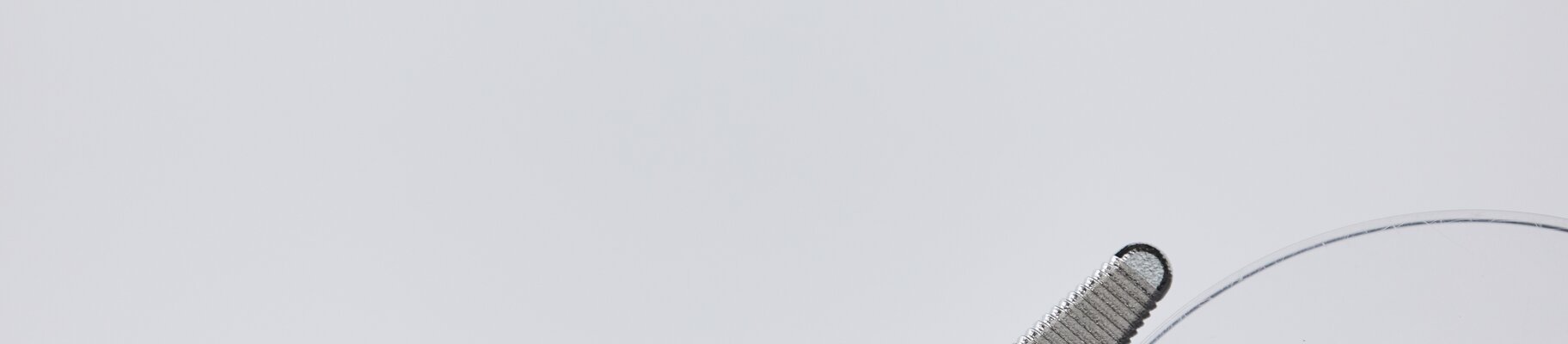
3D Printing for Medical Technology
Customized and Optimized Production
Creating Innovations That Make a Difference
Additive manufacturing offers the medical industry great freedom of design, adaptability and functional integration. For the manufacturers of dentures, medical and orthopedic technology products, orthoses and prostheses, this creates many far-reaching opportunities. There is complete control over the shapes, materials and specific designs based on patient-specific data which makes it possible to offer more individual treatments, simplifies biomechanical reconstruction and enables innovative therapy methods to be implemented quickly.
"With more than 30 years of experience in manufacturing all kinds of machines and solutions for additive manufacturing, we have accompanied and supported our customers across a diverse range of exciting and innovative medical projects. In doing so, we have learned to understand the specific requirements of this market."
We design our production technology to reflect our knowledge of the challenges associated with certifications and material-specific requirements. For better patient care.
Away From Standardized Solutions Towards a Patient-Specific Approach
With additive manufacturing, prostheses, orthoses and dental implants can be manufactured directly from each patient’s individual anatomical data. This results in custom products that are rapidly available, which significantly improves the healing process and prognosis.
Industrial 3D printing opens up far-reaching opportunities for manufacturers of dentures, medical and orthopedic technology products, orthoses and prostheses: the customization potential of products, combined with cost-efficiency, makes it possible to manufacture better and more economically viable products and develop new business models.

Away From Standardized Solutions Toward Improved Functionality
The ability to create complex geometries and integrate functionality with the additive manufacturing process creates vast benefits in orthopedic technology and when manufacturing complex medical equipment.
Our technologies have now been used in custom implants for several years. In complex cases, cancer treatment, implant revision or serious accidents, these patients may benefit from EOS additive manufacturing technology which allows a specific and potentially very complex product to be designed and quickly made available based on their individual diagnosis. EOS 3D printing technology can also be used to create a wide variety of surface structures, which can simplify processes such as osseointegration, namely the growth between living bone tissue and the surface of the bone implant.
For high-tech medical equipment and specialized machines, the freedom of design means that assemblies can be simplified and functionality can be integrated into the part. In these cases, additive manufacturing can pay off even with small batch sizes. Tool costs are eliminated, as well as any assembly and logistics costs.
With 3D printing, the design is driven by functionality and no longer by manufacturability. Whether for manufacturing implants, surgical instruments or complex medical technology products: additive manufacturing empowers you to reimagine the geometry. As a result, you can design and manufacture your products more efficiently for their specific applications.

