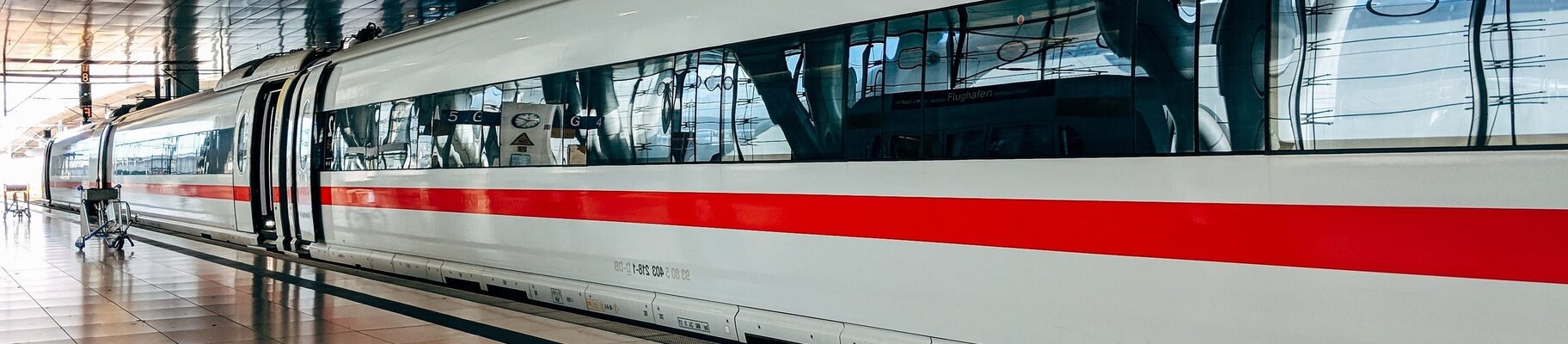
La voie rapide vers des pièces de train personnalisées imprimées en 3D grâce à la fabrication additive d'EOS
Hasenauer & Hesser - Histoire d'une réussite
La Deutsche Bahn choisit la fabrication additive pour entretenir ses trains
La flotte de trains ICE de troisième génération exploitée par la Deutsche Bahn compte un peu moins de 160 unités issues de différentes séries de production. Chacun d'entre eux a toujours l'air moderne, grâce à son design élégant et à ses intérieurs régulièrement rénovés. Malgré cela, l'industrie des transports considère tout ce qui a été construit avant 1996 comme un "youngtimer". Comme pour les automobiles de cette époque, il peut être difficile de trouver des pièces de rechange pour ces trains. Pourtant, la Deutsche Bahn ne se laisse pas décourager, grâce à la technologie d'impression 3D industrielle d'EOS.

"L'énorme avantage de la fabrication additive est que nous pouvons toujours fabriquer des pièces de rechange qui sont aussi bonnes que neuves, ce qui nous permet de maintenir nos trains correctement entretenus pendant des décennies. Nous n'avons pas à faire de compromis sur la qualité ou les performances. Le coût est également inférieur à celui des moules sur mesure."
Florens Lichte | Responsable de l'impression 3D | DB Fahrzeuginstandhaltung GmbH
Défi
Les trains ICE de troisième génération sont quelque peu intimidants. Avec un poids à vide allant de 270 tonnes à plus de 400 tonnes et une vitesse de circulation de 140 à 190 miles par heure, la diversité des composants à bord de chaque train est facilement négligeable. Les composants les plus petits sont souvent les plus difficiles à remplacer. Alors que les vis commerciales standard sont faciles à remplacer, de nombreux autres petits produits fabriqués sur mesure ne peuvent pas être simplement commandés auprès du fabricant s'ils s'usent ou tombent en panne. Pour certaines pièces, la production a été interrompue ; pour d'autres, les fabricants sont insolvables. Seuls quelques exemplaires de chaque pièce sont généralement nécessaires. Les coûts d'outillage élevés et les limites d'achat minimales font qu'il n'est pas rentable de les fabriquer selon les méthodes conventionnelles.
Un lot de 160 unités est minuscule par rapport à des commandes de taille industrielle. En comparaison, des centaines de milliers de véhicules de taille moyenne sont fabriqués chaque année ; même pour les avions, les chiffres de production annuelle peuvent atteindre plusieurs milliers pour les modèles court et moyen-courriers à succès.
Bien que cela démontre certainement la durabilité des trains en tant que moyen de transport, les petites échelles de production compliquent la production et la logistique d'entreposage des pièces de rechange. Des problèmes similaires se posent pour de nombreux autres composants spécialement fabriqués. Dans l'exemple spécifique considéré ici, des pièces de rechange étaient nécessaires pour certains tubes fluorescents très délicats utilisés pour les écrans du système électronique d'information de bord des trains ICE-3 et ICE-T. Les écrans affichent des informations sur la vitesse, l'heure et la distance entre les trains. Les écrans affichent aux passagers des informations sur la vitesse, l'heure et les gares à venir.
Avec le temps, l'usure normale et la fragilité affaiblissent progressivement les pièces moulées par injection de 9,4 x 0,4 x 0,3 pouces, ce qui signifie qu'elles doivent être remplacées tous les 10 à 15 ans. Les véhicules ferroviaires sont conçus pour avoir une durée de vie supérieure à 25 ans, mais il n'est pas rare qu'un train reste en service pendant 40 à 50 ans, voire plus dans des cas exceptionnels. Malgré cela, le fournisseur a décidé d'arrêter la production de ces pièces. Environ 40 unités sont nécessaires par an. L'entreprise de maintenance chargée de cette responsabilité, Electronikzentralwerk (EZW) à Munich/Allemagne, s'est mise à la recherche d'alternatives ou de partenaires susceptibles d'apporter des réponses. Cette recherche a conduit les experts en technologie ferroviaire directement à la fabrication additiveet aux possibilités qu'elle offre.

