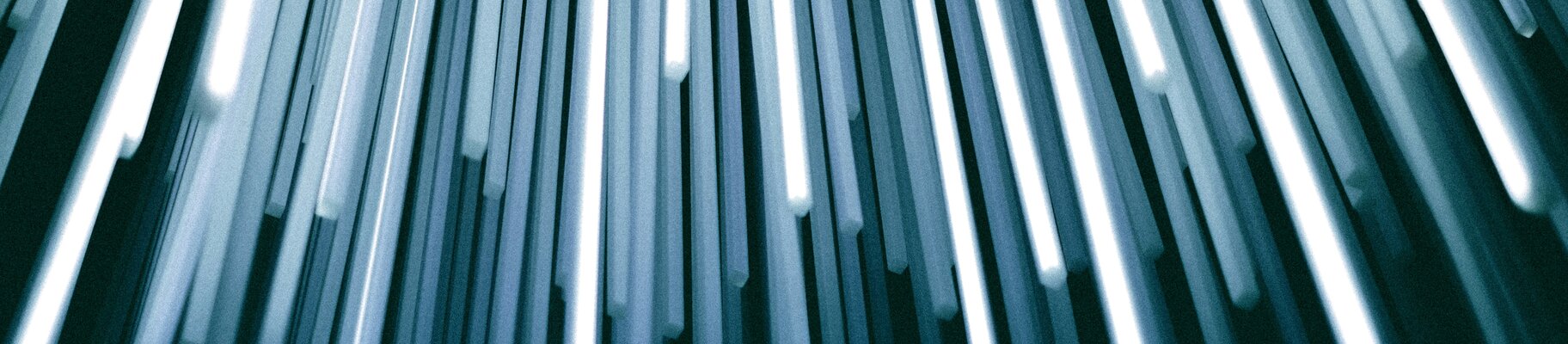
Unlocking the Potential of Automation in Additive Manufacturing
AUGUST 21, 2024 | Reading time: 10 min
Additive manufacturing (AM) has revolutionized the production landscape, offering unprecedented flexibility and precision. However, the full potential of AM can only be unlocked through automation. For EOS M 400-4 users and traditional manufacturers looking to embrace automation, this guide sheds light on how integrating automated solutions can drastically enhance productivity, reduce costs, and optimize production cycles. With all the advanced features it provides, automation can be highly cost-effective, especially when leveraged for night and weekend operations, increasing productive machine time dramatically.
Maximizing Efficiency and Reducing Unproductive Time
One of the most significant advancements in AM automation is the Grenzebach Dual Setup Station - EOS Edition. This system enables automatic changeover of build jobs and automatic job start of the second without the need for an operator.
Here’s how it maximizes efficiency:
- Dual exchange frames: Two exchangeable frames allow the second job to initiate automatically once the first is complete. This innovation reduces the typical laser-off-to-laser-on time.
- Continuous operation: While one job is being unpacked, the second job can run concurrently, thus ensuring continuous operation of the machine. The automatic job start feature makes it possible to utilize nights and weekends productively, without additional investments in personnel.
- Increased productivity: By eliminating some 30% waiting time in a manual setup, the Dual Setup Station can significantly increase productive time. This boost is crucial for manufacturers looking to enhance their output without additional labor costs.

Streamlining Material Handling and Enhancing Safety
Efficient material handling is another critical aspect of automating AM. The Volkmann Automated Powder Handling Solution – EOS Edition addresses these challenges seamlessly across the pre- and post-printing stages. Key benefits include:
- Closed-loop automated powder handling: This system ensures maximum processing efficiency and powder availability while reducing the risk of powder contamination and saving on manual labor.
- Enhanced safety: By minimizing human interaction with the powder, the system enhances workplace safety and complies with stringent industrial safety standards.
- Scalable production: Since all EOS systems are built with forward compatibility in mind, manufacturers can easily scale their production capacity with a production cell of multiple 3D printers.
Efficient and Automated Powder Management
The main component of the automated powder handling solution, the PowTReX – EOS Edition, exemplifies efficient and automated powder management with its advanced functionalities:
- Vacuuming, sieving, and filling: This system efficiently vacuums, sieves, and makes powder available to the machines, ensuring the material is handled optimally throughout the production process.
- Optimized powder conveying: State-of-the-art vacuum conveying ensures reliable material handling, which is critical for uninterrupted serial production.
- Automation: The PowTReX – EOS Edition allows for both automated and manual operations, making it versatile for different EOS M systems.
Handling Large Volumes With Ease
For managing substantial powder volumes, the vHub 250 – EOS Edition offers a versatile solution:
- Large storage capacity: With a capacity to store 250 liters of powder and options to connect multiple units, the vHub 250 caters to large-scale production needs, even as a buffer unit.
- Efficient powder transport: Its integrated vacuum conveyor system can transport powder over distances up to 30 meters, ensuring efficient and quick material handling.
Ensuring Consistent Powder Supply
The vLoader 250 – EOS Edition plays a vital role in maintaining a consistent powder supply to EOS metal AM printers. Capable of operating through a pipe or hose line up to 30 meters, the vLoader 250 provides fully automated filling of the M 400-4 machine and can adapt to various production setups. Additionally, it can be integrated with the vDryer 250 for powder drying.
Leveraging EOS Resources for Optimal Production
EOS provides extensive support and resources to help manufacturers optimize their AM processes, with the Additive Minds team delivering a standout offering. This technical consulting group combines 3D printing expertise from various fields and industries, focusing on customer success in AM applications.
Additive Minds: Expertise and Support
The Additive Minds team, consisting of over 100 global AM experts, collaborates with clients to optimize, validate, and scale industrial 3D printing processes. With over 1,000 projects completed worldwide, they offer:
-
Process optimization: Refining AM processes for higher efficiency and quality.
-
Solutions-oriented approach: Providing setup suggestions tailored to unique challenges.
-
Real-world applications: Courses based on real-world case studies, ensuring practical skills.
-
Expert instructors: Industry leaders providing hands-on support and feedback.
-
Certificate programs: Gain essential AM skills and certification in as little as two days.
By leveraging these resources, manufacturers can enhance their AM capabilities, increase efficiency, and achieve higher-quality production.
Gain a Competitive Edge Through Automation Today
Automating the AM shop floor offers numerous benefits, from increased efficiency and reduced unproductive time to enhanced safety and consistent material handling. For EOS customers, exploring these automated solutions can lead to significant productivity gains and cost savings. By leveraging advanced technologies and consulting services offered by EOS, manufacturers can transform their production processes, gaining a competitive edge in the industry. For personalized advice and solutions, consult EOS Additive Minds.
Share this blog post with peers and colleagues in the manufacturing industry to spread the word about the transformative power of automation in additive manufacturing.