3D Printing for Implants and Surgical Instruments
Patient-Specific and Accurate Implants and Surgery Instruments From the 3D Printer
EOS additive manufacturing technology creates precisely fitting instruments and implants directly from CAD data.
The process manufactures implants based on anatomical data collected from the wearer and allows them to be delivered quickly. This avoids any waiting times or complications due to extended periods of inactivity, so the implants fit better. It also speeds up the healing process as a whole and has a lasting positive impact on the patient’s quality of life.
"Products can be designed to reflect the diagnosis, no matter their level of complexity, they can be manufactured and delivered to the clinic in the shortest possible time. It takes about 6 weeks for conventional manufacturing, whereas with additive manufacturing, production is possible within just 10 days."
Additive manufacturing by EOS can also be used to create a wide variety of surface structures, which can simplify processes such as osseointegration, namely the growth between living bone tissue and the surface of the bone implant. The applications of 3D printed implants include spine implants, shoulder joints (glenoid replacement, hip implants) and implants for the OMF area (oral and maxillofacial surgery).
For complicated interventions, surgeons are increasingly switching to patient-specific single-use instruments. This allows the implants to be inserted more precisely, increasing the success of the operation for patients, surgeons, and hospitals. These customized instruments can also be manufactured with a 3D printer. The surgeon benefits from a high-quality and precise product that meets the strict standards associated with medical applications.
The 3D printed alternative enables greater variety (“mass customization”), and production can be performed “on demand". Compared to multiple-use instruments, hospitals save on sterilization and storage costs and benefit from higher productivity.







3D Printing in Practice
Permedica: 3D Printing of an Artificial Hip Cup

To show the video you have to accept marketing cookies.
Surface structure for improved osseointegration
The implant can be significantly optimized thanks to 3D printing. The hip cup consists of fixed sections to provide the necessary stability and elements with rough structures. These elements are structured directly to ensure that the implant is firmly anchored: coarse structures are advantageous in terms of pressure transmission, whereas smaller structures support the initial fixation. In this way, the complex structure simplifies osseointegration, accelerating the healing process.
Flexible production is possible
Together with the EOS Additive Minds team and the well-established EOS M 290 system for metals, Permedica succeeded in creating a completely new product. The entire implant is made in a single production step on the 3D printer and would be incredibly difficult to reproduce with conventional manufacturing methods. Thanks to the high flexibility of additive manufacturing, the surface and size of the hip cup can be specified individually for each patient.
Whitepaper: Multi-Machine Capability Study for Lattice Structures
This whitepaper investigates the performance of a standardized job layout with lattice structures printed on three different EOS M 290 systems using EOS Titanium Ti64ELI. In a nutshell, the results verify that
-
The machine to machine repeatability of capability is proven as relative density and compression strength both achieve Six Sigma confidence level
-
There is a high correlation between relative density and compression strength.
-
The testing scope and effort can be reduced due to this high correlation
Want to learn more? Get the free Whitepaper here.

EOS Success Stories
Implantology Products With Manufacturing Systems by EOS

Developing Biocompatible Materials for Implants
Customer Success story|University of Michigan
The University of Michigan uses a FORMIGA P 100 to produce individualized and lifesaving implants for children. Together with EOS they develop new biocompatibe materials.

