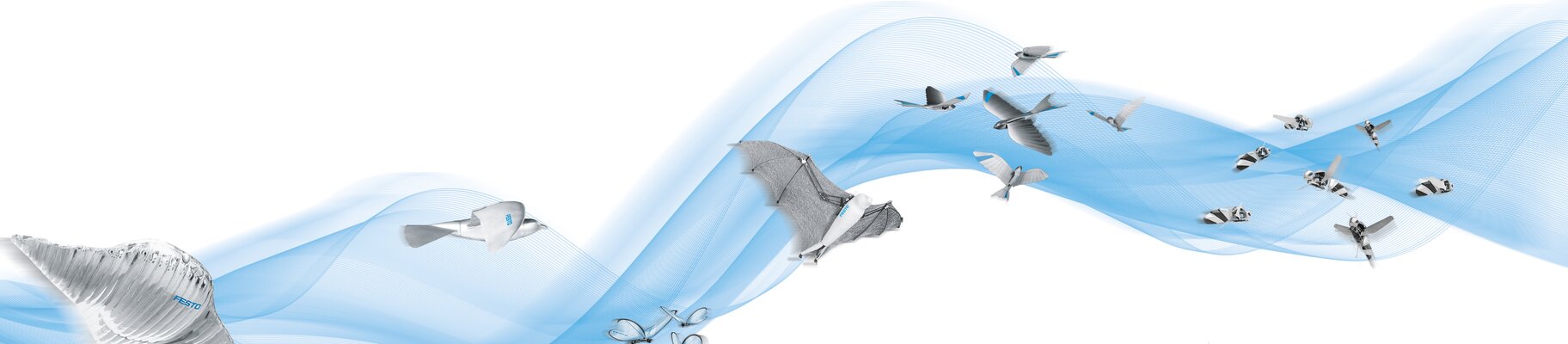
Bionic Bee Drones: The Future of Autonomous Swarm Technology Takes Flight
Festo | Case Study
Pioneering Lightweight Flight
- 75% reduced frame weight to just 3 grams
- Successful autonomous swarm flight with 20 units
- Rapid design iterations and short lead times
- Paved the way for more intricate lightweight designs in the future
In high-stakes applications like search and rescue, drone performance can mean the difference between success and failure. Lightweight, autonomous systems capable of navigating complex environments with precision are high in demand, pushing the boundaries of engineering and materials science. But what if the answer to the quest for new serial possibilities wasn’t a typical drone at all?
Enter the Bionic Bee — a micro aircraft inspired by nature, designed by Festo, and enabled by cutting-edge additive manufacturing (AM). This remarkable project isn’t just a showcase of biomimicry; it’s a demonstration of how advanced design and 3D printing revolutionize lightweight flight. Festo developed the concept, while 1zu1 and EOS provided the expertise and technology to turn an ambitious idea into a reality. The result: an ultra-light, agile swarm of robotic bees that redefine what’s possible in autonomous flight.

"Leveraging FDR technology has been a game-changer for the BionicBee. By pushing additive manufacturing to its limits, we were able to reduce our frame weight from 12 grams to just 3 grams — without compromising stability."
Mattias-Manuel Speckle | Head of Additive Manufacturing Prototyping at Festo
Challenge
Creating the BionicBee posed a unique challenge. With a wingspan of 240 millimeters and a weight of just 34 grams, the goal was to design a structure that balanced ultra-lightweight construction with durability and functionality. The bee’s body had to house a brushless motor, three servomotors, a battery, a gearbox, and several circuit boards to enable precise wing movement. Festo’s development team embraced AM to optimize the frame’s structure, but early prototypes often faced limitations in robustness or flexibility. Conventional selective laser sintering (SLS) systems couldn’t produce the fine, intricate geometries needed for the frame to perform under real-world conditions. Even the smallest differences in material behavior or manufacturing inconsistencies could have affected flight performance. Additionally, the tight timeline added further pressure to deliver results quickly and efficiently.
Solution
Festo turned to 1zu1 for production expertise, and 1zu1 selected the EOS FORMIGA P 110 FDR system to deliver the intricate, lightweight components required. By combining Festo’s bionic design approach with the FORMIGA P 110 FDR’s high-resolution capabilities, the team developed a frame that effectively balances minimal mass and structural strength. This setup also allowed Festo to iterate quickly and refine the bee’s delicate lattice structure, even under time constraints. As Philipp Schelling, Production Manager SLS at 1zu1explains, “The BionicBee demanded extremely fine features and consistent part performance in flight. EOS’ fine detail resolution (FDR) technology with the one-of-a-kind CO laser, which has an ultra-fine beam half the size of standard SLS systems, was ideal to meet those requirements and bring Festo’s vision to life.”
The use of PA 1101 — a tougher and more flexible polymer — ensured the lattice structure was both lightweight and durable, meeting the rigorous demands of autonomous flight. PA 1101 parts show high impact resistance and strain at break, maintaining constant mechanical properties over a wide temperature range. This renewable resource-based material offers superior performance compared to PA 12, including the ability to withstand the highest mechanical loads without splintering.
Festo further optimized the frame with algorithm-driven modeling, removing unnecessary material to achieve a dramatic weight reduction of 75 %. The team also implemented an automatic calibration function that tunes each BionicBee’s controller parameters after a short test flight, mitigating any remaining variations in material behavior. “We saw the BionicBee as the perfect challenge to showcase what FDR can do. This project highlights how precise, ultra-thin structures enabled by the FORMIGA P 110 FDR system can revolutionize lightweight design — even at larger part sizes,” says Philipp Schelling, Production Manager SLS at 1zu1.
Through close collaboration and an agile production process, 1zu1 delivered prototypes and components on a tight schedule. This collaborative approach enabled Festo to assemble and test the BionicBee’s frame in real time.
Results
The partnership between Festo, 1zu1, and EOS broke new ground for the design, manufacturing, and operation of autonomous flying objects. The optimized lattice structure reduced the frame’s weight, a key factor in extending flight duration and improving maneuverability. “By pushing AM to its limits, we were able to reduce our frame weight from 12 grams to just 3 grams — without compromising stability,” stated Mattias-Manuel Speckle, Head of Additive Manufacturing Prototyping at Festo. BionicBee’s flight capabilities were demonstrated by a synchronized swarm of 20 units, highlighting advanced localization, communication, and control systems. Meanwhile, AM accelerated innovation cycles by enabling rapid prototyping and on-demand production, significantly shortening development timelines. This successful collaboration has become a blueprint for future lightweight endeavors, underscoring the impact of functional design and high-resolution AM on achieving unprecedented levels of efficiency and performance.
Light & Agil
The BionicBee is the smallest flying object from the Festo Bionic Learning Network. It weighs about 34 grams, is 22 centimeters long, and has a wingspan of 24 centimeters.


"We saw the BionicBee as the perfect challenge to showcase what FDR can do. This project highlights how precise, ultra-thin structures enabled by the FORMIGA P 110 FDR system can revolutionize lightweight design — even at larger part sizes."
Philipp Schelling | Production Manager SLS at 1zu1
Natural & Autonomous
With the BionicBee the Festo team has developed a flying object that can fly in large numbers and completely autonomously in a swarm.


EOS Case Studies
Explore three decades of pioneering 3D printing excellence with EOS