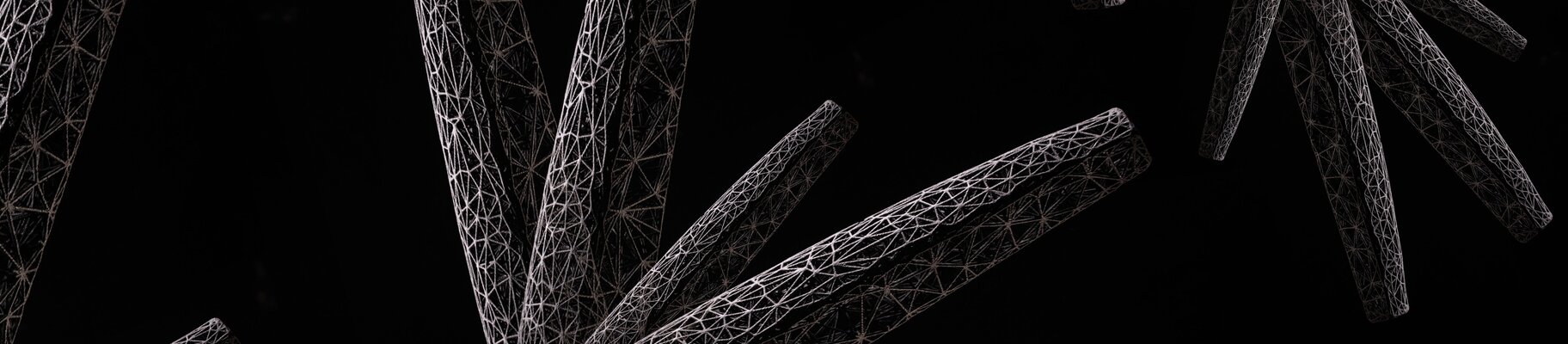
Next innovation leap in metal additive manufacturing
EU project InShaPe
____ Munich, Germany, July 13, 2022
In many industrial sectors, such as in the automotive industry, in aerospace or in the energy sector, the demand for special metal components that are light and have a high-strength is increasing. Modern gas turbines, for example, require extremely stable and at the same time lightweight heat shields. An important manufacturing process for this is the powder-bed fusion process of metals using laser beam (PBF-LB/M). Depending on the application, the process is not yet always competitive compared with conventional production in terms of unit costs. The research and innovation project InShaPe, funded by the EU with EUR 6.8 million, aims to make a decisive contribution to the further development of the technology.
Under the coordination of the Technical University of Munich (TUM), here the Professorship of Laser-based Additive Manufacturing, ten partners from seven countries are working together on the project. In powder-bed fusion of metals, extremely thin layers of metal powder are applied to a building platform. This powder layer is melted by a focused laser beam and binds to the underlying material layer during solidification. This process is repeated layer by layer until a finished component is created. Due to the layered structure, complex and weight-saving geometries can be realised. After removal of excess powder, the finished component is then usually post-processed depending on the application.
Flexible adaptation of the laser spot enables efficient and cost-effective production
"The combination of these two new technologies enables efficient and advanced exposure strategies so that even the most demanding production of complex special components works right away."
Prof. Dr.-Ing. Katrin Wudy from the School of Engineering and Design at the Technical University of Munich.

InShaPe makes metal-based additive manufacturing faster, cheaper and more sustainable
The consortium has set itself the goal of further developing this form of additive manufacturing into a commercially wide-ranging manufacturing technology that shall outperform conventional manufacturing processes such as die casting in terms of precision and sustainability in the future. This is due to the fact that the adaptation of the laser beam shape and the new exposure options enable an energy- and material-efficient production process. At the same time, the InShaPe innovation aims at demonstrating the competitiveness of additive manufacturing compared to traditional manufacturing processes in terms of unit costs, flexibility and production volume. The AI-supported control and operation should also enable non-highly qualified workers to use the new process.
The overall goal of InShaPe is to further develop and demonstrate an innovative powder-bed fusion process for metals (PBF-LB/M) for four industrial applications in the aerospace, energy and automotive industry. Compared to the current state of the art, the following advantages should be achieved:
- a seven times higher production rate
- over 50 percent lower costs
- 60 percent less energy consumption
- 30 percent less waste
In the long term, the successful development and marketing of InShaPe technologies is intended to strengthen the European PBF-LB/M manufacturing industry as a leading provider of highly complex parts and set new best-in-class standards for digital, resource-efficient and agile laser-based production methods.
About the EU project InShaPe
InShaPe started on June 1, 2022 and will run until the end of May 2025. The project is being carried out by the Technical University of Munich with nine other partners from France, Germany, Israel, Italy, the Netherlands, Sweden and Spain. The project is managed by Prof. Dr.-Ing. Katrin Wudy, Head of the Professorship of Laser-based Additive Manufacturing at the Technical University of Munich. The EU is supporting the project with EUR 6.8 million under the European Framework Programme for Research and Innovation, “Horizon Europe”.

Steckbrief InShaPe
Project name: InShaPe (Grant Agreement no. 101058523) – Green Additive Manufacturing through innovative beam shaping and process monitoring
Duration: 06/2022 – 05/2025
Coordination: Technical University of Munich, Germany
Project partners:
- Aenium Engineering, Spain
- AMEXCI, Sweden
- Bavarian Research Alliance GmbH, Germany
- BEAMIT Group, Italy
- Eindhoven University of Technology, The Netherlands
- EOS GmbH Electro Optical Systems, Germany
- Oerlikon AM Europe GmbH, Germany
- SILIOS Technologies, France
- Technion – Israel Institute of Technology, Israel
Project coordinator: Prof. Dr-Ing. Katrin Wudy, Technical University of Munich
Programme: Horizon Europe
Total funding amount: EUR 6
About the Company
EOS
EOS is the world’s leading technology supplier in the field of industrial 3D printing of metals and polymers. Formed in 1989, the independent company is pioneer and innovator for comprehensive solutions in additive manufacturing. Its product portfolio of EOS systems, materials, and process parameters gives customers crucial competitive advantages in terms of product quality and the long-term economic sustainability of their manufacturing processes. Furthermore, customers benefit from deep technical expertise in global service, applications engineering and consultancy.
Downloads
Source: EOS
-
TUM-Components manufactured by powder bed fusion
JPG 2,46 MB -
Prof. Dr.-Ing. Katrin Wudy from the School of Engineering and Design at the Technical University of Munich
JPG 444,96 kB