Cranial Implants Produced With Additive Manufacturing
Customer Success Story | Alphaform
Development and manufacture of a precision-fit implant for the cranial area with particular permeability for liquids and heat dissipation.
Additively Manufactured Instruments for Medicine




BodyCad: Surgical Guide System for Knee Operations
To show the video you have to accept marketing cookies.
Together with BodyCad, EOS developed a surgical drilling template for customized knee arthroplasty. The system offers a more precise and controlled method to prepare the bone for the implant. A combination of a patient-specific implant and a surgical drilling template was developed to facilitate precise knee replacement or restoration interventions that reflect the patient’s anatomical features and musculoskeletal system.
The result was a revolutionary unicompartmental knee system (UKS) with patient-specific surgical instruments. The newly manufactured instruments, featuring custom drilling templates, guarantee higher precision at lower costs, reduced operation times and better clinical results. Made on an FORMIGA P 110 with the material PA 2201.
- Efficient: the instruments can be created quickly
- Profitable: lower costs compared to conventional processes
- Timely: patient-specific instruments can be delivered within 21 days
Stereotactic Platforms for Neurosurgery
Small-batch production of precision surgical components using a FORMIGA P 100.

Our Additive Manufacturing Solutions for Orthopedic Technology
Additive manufacturing helps to optimize patient treatment, reduce hospital stays and alleviate side effects. With our systems, you can make individual implants and instruments from high-quality, medically compatible materials based on 3D CAD data. Whether from metal or polymer materials, our 3D printing solutions enable tool-free production of highly customized products at low unit costs within a cost-efficient framework.
We help you to implement your products
With the right 3D printing system and our comprehensive consulting and training services, our customers successfully master their entry into the manufacturing of high-precision, patient-specific implants and instruments.
Our Integrated Solution Portfolio
Your Production Solution From a Single Source
We offer customer-specific 3D manufacturing solutions for the entire value chain – from conception, design and engineering to production and post-processing, right up to the finished part. Benefit from more than 30 years of experience in additive manufacturing and take advantage of our full portfolio of systems, consulting and services for the industrial 3D printing of orthopedic technology and instruments – all from a single source. Together with you and our highly effective network of partners, we can develop the solutions that you need for your own production to achieve a comprehensive portfolio of solutions.
Additive Manufacturing for Laboratories and Medical Equipment
Developed and Produced More Quickly, More Flexibly and Cost-Efficient
For laboratory equipment and medical imaging systems (also known as imaging diagnostics or just imaging, e.g. CT, MRT or X-ray equipment), additive manufacturing is a production technology that offers new opportunities to optimize both the product and the manufacturing costs.
Many medical devices and parts for laboratory equipment are complex niche products that are only produced in small series. Conventional production often requires expensive tools whose cost then needs to be added to the products. By contrast, additive manufacturing works without any tools, enabling parts to be manufactured in smaller series, right down to a batch size of one.
The production process is based on the CAD data of the parts. This technology provides freedom of design, as well as the option to integrate functionality directly into the part. The results include shorter time-to-market and a wide range of opportunities for product optimization.
Find out more here about which laboratory equipment parts and diagnostic imaging equipment can already be optimized with EOS 3D printing today, and which machines and materials are right for your application.
-
Tool-free production and reduced assembly costs
-
Flexible design and functional integration
-
Faster development cycles & time-to-market
3 Assembly Components Instead of 32 – the Washing Rotor by Hettich
The centrifuge manufacturers Hettich significantly improved the cost-efficiency of their series production with additive manufacturing and are fully taking advantage of 3D printing. Hettich invented and patented a new type of centrifuge that allows blood components to be sedimented and separated in a single device.