Solution
La technologie de fabrication additive est la solution idéale, compte tenu des petites tailles de lots. Elle ne nécessite pas de travaux préparatoires importants, par exemple pour la mise en place des outils de fabrication. "D'après notre expérience, une solution basée sur un moule équivalent en aluminium et un déchargement manuel coûterait plusieurs milliers d'euros, avant même les coûts de manutention et de mise en place pour chaque commande, ainsi que les coûts annuels de stockage et d'entretien des moules. En outre, la fabrication des moules prendrait environ trois mois, et les premiers échantillons un mois de plus", explique Florens Lichte, responsable de l'impression 3D chez DB Fahrzeuginstandhaltung GmbH.
Si une entreprise souhaite fabriquer un composant de manière additive, elle n'a pas besoin d'acquérir ses propres imprimantes 3D industrielles ou de développer sa propre expertise - le modèle commercial des fabricants sous contrat profite à tout le monde. C'est la voie choisie par la Deutsche Bahn. Son entreprise de logistique a collaboré avec succès à plusieurs reprises avec Hasenauer & Hesser GmbH. Mais c'est dans les détails que le bât blesse, explique Hans-Jörg Hesser, directeur général de Hasenauer & Hesser GmbH : "Notre objectif premier était de préserver la fonctionnalité du composant. Pour ce faire, les spécifications du composant ont dû être repensées et adaptées au processus de fabrication en couches. L'impression 3D est généralement facile, mais ce projet a exigé une expérience considérable. Le composant utilisé dans les trains ICE est long, étroit et à parois minces. Pour cette raison, il se déforme incroyablement facilement. Le positionnement des pièces dans la chambre de construction était essentiel, d'autant plus que nous voulions fabriquer plus de 200 pièces en même temps pour cette commande.

"Nous avons plus de 10 ans d'expérience dans la fabrication additive et nous utilisons les systèmes EOS depuis toujours. Nous sommes ravis de la qualité des composants et de la fiabilité du système. Ils nous permettent de fournir des pièces de rechange de première qualité à nos clients en temps voulu."
Hans-Jörg Hesser | Directeur général | Hasenauer & Hesser GmbH
Résultats
Les montages ont été fabriqués avec la FORMIGA P 110. En l'absence de données de CAO 3D et de dessins de conception, l'étape de réingénierie a entraîné des dépenses de l'ordre de quatre chiffres. Les coûts de fabrication étaient alors inférieurs de plus de 80 % à ceux du moulage par injection. Le projet a nécessité au total un mois, du début à la première livraison, ce qui signifie que les pièces imprimées en 3D étaient disponibles quatre fois plus rapidement. Les commandes ultérieures pouvaient être traitées en 24 heures. Les employés d'EZW Munich ont eux-mêmes testé les pièces imprimées sur place pour en vérifier la forme, l'ajustement et le fonctionnement. Les résultats ont été très convaincants : les accessoires fabriqués de manière additive répondaient à toutes les exigences du client. "Les pièces étaient parfaitement ajustées et ne se sont pas déformées. Nous avons déjà installé au moins 20 unités", ajoute Florens Lichte.
Cependant, M. Lichte et ses collègues allemands n'ont pas eu à se soucier uniquement de la réussite des tests fonctionnels. Tout plastique destiné à être utilisé dans l'industrie ferroviaire doit satisfaire aux exigences de protection contre l'incendie définies dans la norme EN 45545-2 / DIN 5510-2 (pour les véhicules existants). Il existe différents ensembles d'exigences, avec des exceptions supplémentaires dans certains cas, en fonction de la taille de chaque composant, de son poids, de son emplacement dans le véhicule et de sa distance par rapport à d'autres composants. Le matériau EOS PA 2210 FR sélectionné pour ce projet a dû être soumis à des essais de résistance au feu approfondis pour s'assurer qu'il répondait aux exigences spécifiques de son domaine d'application. Ces nouvelles pièces permettent non seulement aux passagers de se tenir au courant, mais aussi de rester en sécurité lorsqu'ils se déplacent sur les voies à une vitesse vertigineuse.
Les résultats en un coup d'œil
- 75 % Réduction du temps de production
- 80 % Réduction des coûts de production
Les succès d'EOS
Découvrez trois décennies d'excellence en matière d'impression 3D avec EOS