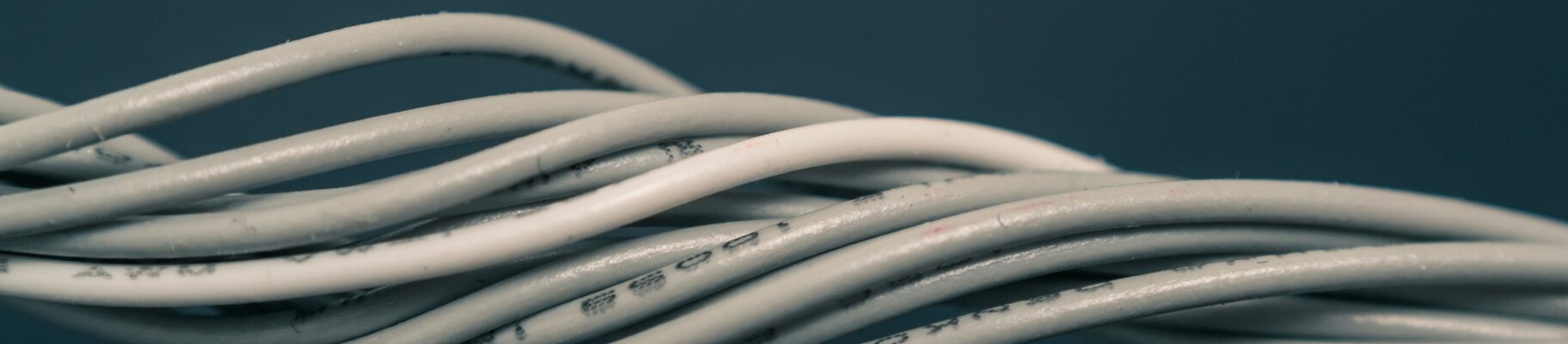
Precision & Stability: The Future of Electrical Connectors made possible by FDR 3D Printing
WAGO | Case Study
Achieving Excellence
- Rapid delivery with components available in days, not weeks
- Top-notch quality, almost indistinguishable from the final product
- Streamlined efficiency with minimal post-processing required
- Detail resolution fulfills the requirements of the
prototype's laboratory test
Without electricity, almost nothing works in our society and economy – the power lines in houses, factories, ships, trains, etc. are the lifelines of our time. In order for the electrons to transport their energy, they must reach the right place via cables. This requires reliable connection components, such as those manufactured by WAGO in East Westphalia. In reference to the Californian IT stronghold Silicon Valley, the electronics cluster there is also called "Terminal Valley". And rightly so, as WAGO proves: In the field of additive manufacturing (AM), prototype construction uses a high-resolution process for connection technology prototype manufacturing, so-called Fine Detail Resolution (FDR). In this way, WAGO was able to prototype the spring clamps for a new product on the EOS FORMIGA P 110 FDR using PA 1101 very quickly and accurately – and thus successfully shorten the time to market for a new electrical junction and distribution box.

"Humans need models. If you want to make rapid progress, there's no way around industrial 3D printing. It's our workhorse. Regular Selective Laser Sintering has already impressed us, but FDR has taken it up a notch in terms of fineness, precision, and speed."
Olaf Zoschke | Head of Prototype Construction WAGO GmbH & Co. KG
Challenge
Connecting two electrical conductors may sound simple at first, but in detail it places high demands on innovation, function, safety and quality. Where electricity flows, there are rightly accurate regulations. Connections must meet practical, factual and legal safety requirements: "A cable must not simply slip out of the contact point, even under load," explains Olaf Zoschke, Head of Prototype Construction at WAGO GmbH & Co. KG. "In addition, the contact contour must be of appropriate quality. If this were not guaranteed, personal and property damage could occur." He heads the prototype construction at WAGO: With his seven-member team, he creates design and functional prototypes as well as test samples that must pass functional and safety tests in internal and external laboratories; no new product may be sold before that.
Accordingly, the safety tests for products developed by WAGO and its market companions are extensive and frequent. Several challenges must be mastered: Whether at the meter station in the house or in the control cabinet in the railcar, the space for electrical distributions is getting smaller and smaller. At the same time, there is less and less time available to develop, test, and bring corresponding products to market. "To be fast, you can't get around additive manufacturing," Olaf Zoschke sums it up. In addition, the samples must correspond as closely as possible to the final series product – because they should not only convince test engineers, but also specialist retailers and other buyers.
