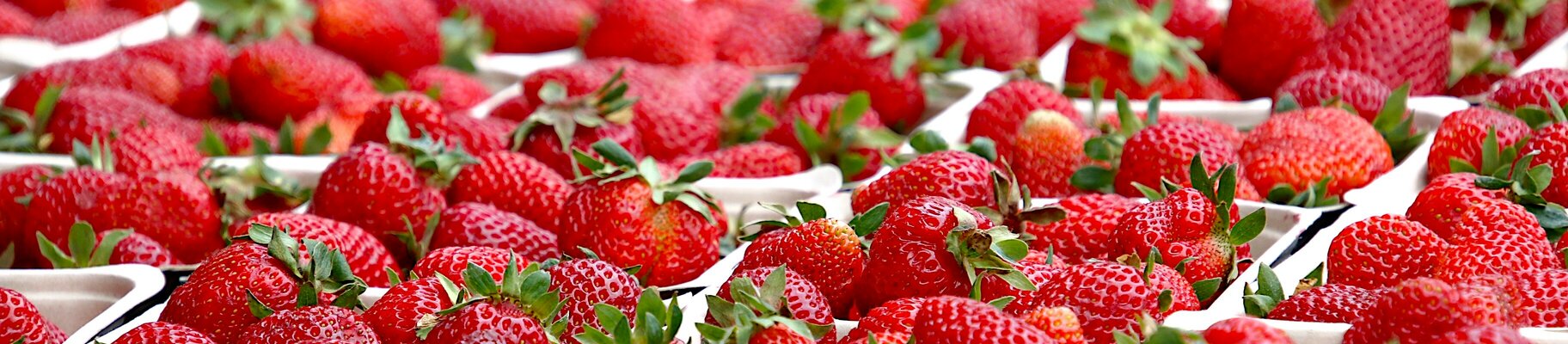
Manufacturing Redefined - Intelligent Automation of a 3D Printed Filling System
apc-tec | Case Study
Compliant Packaging
- 86% cost reduction
- Faster production with fewer components and shorter assembly times
- Regulatory compliance with (EU) 1935/2004, (EU) 10/2011, and GMP standards
- Improved reliability due to eliminating complex mechanical parts and reducing programming complexity
- Space-saving design for compact production environments
The food packaging industry is under constant pressure to innovate — balancing efficiency, cost reduction, and compliance with ever-stricter safety regulations. Traditional automation methods often rely on bulky, complex mechanical systems that require extensive maintenance and programming.
Even small tweaks in the production chain can translate to significant competitive advantages, and additive manufacturing (AM) with declared food-safe materials is proving to allow for even bigger leaps. One example is an innovative expanding flap mechanism that has transformed product handling, reducing complexity, costs, and processing time. This game-changing approach not only enhances automation but also redefines what’s possible in modern food production.

"By streamlining production with industrial 3D printing, we not only cut down on costs but also reduced the risk of mechanical failure, ensuring long-term operational reliability."
Paul Bocionek | General Manager at apc-tec GmbH
Challenge
A food industry manufacturer required an efficient solution to place delicate biscuit sticks into cans while ensuring that a paper inlay prevented direct contact between the biscuits and the can’s surface. Traditional methods using external grippers required excessive space, complex programming, and numerous individual components — raising concerns about cost, processing time, and potential errors. Furthermore, the entire solution needed to comply with stringent food contact regulations while maintaining high mechanical reliability under fast-paced production conditions.
Solution
apc-tec GmbH developed a compact, intelligent mechanical system to automate the packaging process efficiently. Instead of using traditional external gripping mechanisms, apc-tec integrated an expanding clamp within the can that fixes the paper inlay in place before filling it with biscuit sticks. "Our innovative solution optimized this production process in ways that traditional manufacturing couldn’t achieve. The combination of intelligent mechanical component design enabled by EOS’ 3D printing and full food-contact declaration makes this a game-changer for food-safe automation,” explains Paul Bocionek, General Manager at apc-tec GmbH.
This approach significantly reduced the number of required components, eliminating the need for additional sensors and complex programmable logic controllers. The entire system was designed and produced using declared food-safe materials, including PA 2200, which complies with (EU) 1935/2004, (EU) 10/2011, and Good Manufacturing Practice (GMP) standards. Additionally, the expanding flap was manufactured using high-precision industrial 3D printing, allowing for rapid prototyping, iteration, and production. “Our EOS machines not only offer high mechanical reliability, but compliant PA 2200 material ensures each part meets stringent food industry requirements without compromising efficiency,” Bocionek highlights.
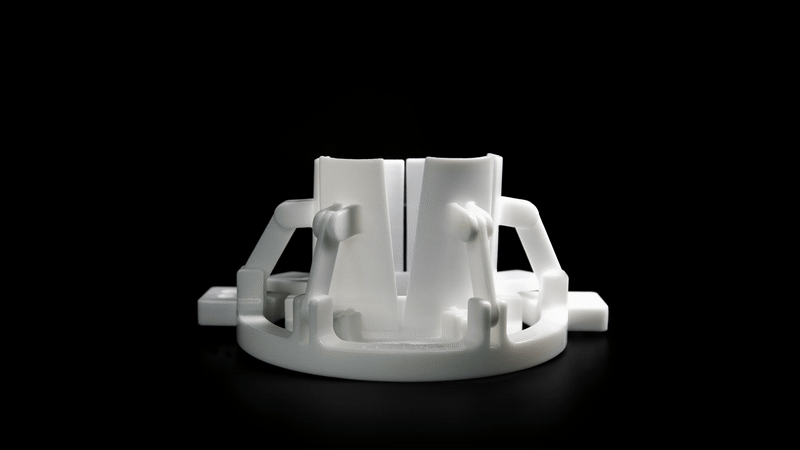
Results
The implementation of apc-tec’s expanding flap transformed the production process by making it significantly more efficient, cost-effective, and compliant with food safety regulations. The compact design, which could only be achieved through AM, eliminated the need for external gripping mechanisms, enabling a more streamlined and space-saving approach. Thanks to the reduced number of components, apc-tec minimized not only material costs but also the time and complexity associated with assembly and programming. “By streamlining production with industrial 3D printing, we not only cut down on costs but also reduced the risk of mechanical failure, ensuring long-term operational reliability,” Bocionek states.
The financial impact was substantial, with initial setup costs reduced from €15,000 to just €2,000, thanks to the elimination of multiple mechanical parts and the simplification of system integration. Furthermore, since the entire flap could be manufactured in a single step using industrial 3D printing, production and implementation timelines were significantly shortened, as the technology enabled rapid design iterations, minimized tooling requirements, and facilitated on-demand manufacturing without delays associated with traditional supply chains.
Beyond cost and efficiency improvements, the new component fully complies with EU food contact regulations and GMP standards, ensuring that all materials used in the process as well as the entire supply chain meet the highest hygiene and safety requirements. This makes it a groundbreaking example of how AM can drive innovation in food production.
"Our solution optimized this production process in ways that traditional manufacturing couldn’t achieve. The combination of intelligent mechanical component design enabled by EOS’ 3D printing and full food-contact declaration makes this a game-changer for food-safe automation."
Paul Bocionek | General Manager at apc-tec GmbH
EOS Case Studies
Explore three decades of pioneering 3D printing excellence with EOS