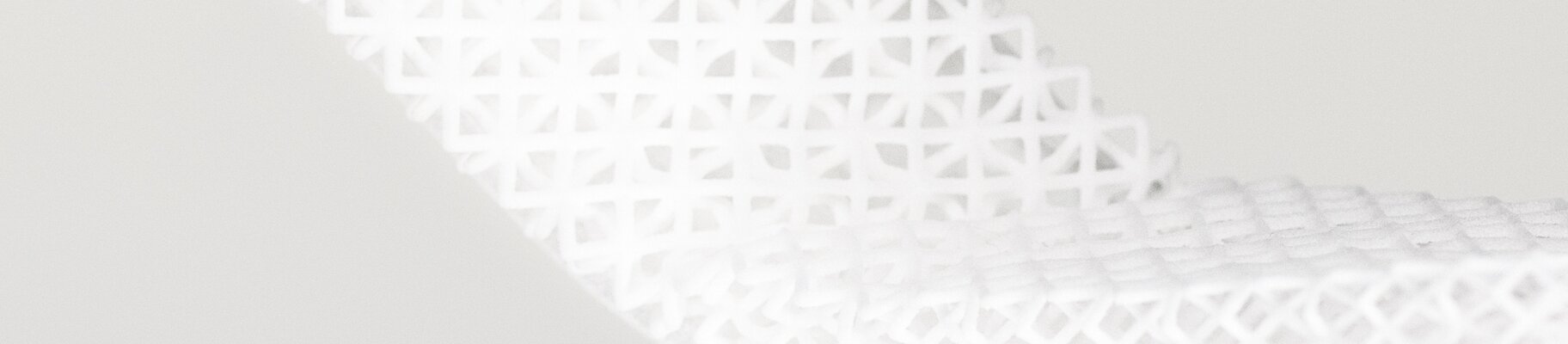
EOS Digital Foam
Discover EOS Digital Foam, a revolutionary 3D printing technology using flexible polymer materials for personalized lightweight products.
Additive Manufacturing With 3D Printed Foam
Complete, end-to-end industrial 3D printing process with flexible, durable polymer materials
Foam has found its way into polymer industrial 3D printing with the revolutionary EOS Digital Foam process. By unlocking the capability to produce flexible and adaptable polymer products with additive manufacturing, organizations interested in evolving their product lines can utilize the customizable technology that is being leveraged by cutting-edge manufacturers in sports manufacturing and consumer goods industries alike.
What exactly is Digital Foam?
Digital Foam is not a product, it is an approach to 3D printing foam-like products. It revolutionizes the intricate process of 3D printing by harnessing the potential of highly adaptable polymer materials such as TPU or PEBA. This cutting-edge technology enables precise customization to every voxel, resulting in unparalleled levels of comfort, safety, and performance.
Digital Foam breathes new life into mature products, while also creating entirely new product offerings from athletic shoes, to orthotics, to protective gear and medical products. Manufacturers can “dial-in” exactly the performance or features they need to deliver product differentiation as well as provide mass customized product offerings.
Underpinning Digital Foam is the EOS patent relating to any generatively 3D printed object which has a flexible grid-like structure or matrix (i.e., lattice), composed of open cells that are joined together in groups of differing characteristics. Described in basic terms, this covers any varying 3D printed lattice structures morphing into each other.
MyBauer REAKT Helmet
The REAKT helmet project with the global leader in hockey equipment innovation began with a desire to integrate customization and enhanced comfort and breathability into their protective equipment portfolio.


Bauer investigated how to leverage and incorporate AM into business because of industrial 3D printing’s customization capabilities, and found that EOS and our patented Digital Foam approach to printing polymers gave them a distinct advantage.
The MyBauer helmet production process begins by scanning a player’s head, then creating a digital file. Using Selective Laser Sintering (SLS) and in this case, more specifically an >EOS P 396 system, a helmet insert – created to fit perfectly to its wearer – is 3D printed in Digital Foam which involves a complex, varying lattice that is both personalized for the wearer for improved comfort, but also lighter weight – at 580 grams, and greater breathability. Once printed the helmet inserts are colored, finished and redyed for final assembly.
Learn more about the MyBauer REAKT helmet project by watching their production story with collaborating partners.
Wilson Airless Prototype Basketball
Wilson Sporting Goods, the world’s leading manufacturer of high-performance sports equipment, apparel, footwear and accessories, dared to do what no brand had done before – build an airless basketball.


The first-of-its-kind 3D printed ball is truly playable, nearly fitting the performance specifications of a regulation basketball, including its weight, size and rebound (bounce). The ball, however, does not need to be inflated because it is comprised of black, see-through lattice with eight panel-like “lobes.” By leveraging Digital Foam and our network of partners, Wilson was able to successfully produce the Wilson Airless Prototype, with customized Digital Foam material, a digitally optimized lattice structure, and industrial 3D printing solutions such as the EOS P 396.
The Airless Prototype Basketball innovation sets the stage for more sports equipment innovation, changing the game for traditional sports manufacturing, Learn more about the project by watching Wilson’s Airless Basketball prototype journey.
Biomechanical Podiatry by Doc Sols
Doc Sols software utilises lattice structures in 3D printed digital foam (TPU) due to its advanced geometric kernel which uses voxels, three dimensional pixels to represent objects of unlimited complexity.


Podiatry is a field where inspiration and innovation converge to create customized end-user products. By integrating AI, a platform-based business model, and additive manufacturing technology, it offers medical applications that significantly enhance people’s lives.
Doc Sols, an Australian company, specializes in producing 3D custom foot orthotics. They leverage cutting-edge artificial intelligence to analyze foot data, making the diagnosis and design of custom orthotics easier than ever. Since every foot is unique, their approach addresses issues like lack of support or improper loading that cause pain.
Their software uses lattice structures in 3D-printed digital foam (TPU), thanks to an advanced geometric kernel that employs voxels—three-dimensional pixels—to represent objects of unlimited complexity. This lattice mimics the structure of cortical bones, helping the foot withstand daily stresses. No other device in the world offers this capability.
The Digital Foam Architects Network
Digital Foam applications typically have complex requirements, requiring multiple disciplines to ensure success. The Digital Foam Architects network formalizes a standing alliance of AM experts ready to bring ideas to production – design software, materials, and the various AM hardware elements, from printing to post-processing and colorization. The Digital Foam Architects network is another chapter in the maturation of this approach by coalescing the required AM expertise to streamline Digital Foam products. To learn more about the Digital Foam Architects network, read our recent alliance announcement.