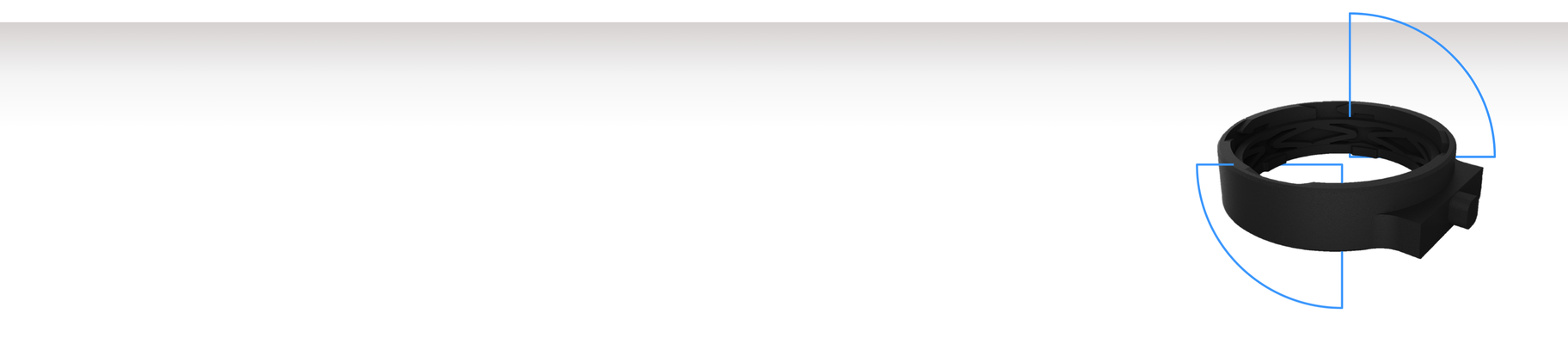
Housings
Complex Design and Flexible Production
Having a stable housing protects the interior. Robust cases are often essential, especially for sensitive electronics. They need to be strong and properly sealed, while also fitting as closely as possible, and they need to be manufactured quickly enough to achieve short production cycles. However, with the injection molding process, manufacturing housings with these properties is only viable in very large series productions.
Industrial 3D printing offers a cost-efficient alternative for the small and medium series production of plastic housings. Whether made from materials with insulating or especially favorable dissipation properties, the additive manufacturing of housings is characterized by cost efficiency, design freedom and functional integration potential.
Whether you want to make prototypes, pilot series or small series productions of housings, additive manufacturing opens up a great deal of potential – not the least of which being lower production costs.
Advantages of 3D Printed Housings
- Integrate functionalities to reduce number of components
- Reduced time-to-market
- Economically attractive manufacturing process
- Produce stable end-use components
3D Printed Camera Housing for Outdoor Use
The challenge was to manufacture a low number of units of a robust camera holder with a complex design. The housing needed to be flexible enough to hold six cameras. At the same time, the production process needed to be open to support later design iterations without causing issues.
Thanks to EOS technology, a product design was successfully realized that would previously have been impossible.
The partnership with Freedom360 allowed design changes to be made rapidly. Midwest Prototyping were able to implement cost-effective production in small quantities.
Canto
The developed underwater dive lamp is smaller, lighter and more robust than anything else on the market. Canto succeeded in solving this challenge with a FORMIGA P 110 Velocis using PA 2200 material.
The internal system of the additive manufactured lamp connection, which features a spring latching mechanism, is produced in a single piece. This allowed the number of assembly parts to be reduced from 3 to 1. Weighing just 580 grams, the lamp is setting new standards. As an added benefit, Canto Ing. GmbH were spared the need to manufacture an expensive injection molding tool, which would have cost up to € 35,000.
