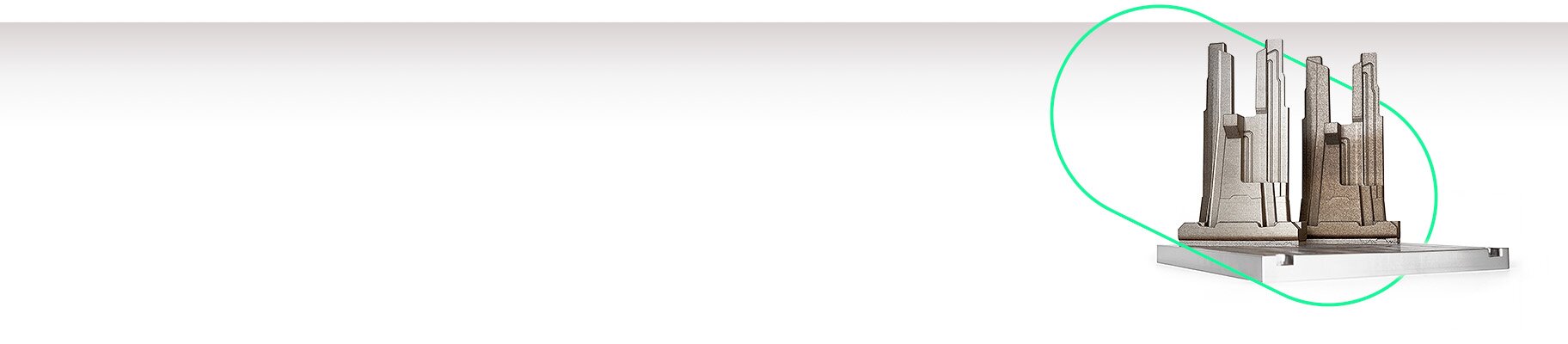
Smart Fusion - Feedback Loop Control
for Homogeneous Microstructures
March 24, 2025 | Reading time: 7 min | Author: Tobias Novotny, Narges Mirzabeigi, Dominik Kunz, Ulrich Kleinhans
Overheating is a major challenge in laser powder bed fusion of metals (PBF-LB/M) which affects the buildability of complex features and flat overhangs, the quality of downfacing surfaces and the material properties of finished parts. While we have demonstrated in the past how Smart Fusion, our feedback loop control system, can reduce the need for support structures, this article aims to showcase its effect on thermal history and microstructure formation. In collaboration with the Institute of Photonic Technologies (LPT), we compared standard open-loop processes with Smart Fusion closed-loop processes in geometries that provoke heat accumulation. We found that Smart Fusion improves the homogeneity of microstructures and hardness significantly by ensuring a consistent thermal signature throughout the build.
Basics of Overheating and Smart Fusion
In PBF-LB/M, the laser repeatedly delivers energy into the part with each layer. If the energy cannot be transferred away from the process zone sufficiently, heat will accumulate during the build and eventually lead to overheating. AM application engineers are well aware of the risks of overheating and have always had options at their disposal to mitigate its effect.
Common approaches to deal with overheating include:
- adding waiting times e.g. minimum layer or vector times for more cooling time
- using more support structures for better heat conduction into the build plate
- lowering the energy input of the process e.g. by reducing laser power
However, waiting times and increased support volume lead to longer build times and higher part costs, while a parameter with reduced energy input may compromise the part density. A different solution is needed.
Figure 1 shows some exemplary build jobs with common geometrical features that are prone to overheating and the corresponding thermal signature with and without Smart Fusion.

In complex geometries, such as the AlSi10Mg bracket, heat accumulation occurs where overhangs or small features restrict heat flow. To achieve stable conditions, the laser power needs to be reduced in those regions.
In build jobs with small exposure areas and thus short layer times, such as the MS1 tooling insert job, heat typically accumulates from layer to layer. This results in increasing part surface temperatures until an equilibrium is reached. Therefore, a gradual reduction in energy input over the build height is required.
Ideally, the energy input should be dynamically adjusted depending on the part geometry and build job load (i.e. layer time). This needs to be done in such a way that the thermal conditions in the part remain stable.
A possible solution consists of measuring thermal signatures during the build job and using a controller to regulate the energy input locally based on the acquired measurement data. Our closed loop control system, Smart Fusion, monitors gray values recorded by optical tomography (EOS Exposure OT), compares them to a material and process-specific target gray value, and adjusts laser power accordingly on a microvector level in the next layer.
Figure 2 illustrates the working principle of Smart Fusion. The difference that Smart Fusion makes is immediately visible when observing the process appearance.
The following video shows the exposure of an exemplary layer for a challenging geometry using Smart Fusion and a standard open-loop process for comparison. Figure 3 shows this geometry and comparative snapshots of the two processes.

To show the effects of overheating in this study, a test geometry consisting of three upside-down cones (“heat accumulation demonstrator”), which had also been used in previous studies, was selected. In this demonstrator, heat accumulated quickly in the cones because of the thin connecting cylinders that act as a thermal bottleneck. Without Smart Fusion this leads to glowing hot part surfaces visible for an extended period of time after the part is exposed.
While our standard process parameters are resistant to overheating, they represent a best compromise of many factors and are therefore not ideal for extreme geometries or excessively short layer times. Using the process signature (i.e. mean GV) that these process parameters typically produce as the target for Smart Fusion ensure the ideal results, even for very complex parts.

