterations required to get a part right is reduced to one, along with the advantage of reducing support structures which solely exist to dissipate heat.
Smart Fusion Replay: Reproducible Intelligence for Quality-Critical Applications
Smart Fusion Replay enables the adaptive process control of Smart Fusion to be applied as a fully reproducible manufacturing process – a crucial advancement for quality-critical industries such as aerospace and medical technology. This feature allows a previously optimized build job to be repeated deterministically, including all laser-related corrections. As a result, the benefits of Smart Fusion – such as reduced support structures, shorter build times, and improved part quality – can be leveraged more reliably and traceably, even in highly regulated production environments. Smart Fusion Replay thus forms a vital bridge between intelligent process control and industrial-scale series production.