The design of the cable strain relief proved to be particularly challenging in the development of a new junction box with as little installation space as possible: If a conductor is inserted into the socket, it must snap securely into place. This happens via a clamping mechanism. This locks into place via an interlocking gear. Any tensile forces on the conductor must be absorbed by this fixation at its insulation. The contact itself must not be strained. To meet the size requirements, the gears applied to the tabs must also be as small as possible. At the same time, a high degree of stability is required to comply with the relevant safety regulations. In series production, such a requirement catalog can be implemented because the costs for traditional processes can be spread over large quantities. But in prototype construction?
Precise & Fast
3D printing enabled WAGO to develop a fully functional junction box to market maturity within a very short time.


Solution
"We naturally change the component during the development process in the course of initial tests and optimizations. Additive manufacturing is known to have an advantage here. Above all, however, we need certain batch sizes for the functional and laboratory tests. We are talking about ten to 50 pieces, which of course must be absolutely equivalent to each other. The high precision required for fine gearing, for example, was not possible until recently," explains Olaf Zoschke. Only FDR has made it possible to incorporate the advantages of industrial 3D printing into applications with very filigree components.
The fine-detail-resolution process for additive manufacturing with the help of the FORMIGA P 110 FDR is the perfect choice at this point: Due to the very small components, only a small building chamber is needed to produce the required quantities in one pass. This also creates a "perfect timing match" with the other parts of the prototypes. Depending on the requirements, these are produced using other processes, including coarser selective laser sintering (SLS). "For the larger part 1, for example, conventional SLS is sufficient, for the smaller part 2 we rely on FDR. SLS is faster than high-resolution 3D printing, but because of the part size, we get the samples in about the same time," explains Olaf Zoschke vividly.
The prototyping team determines in advance which process is to be used in each case: The decision for this as well as for the material is already made in CAD planning – depending on the later intended use. Ultimately, the decisive question is how the required quality can be sensibly delivered in the required quantity. Olaf Zoschke's team can thus specifically utilize the strengths of the individual processes and materials. "FDR is the golden mean of precision, high edge sharpness and functional integration; PA 1101 as a material is very suitable for this. There are prototyping methods that are even more accurate. However, functional integration is missing there, for example. Standard SLS would be faster, but it is not as accurate," adds the head of prototype construction.
Results
And this high-resolution golden mean of 3D printing processes has led to the desired goal: WAGO was able to successfully produce the samples of the gears and plates – within the desired time, within the required tolerances, and in the required quantities. In this way, a durable component has been created that is in no way inferior to the later series product in terms of longevity. The production and post-processing took only about two days; other procedures require one to two weeks. Speaking of post-processing: Due to the high resolution of the FDR process for additive manufacturing, only little work on the component was necessary afterwards.
Olaf Zoschke confirms this: "The EOS products always delivered very good quality even without FDR. We have always obtained impressive results via post-processing. These are even better with Fine Detail Resolution. We achieve an extremely good value for prototyping of about 80 percent of the quality of the later series component. This has also excited our product developers." Another reason for the superiority of the high-resolution technology in SLS lies in post-processing: The process also enables chemical smoothing of unevenness. This leads to slight "blurring" and is therefore not quite as precise as the production by FDR.
In this way, the WAGO component also received the necessary product properties for the sample tests: The delicate lugs and their teeth provide the required strength. At the same time, they are manufactured to such a high quality that they interlock seamlessly and thus robustly – the hooking leads to the required conductor clamping force. And multiple internal and external tests have proven that if an additively manufactured component lasts, it will also last in series production. The innovative FDR process has thus kept its promise: to further increase the precision and speed of industrial 3D printing, with fully integrated functionality.
Robust & Reliable
3D printing can deliver top-notch quality, nearly indistinguishable from the final product
"The EOS products always delivered very good quality even without FDR. We have always obtained impressive results via post-processing. These are even better with Fine Detail Resolution. We achieve an extremely good value for prototyping of about 80 percent of the quality of the later series component. This has also excited our product developers."
Olaf Zoschke | Head of Prototype Construction WAGO GmbH & Co. KG
EOS Case Studies
Explore three decades of pioneering 3D printing excellence with EOS