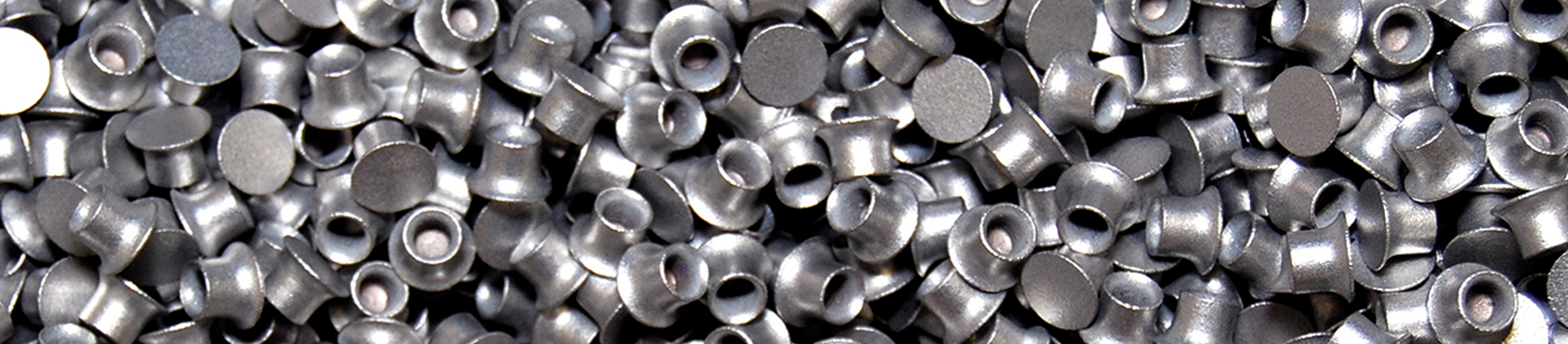
From Bottlenecks to Breakthroughs: Atlas Copco’s 3D Printing Journey
Atlas Copco | Case Study
Enhancing Production Efficiency
- 92 % lead time reduction from 6-12 weeks to just 3-4 days
- 30 % production cost savings attributed to the elimination of external supplier expenses and reduced labor hours
- Material waste reduction from approx. 7 % to near zero
- Enhanced agility in responding to unplanned orders and urgent customer requirements
Long lead times, supply chain disruptions, and rising production costs are common challenges in modern manufacturing. Traditional methods often struggle to keep up with the growing demand for flexibility, speed, and efficiency. For companies relying on outsourced components, delays and inefficiencies can lead to costly setbacks and lost opportunities.
Atlas Copco, a leader in industrial solutions, faced these very challenges with the production of its rivet delivery bowl—an essential component in self-piercing riveting systems used in the automotive industry. By adopting in-house additive manufacturing (AM), the company not only overcame these obstacles but also unlocked significant cost savings, reduced waste, and dramatically shortened lead times. Using the EOS P 396 and PA 2200 polymer material, Atlas Copco transformed its approach to production. This case study explores how additive manufacturing delivered measurable improvements and reshaped their manufacturing strategy.

"Working with EOS has given us a turnkey solution and helped us adapt our processes such that we are now in serial production with several components, are rapidly prototyping hundreds more, and achieved ROI in just 18 months."
Jason Edwards, Technical Manager at Atlas Copco
Challenge
Traditionally, Atlas Copco relied on external suppliers for components like the rivet delivery bowl, a critical part in their self-piercing riveting systems used extensively in the automotive sector. This dependency resulted in extended lead times of 6 to 12 weeks, increased production costs, and supply chain complexities. Additionally, the conventional manufacturing processes contributed to approximately 7% material waste, highlighting a need for a more sustainable solution.
“We wanted tighter control over our manufacturing that would lead to shorter lead times, lower costs, and the ability to rapidly prototype new products,” explained Working with EOS and Additive Minds has given us a turnkey solution, and helped us adapt our processes such that we are now in serial production with several components, are rapidly prototyping hundreds more, and achieved ROI in just 18 months,” explained Jason Edwards, Technical Manager at Atlas Copco.
Sort & Feed
3D printed bowl efficiently delivers rivets streamlining automated manufacturing processes


Solution
To address these challenges, Atlas Copco collaborated with EOS and its consultancy division, Additive Minds, to bring AM capabilities in-house. They selected the EOS P 396 3D printer, known for its flexibility and precision, and utilized the polymer material PA 2200 for manufacturing the rivet delivery bowl. This transition enabled Atlas Copco to streamline its supply chain, reduce reliance on third-party suppliers, and gain tighter control over production schedules. The in-house AM approach also facilitated rapid prototyping, allowing for swift iterations and design optimizations.
Results
The shift to in-house additive manufacturing delivered transformative results for Atlas Copco. One of the most significant improvements was the dramatic reduction in lead times. Previously, the production of the rivet delivery bowl required 6 to 12 weeks, largely due to reliance on external suppliers and the complexities of traditional manufacturing processes. With the implementation of the EOS P 396 3D printer, lead times were cut to just 3 to 4 days—a remarkable 92% reduction. This improvement allowed for faster response to production demands and greater flexibility in meeting urgent customer requirements.
Cost savings were another major outcome. By eliminating the need for external suppliers, reducing person-hours involved, and streamlining the overall production process, Atlas Copco achieved a 30% reduction in production costs. The efficiency of additive manufacturing minimized the expenses related to retooling, setup changes, and supply chain management. Additionally, the precision and reliability of the AM process significantly reduced material waste. Where traditional manufacturing methods resulted in approximately 7 % material waste, the new process brought this figure down to nearly zero. This reduction not only contributed to cost efficiency but also supported sustainability goals by minimizing resource consumption.
Through the adoption of additive manufacturing, Atlas Copco gained enhanced production agility, cost efficiency, and environmental benefits—demonstrating the powerful potential of AM in industrial applications. “AM has been transformative for us. We’re winning new contracts across the globe because we can supply directly, at lower cost and with short lead times. In EOS, we have a partner that has supported us throughout our transition, offers us rapid support, and continues to advise us on designing components to achieve the best result with our 3D printer,” concludes Jason Edwards, Technical Manager at Atlas Copco.
Efficient & Reliable
The move to in-house 3D printing has meant Atlas Copco needs fewer third-party components and is no longer constrained by supply chain lead times and transport delays.


"Additive manufacturing has been transformative for us. We’re winning new contracts across the globe because we can supply directly, at lower cost and with short lead times."
Jason Edwards, Technical Manager at Atlas Copco
EOS Case Studies
Explore three decades of pioneering 3D printing excellence with EOS