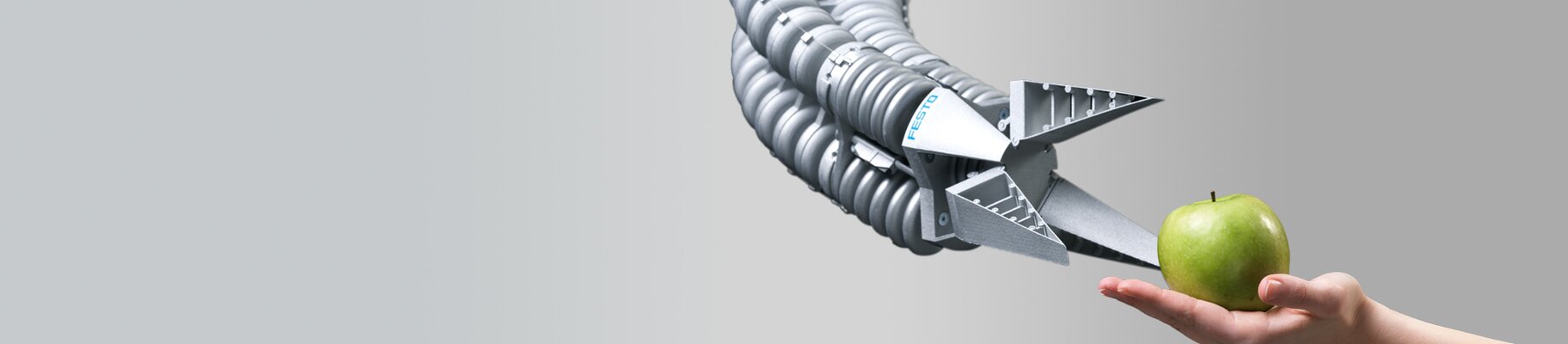
Solutions for a More Economic Small Batch Production
Festo AG | Case Study
Advantages for a Bionic Gripper Design
- Function integration reduces the number of single parts and the expenditure for assembly
- Thanks to the high degree in design flexibility, the design determines the production method
- Innovative manufacturing method makes grippers light-weight and long-lasting
"Laser sintering was the only process that made it possible to produce the Bionic Handling Assistant and its gripping element, the DHDG adaptive gripper. Due to the complexity and integrated functionality of the components, there is no alternative way of production.This process enables us to adjust the DHDG adaptive gripper to the specific application and is thus already used by customers all over the world."
Klaus Müller-Lohmeier | Head of Advanced Prototyping Technology | Festo AG & Co. KG
Additive Manufacturing Offers New Design Solutions for a More Economic Small Batch Production
One example of successful product development and production using additive manufacturing is the DHDG adaptive gripper. It has become an inherent part of Festo‘s production range and is manufactured on a FORMIGA P 100 supplied by EOS. Its structure is adapted from a fish fin and has two flexible bands which form a triangle to converge at the top. Intermediate webs are connected to the bands via joints at regular intervals.
Another example is the Bionic Handling Assistant. The flexible assistance system, which is modelled after an elephant‘s trunk, consists of three basic elements for spatial movement, a hand axis and a gripper with adaptive fingers. With a FORMIGA P 100, a complete handling assistant can be manufactured in just four building sessions.
The EOS technology makes it possible to directly incorporate functions that the final product is supposed to have. This is advantageous, since it reduces the number of parts and the additional assembly costs.
Moreover, the DHDG adaptive gripper is very economic, because it is about 80 % lighter than conventional grippers made of metal. The reason for this is the additive manufacturing of plastics which allows the production of especially light-weight, elastic but very strong structures. Tool-less production saved 40 % of the unit costs compared to injection moulding.

"At the moment, we are also using the EOS technology more and more for projects that only call for limited annual quantities of a complex part. In such cases, the process is a real alternative for us to existing, often tool-based methods."
Klaus Müller-Lohmeier | Head of Advanced Prototyping Technology | Festo AG & Co. KG
The Results at a Glance
- -40 % costs per part reduction
EOS Case Studies
Explore three decades of pioneering 3D printing excellence with EOS