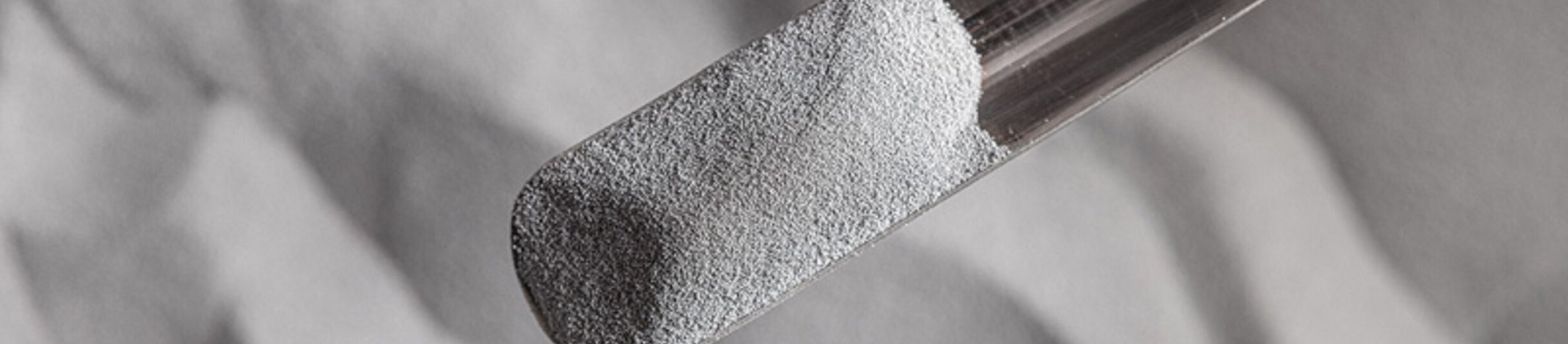
The INTEGRA P 450 Offers Materials Processing up to 300°C
April 13, 2022 | Reading time: 3 min
Achieve unprecedented material flexibility, realize new opportunities for innovation, and embrace possibilities to optimize and develop new materials. Until recently, additive manufacturing (AM) was challenged with a limited portfolio of polymer and composite materials. The INTEGRA P 450 processes materials at up to 300 degrees Celsius, enabling new materials and applications that weren’t possible before.
Unprecedented Material Flexibility
Industries are demanding more engineering-grade materials in AM. While standard 3D printable thermoplastics including polylactic acid (PLA) and acrylonitrile butadiene (ABS) have been available for some time, they are still largely utilized for prototypes and only represent a small fraction of the materials that are used in everyday products. Many applications require engineering-grade plastics to meet challenging requirements in terms of mechanical profile and thermal/chemical resistance.
When using these materials, heat is both a challenge and an opportunity. Materials like nylon 6 and polybutylene terephthalate (PBT) melt at around 225°C and others such as polyetherketoneketone (PEKK), melt at 300°C. But higher melting temperatures also yield better attributes for applications that demand resilience and strength in addition to heat deflection and chemical resistance.
The INTEGRA P 450 was designed with performance materials in mind. With its ability to process materials at up to 300°C, it can not only produce a wider range of thermoplastics, but it can also support composite materials such as glass and carbon fiber filled nylons. With the availability of these materials, customers in aerospace, automotive and medical can leverage the benefits of AM across a broader spectrum of components and parts.
New Opportunities for Innovation
Additive manufacturing offers several important advantages. It’s typically faster and less costly for small runs. Also, because AM relies on digital technology, engineers can design with newfound freedom, which can help with lightweighting, part consolidation, and customization, among other product enhancements. Together, these unique value-adds can help organizations continuously improve, while also providing them a viable short-run alternative to mass production.
The INTEGRA P 450 was built to help customers leverage AM from design to production. Having the ability to process at up to 300°C unlocks a wider gamut of material choices, which can ultimately help companies manufacture end-use parts more quickly and with less supply chain risk.
Optimize and Develop New Materials
Organizations often develop materials with unique properties in mind. To be considered as a mainstream manufacturing technology, AM must become more flexible, providing an open platform where customers can collaborate and innovate.
The open software architecture provides unparalleled access to all of the INTEGRA P 450’s processing parameters. Working with their material suppliers and the team at EOS North America, customers can optimize existing materials for specific uses or even develop new materials that better meet their needs.
For example, one of EOS’ aviation customers wanted to design and qualify new additively manufactured parts. Working with their material partner they developed a carbon fiber filled nylon material that could replace metal parts in certain areas of the aircraft. In tandem, they also tested and validated a PEKK material that offered a higher heat deflection temperature (HDT) than other commercially available materials, while also providing excellent chemical and abrasion resistance. Together these two unique materials are enabling the customer to 3D print components that weren’t possible before, while reducing the weight compared to the original parts.
Conclusions
For additive manufacturing to reach its full potential, customers must have access to more industry standard materials and need the ability to optimize and improve them based on their own requirements. EOS North America is paving the way with its new polymer AM system, the INTEGRA P 450. With material processing at up to 300°C, it offers unprecedented material choice and flexibility, while also providing an open platform where customers can innovate and develop new solutions.
Author: Cary Baur