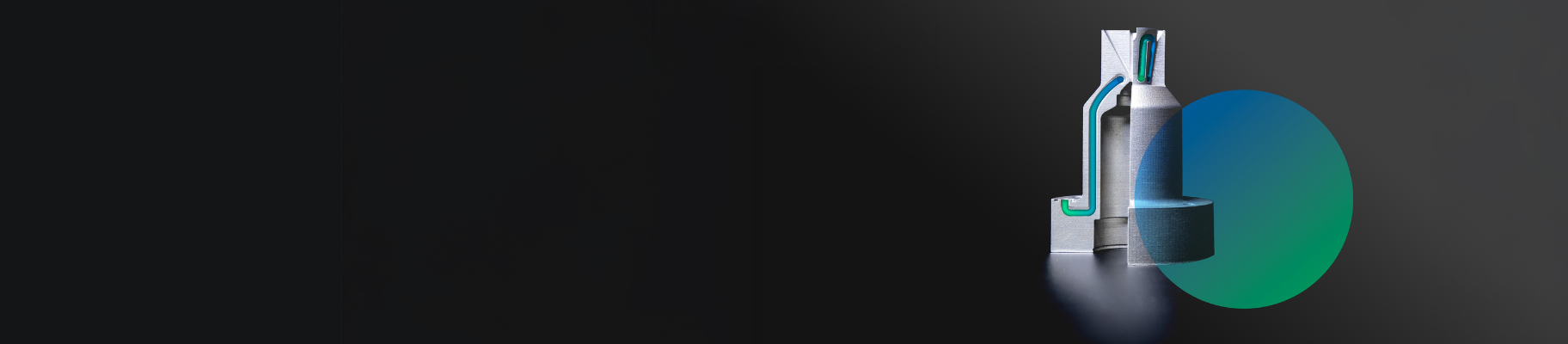
The Strategic Advantage of
Additive Manufacturing for Tooling
March 27, 2025 | Reading time: 8 min
Manufacturers face persistent challenges in tooling that directly impact production efficiency, part quality, and bottom-line results. Thermal management issues create production bottlenecks. Complex geometries require design compromises. And long lead times for traditional tooling delay product launches and limit responsiveness to market changes. As these challenges intensify, additive manufacturing (AM) has emerged as a compelling alternative that addresses these fundamental pain points while opening new possibilities for performance optimization.
The Case for Additive Manufacturing in Tooling
Traditional tooling manufacturing methods have served industries well for decades, but they come with inherent limitations. Complex geometries require multiple machining steps, cooling channels are restricted to straight-line designs, and lead times can stretch into months. AM addresses these pain points directly:
- Reduced Lead Times: While conventional tooling can require lengthy setup times, additively manufactured tools can often be designed, printed, and post-processed in just weeks. This dramatic reduction enables faster market responsiveness and more agile product development cycles.
- Enhanced Performance Through Design Freedom: AM allows for previously impossible geometries, including conformal cooling channels that follow the exact contour of the part. This results in more uniform cooling, reduced cycle times (often by 20-40%), and improved part quality with fewer defects.
- Cost-Effective Iteration: Making design changes to traditional tooling is expensive and time-consuming. With AM, modifications can be implemented digitally and a new tool printed without the high costs associated with re-machining or creating new molds.
Overcoming Traditional Tooling Challenges
Manufacturers across industries face common tooling challenges that AM is uniquely positioned to solve:
- Thermal Management: Consider high-pressure die casting (HPDC), where shot blocks face significant thermal fatigue issues. Traditional straight cooling channels often create uneven cooling, leading to hot spots, premature tool failure, and casting defects. With AM, cooling channels can conform precisely to where thermal imbalances occur, following complex contours impossible to machine conventionally. This targeted cooling approach extends tool life dramatically while improving casting quality and consistency.
- Tool Longevity: High-wear areas in tooling have traditionally created maintenance headaches and production bottlenecks. The combination of high-performance tooling steels and the design freedom only AM can provide allow for exceptional durability and performance under demanding conditions, extending tool life significantly
- Complex Geometries: As product designs become increasingly complex, traditional manufacturing methods struggle to create tools that can produce these intricate shapes efficiently. AM removes these constraints, enabling tooling that perfectly matches product requirements without design compromises.
Powering Additive Manufacturing for Tooling
EOS offers a range of industrial 3D printing systems designed to meet the diverse needs of tooling manufacturers. Our metal systems, using Laser Powder Bed Fusion (LPBF) technology, provide the precision, repeatability, and material flexibility required for creating high-performance tooling. Whether you need a compact system for smaller tools or a large-format system for high-volume production, EOS has a solution to empower your AM journey. Our systems are known for their robust build quality, advanced process monitoring capabilities, and open architecture, allowing for optimization to meet even the most complex application requirements.
The Material Advantage: EOS Tool Steel
While material choices are always a core question, in tooling it’s even more important, as parts have to endure wear and tear, often under extreme conditions. That’s why EOS has heavily invested in its tooling line-up, and that includes a range of materials specifically tailored to tooling applications. One example of that is EOS ToolSteel 1.2709, which offers superior performance for demanding tooling applications. This material is the preferred choice for many leading manufacturers due to its exceptional characteristics:
- Outstanding mechanical characteristics.
- Easy post-processing with excellent machinability.
- Heat-treatable to 57 HRC under vacuum or inert gas atmosphere.
- Versatile finishing options, including machining, spark-erosion, welding, shot-peening, polishing, and coating.
- Superior performance in high-pressure, high-temperature applications.
Industry Leaders Embrace AM Tooling
For every new process, decision-makers have to weigh initial costs or other changes against expected benefits like cost savings. And while it’s worth considering the benefits and drawbacks of both traditional and AM manufacturing for tooling, there’s no denying that it's already happening across industries with remarkable results.
AarKel: A Pioneer in AM Tooling
AarKel, a renowned North American tooling manufacturer with over 40 years of experience, recognized the limitations of traditional tooling methods, particularly in addressing challenges related to thermal management and tool longevity. Seeking innovative solutions, they turned to EOS and AM to push the boundaries of tooling performance.
"At AarKel, we combine the advanced capabilities of EOS machines with our proprietary heat treatment recipes and parameter optimizations. We have data on multiple additively manufactured components with shot counts exceeding one hundred thousand—surpassing the typical tool life of traditionally manufactured components in high-wear areas. We truly believe that additive manufacturing represents the future of tooling."
Vilas Dulipeta, Manager of the Additive Manufacturing Group at AarKel
This real-world validation underscores what many early adopters have discovered: AM tooling doesn't just match conventional tooling performance — it often exceeds it, particularly in challenging applications.

Getting Started With AM Tooling
Ready to explore how additive manufacturing can transform your tooling operations? EOS offers comprehensive resources to help you navigate the transition:
- Learn about part screening, AI design optimization, simulation insights and implementation strategies in our Digital Tooling Session.
- Connect with our materials experts to understand how EOS MaragingSteel MS1 or other materials can address your specific tooling challenges.
The future of manufacturing demands more than incremental improvements - it requires practical solutions to persistent challenges. AM for tooling delivers tangible benefits - shorter lead times, enhanced performance, and competitive advantages that directly impact your production efficiency and bottom line. Discover how AM tooling can enhance your manufacturing processes - your competitors already are.