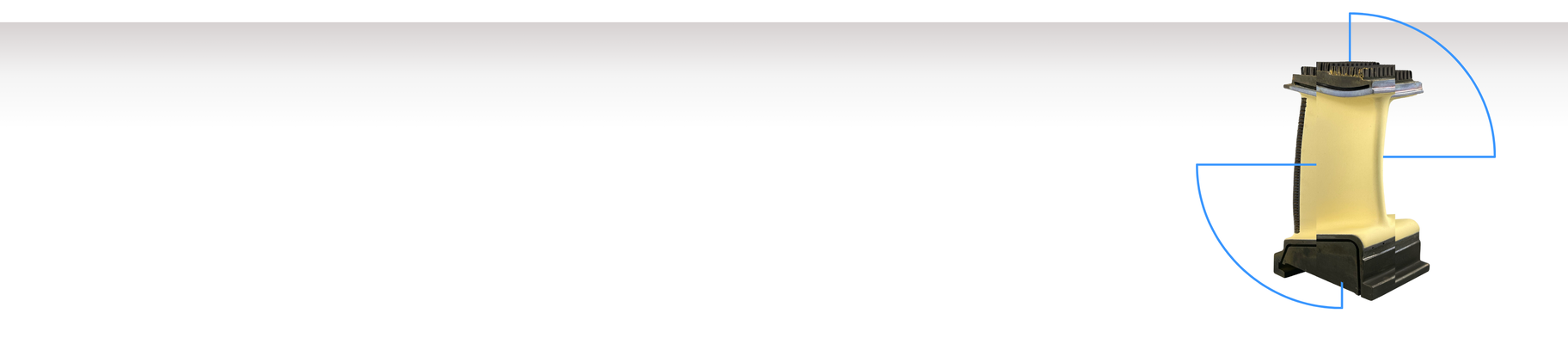
Turbomachinery & Turbines
Additive Part Manufacturing for Turbomachinery
Turbomachinery is indispensable for energy generation. Its high-performance parts feature complex, high-tech designs that need to be more and more robust and powerful as the demand for energy increases. In addition, turbomachinery parts need to be resistant and reliable – even at temperatures beyond the melting point.
The 3D metal printing (DMLS) offers the right technological foundations for implementing an optimized cooling strategy, among other things. Parts can be designed and made to transport and apply energy with increasingly precise focus. Innovative repair processes, for example, are revolutionizing the efficiency of turbomachinery parts by building at worn areas directly on the original part.
Advantages of 3D Printed Turbine Parts
SUCCESS STORY
Material Solutions & Siemens - Innovative Project Outstanding Results
The collaboration between Siemens, Material Solutions and EOS demonstrates that 3D metal printing is a reliable and proven technology viable even for “moving” applications, without any compromise. In focus: developing a new turbine blade. The part was developed together with Siemens NX, built on EOS systems and produced by Material Solutions.
- Performance increased to 13 000 rpm
- 75 % shorter development time & 50 % quicker lead time
- Can be used with ambient temperatures of up to 1 250 °C
Blades, fuel injectors, burners and combustion chambers, cladding, seals and housings: when manufacturing parts for the energy sector, functional integration and heat resistance are the decisive factors of longevity and process selection. For these factors, industrial 3D printing opens up opportunities beyond the reach of conventional manufacturing processes. The applications range from 3D-printed turbine blades to innovative repair solutions. Find out more on this page about how we’ve broken new ground in turbomachinery together with our customers.
SUCCESS STORY
Siemens - Burner Fronts with Functional Integration
Siemens relies on an EOS system to manufacture burner fronts featuring functional integration – redesigned with Siemens NX and manufactured in series on an EOS M 400-4 from EOS NickelAlloy HX.
The part is manufactured as a single piece and no longer has 13 different components Since less material is used, the part is considerably lighter. The lead time is reduced from 26 weeks to 3 weeks. Reduced heating of the metal extends the service life of the part
SUCCESS STORY
Siemens - Optimized Maintenance Management Based on 3D Printing
Downtime caused by repairs and maintenance work is a huge cost factor in large-scale energy generation plants. Especially for parts with high complexity and integrated channels, the hybrid repair process based on DMLS opens up unique opportunities to save time and costs. How does it work? Areas that experience wear are reconstructed directly on the original part. This has far-reaching advantages:
- No additional welding steps are required
- Improved quality of the connection between the reconstructed area and the original part
- The alignment of internal structures is preserved
A Demanding Task and a Smart Solution
Thanks to a customized EOS system, Siemens found success with a precise and fast maintenance process for burner tips subject to high thermal stress in gas turbines. The repairs are performed by building directly onto the worn material, saving time and cost.
- Repair times were reduced by 90 %
- Repair process became significantly more streamlined
- Technical improvements can be incorporated during repairs
Euro-K
The new burner is able to use gaseous and liquid fuels equally effectively. The new, optimized geometry also allows the use of liquid fuels that are classified as difficult to burn, such as fusel oils that are created from the distillation of alcohol. Another positive effect is that the burner’s innovative design allowed the size of the combustion chamber to be reduced by 20%.

Everything You Need for Turbomachinery Parts From a Single Source
We offer robust systems with repeatable part quality and a wide portfolio of materials, capable of handling diverse applications, including those involving high temperatures. To complement this, we also offer tools and software for comprehensive quality monitoring and a consulting department to take care of your needs.