To show the video you have to accept marketing cookies.
The ROTOMAT consists of a drum motor with six containers and collection trays. The containers have an elaborate geometry and are placed under high rotational speeds, with accelerations of up to 1,200 times the acceleration due to gravity. Centrifuges use the centrifugal force to separate mixtures into their components. Typical applications include preparing blood samples or performing a blood panel. When manufactured conventionally, each washing rotor consists of 32 separate parts that need to be assembled. This requires complex tools and a time-consuming assembly process, especially since the stainless steel injectors need to be painstakingly deburred.
Switching to EOS technology paid off for Hettich – with outstanding numbers
- The washing rotor was redesigned and now consists of 3 assembly parts instead of 32 – with improved functionality.
- The containers are manufactured tool-free at lower production costs.
- Small series productions and regional adjustments can easily be implemented.
- Assembly no longer requires tools, and the time-consuming deburring step is completely eliminated.
Complex Structures, Delicate Details, Functional Integration
Additive manufacturing opens up a wide range of opportunities for medical imaging equipment. Highly complex, individual geometries can be implemented with the 3D printing process – including structures that would not be possible with conventional manufacturing. For example, parts for computed tomography or magnetic resonance tomography systems or X-ray equipment can be improved and manufactured more cost-efficiently.

3D Printer for Anti-Scatter Grids
X-ray grids (anti-scatter grids) capture the X-rays deflected by the patient’s body tissue before they reach the film or imaging plate. This improves the contrast and accuracy of X-ray images. Making X-ray grids conventionally is extremely difficult and time-consuming, and therefore cost-intensive.
But 3D printing allows the sophisticated design to be manufactured according to a new and optimized approach. The EOS M 290 system combined with the EOS material Tungsten W1 is the first and only solution to the demanding challenge of manufacturing X-ray grids currently available on the market. It comes with a great advantage and has a more attractive cost per unit than manufacturing by conventional methods.

Additive Manufacturing for a Perfect Fit
3D Printing Production of Prosthetics and Orthotics
We offer systems, materials and processes, software, and services – anything that you need for the 3D printing of prostheses and orthoses. With our solutions, orthopedic technicians and companies benefit from reliable data, stable processes, and decades of market experience.
Why 3D printing? With conventional manufacturing processes, the model needs to be manually adapted for each patient. The large number of steps involved means that production is expensive and time-consuming.
In terms of customization and cost-efficiency, conventional production methods like casting, molding, modeling and milling quickly reach their limits.
Additive manufacturing offers maximum benefits for patients and manufacturers. The manufacturing process is based on individual scan data for each patient, meaning that 3D-printed prostheses and orthoses are optimally tailored to the anatomy and requirements of the wearer.
"Orthoses and prostheses help their wearers to achieve better mobility. But every wearer has a different anatomy, usage and therapeutic needs. EOS 3D printing solutions successfully combine rapid manufacturing processes and optimal comfort for the wearer."






Advantages of Additive Manufacturing for Orthoses and Prostheses
- Virtually limitless customization potential in terms of design and functionality
- Optimal comfort for the wearer: lightweight and stable design despite complex structures
- Sustainable – less material consumption, since any leftover material can be reused
- Any necessary adjustments can be implemented quickly, for example with children who are still growing
- Increased comfort thanks to functional integration for more elasticity, breathable designs, etc.
- Fully digital process from scanning to the finished product, for faster availability
Manufacturing Prosthetic Feet on Demand
Mecuris offers a digital platform for patients, doctors, orthopedic workshops and medical suppliers. Using the data submitted to them, they provide contract manufacturing of 3D printed prostheses on EOS systems.
Customized prosthetic feet allow natural walking. The additive manufacturing process significantly reduces the lead time, achieves maximum comfort and enables customized design.

To show the video you have to accept marketing cookies.
Paralympics Cyclist Denise Schindler
Optimal Prostheses Thanks to 3D Printing by EOS and Mecuris
To show the video you have to accept marketing cookies.
Perfectly Fitting Orthoses for Children
The British start-up company Andiamo uses EOS systems to make custom-fitting orthoses for children. Traditionally, orthoses are made from plaster impressions. This process is slow and resource-intensive and offers little room for customization.
Some patients, especially young patients who are still growing, have to undergo this procedure repeatedly. Waiting times can last up to six months – for an orthosis that might not even fit by the time it’s ready. Additive manufacturing reduces the waiting period to a minimum. Using a 3D body scan, a precise and perfectly fitting orthosis is manufactured and delivered within a week.
