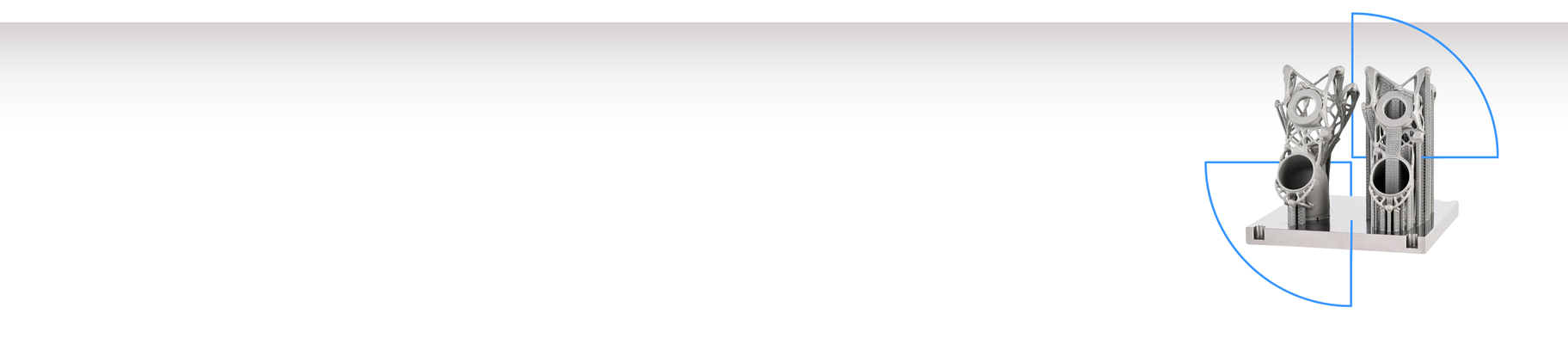
Less Support -
AM for Sustainability
SEPTEMBER 16, 2021 | Reading time: 5 min | Author: Ho Kei-Leong
Additive Manufacturing (AM), also known as Industrial 3D printing, is often considered sustainable for material efficiency, reduced energy consumption, localized production, customization and design optimization, recyclability, and reduced tooling requirements among others. While AM inherently has these sustainability benefits, many challenges remain.
In the world of DMLS ("Direct Metal Laser Melting"), the need for support structures during the printing process remains one of the biggest challenges. With the help of advanced thermal management, a reduction in support structures can be made possible by adjusting the laser power. Support structures are essential to prevent overhanging or intricate features from deforming or collapsing when the metal layers are applied. While the support structures are critical to a successful printing process, they also lead to inefficiencies and waste in the form of material, post-processing and increased energy consumption.
To address these challenges, researchers and manufacturers are working to develop more efficient support structures to optimize the overall printing process. One of the most efficient and innovative approaches is the implementation of real-time monitoring and control systems to help identify and address issues during the printing process, thereby creating a closed loop system for real time adjustments.
EOS Smart Fusion
EOS Smart Fusion is a closed loop feedback control solution assisted by real-time monitoring and adaptive process adjustments to assist the printing of parts with minimal supports. It was developed as an intelligent thermal management method, tailored for manufacturers to allow printing of components with minimal support. This leads to a reduction in build time, post-processing time and material wastage. Based upon an optical tomography pairing of hardware and software for process insights via a high resolution near infrared camera, Smart Fusion records and measures real time energy input to facilitate a more accurate analysis of individual build layers.
In order to test the premise of Smart Fusion against our baseline build along with another 3rd party software available in the market, a study was undertaken with our research partner, A*STAR’s Advanced Remanufacturing and Technology Center (ARTC), based in Singapore. The goal was to provide conclusive data in quantifying the improvements made. Validation of sustainability impact and labelling additive manufacturing as the future of manufacturing can only be achieved through empirical data.

The methodology begins by technology scout and research in the marketplace of the various support-free printing software. Stainless steel 316L material was chosen for this study as this material is known for requiring strong support structures to successfully print the components.* Angled coupons and a demonstrative closed impeller were then built and compared across various approaches, including quantifying dimensional accuracy. The impeller was sectioned to capture micrographs of the overhang while angled coupons were sectioned to assess surface roughness and porosity. Finally, a comparative carbon emission analysis was performed using the EOS Carbon Calculator to examine the differences between the different approaches. All results are highlighted in the following table and illustration.
EOS Standard |
EOS with Smart Fusion |
OEM with Software A |
|
---|---|---|---|
Angled Coupon Overhang | xx | xxx | x |
Dimensional Accuracy | xx | xxx | x |
Surface Roughness | xx | xxx | x |
Porosity # | xx | xxx | x |
Carbon Footprint | x | xxx | No data |
Print Time | x | xxx | xx |
Support Volume | x | xxx | xx |
The EOS M 290 was used as a baseline to compare and evaluate 3 different approaches: a standard print, a standard print with Smart Fusion and a different OEM machine integrated with a commercially available support reduction 3rd party software termed as “software A” in this study. Smart Fusion surpasses both the commercially available software and the conventionally printed impeller in support volume utilization, successfully building the part right first time.
Software A - based print necessitated multiple attempts, requiring at least 4 trials before achieving success in printing the impeller. With Smart Fusion the part was built in significantly shorter overall processing time, requiring least volume of supports and superior dimensional accuracy (see Figure X). Comparison of angled coupons built with Smart Fusion showed better surface roughness and reduced porosity (see Figure Y). Remarkably, Smart Fusion enabled the lowest overhang angle that closely resembled the coupon CAD model.
The result of the comparative evaluation quantifies and highlights the substantial benefits of EOS Smart Fusion. Compared to conventional metal printing, there is a 38% reduction in support volume and a whopping 62% reduction in print time equating to almost an entire day. The cost of producing each part is subsequently reduced by 76%! In addition, Smart Fusion answers the call for sustainability and reduction of carbon footprint with a 62% reduction in CO2 emissions during printing (from 29 to 11 kgCO2-eq) and a substantial 84% reduction in emissions during post-processing (from 187 to 30 kgCO2-eq).
With its intelligent heat management, Smart Fusion offers software that makes it possible to change the AM residual stress of metals. By minimizing material loss and shortening processing time, it is possible to achieve cost savings and make production more sustainable. Our goal is to collaborate with our customers and partners to test, implement and optimize this solution, providing them with a competitive advantage to fully harness the benefits of AM.
As technology continues to evolve and adoption grows, EOS will continue to develop cutting-edge AM solutions with sustainability as the primary focus, tailored to market needs to shape the future of manufacturing.
Interested to find out more? Don’t hesitate to reach out for an in-depth discussion on how EOS and Smart Fusion can empower you to realize sustainable manufacturing through additive manufacturing!
* Stainless Steel 316L is currently in the test phase with Smart Fusion. As a result, no standardized process is currently available.
