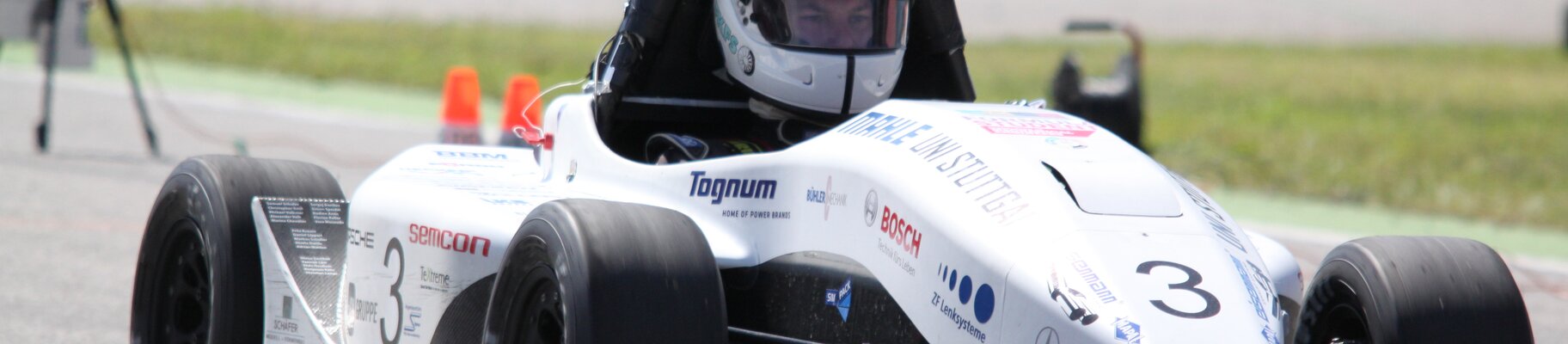
Young Engineers Choose Additive Manufacturing to Tap the Full Potential of the Part
Rennteam Uni Stuttgart | Success Story
-
Significant shortage in development and production time
-
Reliable on the track thanks to an increased rigidity by 20 %
-
Perfect form and contouring for a reduced weight by 35 %
"We are thrilled to have been able to bring the Formula Student Germany 2012 title to Stuttgart. The freedom in the construction process offered by the DMLS technology from EOS has played an important role in our succes."
Yannick Löw | Rennteam Uni Stuttgart
Easing to Victory – The Rennteam Uni Stuttgart Wins the Formula Student Germany With EOS Support
On the one hand, every constructor of an axle-pivot has the task of developing a part with the highest possible stability – otherwise the safety of the vehicle as a whole would be undermined. On the other hand, the wheel mounts cannot, for a number of reasons, weigh too much.
As early as the conceptual design phase, the engineers utilized the CAD software from EOS partners Within Technologies Ltd. Thanks to this tool the constructors were able to match the part perfectly to the structural requirements. In this way, they were able to give the knuckle precisely the required physical properties – lightweight plus rigidity.
One is that with additive manufacturing the need to build negatives or mould forms falls by the wayside. In addition the entire process, from design through fabrication is more precise, meaning that often no reworking or refining is required. The part was almost immediately race-ready.
The weight of the part was reduced by 660 grammes, saving the Rennteam Uni Stuttgart 35 %. At the same time the engineers succeeded in increasing the rigidity by 20 % - big numbers for motorsports, and numbers that translate into faster lap times and reduced fuel consumption.

"We produced the part using the classic precision casting process. This, of course, led to limitations in freedom of form, which meant that the part's potential could never be fully realized. Even back then we'd decided that for the 2012 season we'd investigate new, innovative ways of manufacturing the steering stub axle."
Yannick Löw | Rennteam Uni Stuttgart
The Results at a Glance
- 20 % Higher rigidity
- -660 g Reduction of weight
EOS Success Stories
Explore three decades of pioneering 3D printing excellence with EOS