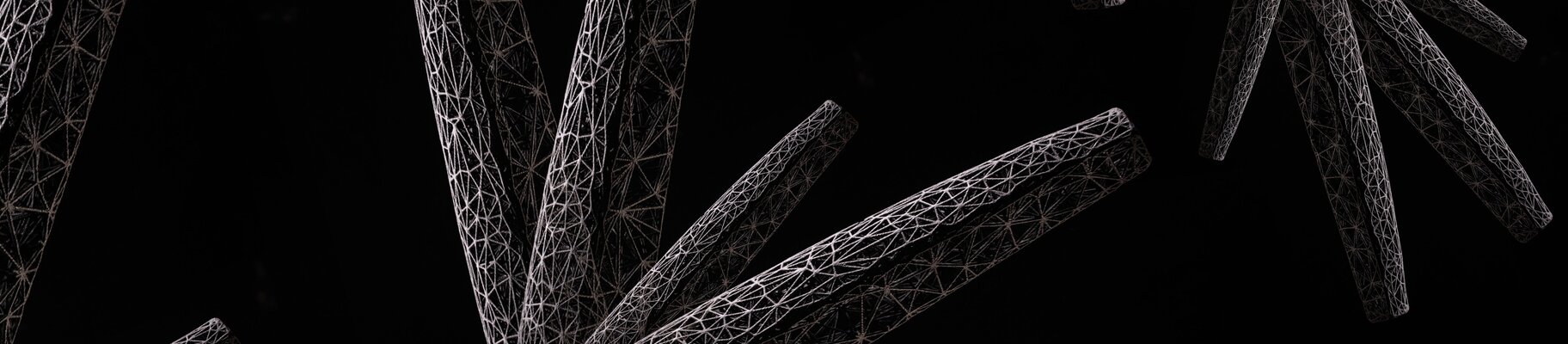
EOS at K 2019 fair LaserProFusion for Tool Free Injection Molding
Highly productive EOS technology makes industrial 3D printing an attractive solution for polymer mass production
____ Düsseldorf, Germany, September 17, 2019
EOS, the world's leading technology supplier in the field of industrial 3D printing of metals and polymers, will be showcasing its range of products and solutions at the K 2019 trade fair (Oct. 16–23, 2019 in Düsseldorf/Germany), the leading trade event for the plastics and rubber industry, in hall 4, stand C25.
With its LaserProFusion technology, EOS will be presenting a revolutionary process for polymer-based additive manufacturing at the fair. The technology is designed to deliver maximum productivity with an emphasis on high-quality and is therefore ideally suited to meet the needs of mass production. It enables tool free injection molding and can even be deployed to replace injection molding in many applications, making industrial 3D printing an attractive prospect for completely new applications.
Tim Rüttermann, Senior Vice President Polymer Systems & Materials at EOS, says: “Conventional injection molding continues to face the challenge that the making of a tool accounts for a considerable part of the costs and is only economically viable for quantities of several thousand units or more. LaserProFusion, however, makes you independent, as both simple and complex components can be manufactured without the need for tools. And digital component data make customized mass production a reality." He continues:
"This 3D printing technology is so productive that it achieves attractive costs-per-part for quantities well over 100,000 per system, per year. Depending on the application, companies can even expand their product portfolio by specifically leveraging the benefits of additive manufacturing."
Tim Rüttermann, Senior Vice President Polymer Systems & Materials at EOS
Small batch production at attractive unit costs
Due to ever-shorter product cycles and an increasing demand for customization, EOS' polymer technology is becoming the right choice for the production of series in small to medium batch sizes. Because of the time saved in product development and the tool-free production, LaserProFusion can reduce costs by up to 20%.
Functional integration: reducing costs, creating added value
Tool free additive manufacturing makes it possible to implement a wide range of technical functions with very few components. The advantage is obvious: all parts required are manufactured in one step, including functional components. The majority of the otherwise required assembly steps are therefore no longer necessary – which saves both time and money. At the same time it also minimizes complexity in both the supply chain and production, thereby boosting output. Looking at the process chains in the already cost-optimized automotive industry, for instance, the use of additive manufacturing can lead to efficiency increases of up to 50%.
Digital additive manufacturing – for sustainable spare parts management
More and more companies need to keep an increasing number of spare parts in stock for many years, which ties up working capital, drives up inventory costs, and makes them dependent on a large number of suppliers. Additive manufacturing is ideal for establishing a future-proof spare parts management system, as digital production makes it possible to make spare parts on demand. The strategy helps streamline the supply chain, reduces logistics and warehousing costs, avoids over-production, and cuts manufacturing and delivery times. The savings per year are frequently in the double-digit million ranges. At the same time, components can be digitally further optimized and a digital warehouse can be established step by step.

Mass customization
The growing demand for product customization is placing mass customization at the center of interest, which can be ideally implemented using additive manufacturing. Products can be quickly adapted on a digital basis. Today, numerous companies already use 3D scans to generate data of the human body, optimize them for 3D printing, and then utilize EOS technology to produce personalized bicycle helmets, glasses, or shoe insoles, for example. The digitalization of product development and manufacturing is creating completely new business models and opening up new market segments at the same time.
One million diode lasers – significantly reduced exposure time
As a pioneer with 30 years of experience in additive manufacturing, EOS is continuously optimizing the interaction between powder materials and laser. The company continues to focus on using lasers as the preferred source of energy for the powder bed process. Almost one million diode lasers are deployed in LaserProFusion technology, with a maximum output of over 5 kilowatts if required.
For each layer, only the diode lasers are activated that match the CAD data of the part – right down to the exact pixel. This method not only makes it possible to perform highly detailed work, the component characteristics can also be influenced locally. The new technology significantly shortens exposure times, regardless of the number of components and their geometry.

About EOS
EOS is the world's leading technology supplier in the field of industrial 3D printing of metals and polymers. Formed in 1989, the independent company is pioneer and innovator for comprehensive solutions in additive manufacturing. Its product portfolio of EOS systems, materials, and process parameters gives customers crucial competitive advantages in terms of product quality and the long-term economic sustainability of their manufacturing processes. Furthermore customers benefit from deep technical expertise in global service, applications engineering and consultancy.
Downloads
EOS at K 2019 fair LaserProFusion for Tool Free Injection Molding
Source: EOS GmbH
-
Exposure process of LaserProFusion technology from EOS
JPG 498,79 kB -
EOS LaserProFusion technology leverages the power of one million lasers
JPG 5,01 MB