Thermal History and its Effect on Microstructure
Parts processed by PBF-LB/M experience a unique thermal history defined by extremely fast cooling rates in the melt pool and cyclic reheating of previously solidified material when adjacent scan vectors and subsequent layers are exposed. When overheating occurs, both the changes to the initial cooling and the subsequent holding at elevated temperatures affect the microstructure evolution.
The surface temperature of the material’s solidified previous layer determines the temperature to which the current layer of material can cool down. If these temperatures reach levels where phase changes occur such as the martensite start temperature (Ms) for steels, the as-built phase composition can be significantly affected. If the martensite transformation is initially suppressed or cannot finish completely, higher levels of retained austenite can be observed, which result in reduced hardness.
In-process precipitation hardening can occur if elevated temperatures are retained in a region of a part for long enough. Therefore, layer times can be critical for the formation of precipitates during the process and precipitation is likely to change depending on the current conditions in the build. Local precipitation leads to inhomogeneous hardness and potentially increased brittleness.
At elevated temperatures typical solidification structures formed in PBF-LB/M such as the Si-rich network in AlSi10Mg start to coarsen or even dissolve. This can reduce the as-built strength significantly (up to 44% hardness loss in testing).
Severe heat accumulation can lead to a tempering of the already solidified material in the process. In challenging geometries made of Ti6Al4V, tempered martensite was observed, which was coarser and more lath-like, instead of the traditional acicular martensite.
Cyclic reheating by subsequent layers also affects microstructure by “tempering” the already solidified material. Differences in the top layer compared to the rest of the build are often attributed to this effect. Overheating can affect the result of the cyclic reheating since a cooling between layers can be required for the tempering effect to occur.
Overall, inconsistent thermal conditions during the build job can lead to local microstructural changes and corresponding variations in mechanical properties. Such changes may result in unexpected deviations in properties when comparing test samples with actual parts and necessitate additional heat treatment (e.g. solution treatment) steps to resolve.
More Homogeneous Properties in EOS MaragingSteel MS1 with Smart Fusion
By now, the typical microstructures for common PBF-LB/M materials are well known. As an example, Figure 6 highlights some features of the as-built microstructure of EOS MaragingSteel MS1 (similar to 1.2709).
Etching reveals a fish-scale like melt pool pattern with clear melt pool boundaries. Clusters of martensite laths are visible in detail images. MS1 is typically martensitic in the as-built state with a small volume fraction of retained austenite. At higher magnifications under the SEM, the cellular and columnar solidifications structures become visible.
Figure 7 compares the microstructure of a heat accumulation demonstrator with and without Smart Fusion.
When Smart Fusion is enabled, a consistent etching response is observed throughout the entire sample. In contrast, for the sample without Smart Fusion, a dark etching region is found above the thermal bottleneck, rather than the traditional bright etching response. On closer inspection, a partial decomposition of the cellular solidification structures is observed. Hardness was significantly higher in the dark etching region, reaching levels up to 540 HV (more than 100 HV higher than usual). This indicates that significant in-situ precipitation takes place.
To prevent recoater contact with the curled edges of the overheating part without Smart Fusion, a minimum exposure time of 40 s was used in this build job. With Smart Fusion enabled, it was also possible to manufacture the part without the need for waiting times. Figure 8 shows a micrograph, as well as a hardness profile comparison between the different settings.
The micrographs demonstrate that even without minimum layer times the feedback loop can effectively control the thermal conditions and produce a highly dense part. Furthermore, an exceptionally consistent hardness was achieved over the build height. The lack of waiting time between layers likely prevented the formation of precipitates, which can occur when the material is tempered by subsequent layers.

Conclusion
Overheating during the PBF-LB/M process results in significant alterations to microstructures depending on part geometry and layer times. Smart Fusion ensures a consistent thermal profile even in the most challenging conditions. By reducing the energy input only where necessary in a dynamic way, more homogeneous properties can be achieved without any loss in productivity for MS1 and Ti6Al4V.
Our results show that Smart Fusion is particularly relevant for:
- More consistent microstructures for complex parts with restricted heat flow
- More consistent microstructures for low build job loads with reduced or no minimum layer times
- Heat treatments which retain the as-built microstructure to some degree (such as direct aging)
- Exploring tailored microstructures and properties
How does Smart Fusion affect microstructures in other materials? We continuously conduct extensive testing on how Smart Fusion performs with our various materials. Do not hesitate to reach out!
Sources and further reading:
Nahr F, Novotny T, Kunz D, Kleinhans U, Chechik L, Bartels D, Schmidt, M. Advanced process control in laser-based powder bed fusion–Smart Fusion feedback-loop control as a path to uniform properties for complex structures?. JMRT 2025;34:604-618. https://doi.org/10.1016/j.jmrt.2024.12.014.
Nahr F, Rasch M, Burkhardt C, Renner J, Baumgärtner B, Hausotte T, et al. Geometrical influence on material properties for Ti6Al4V parts in powder bed fusion. JMMP 2023;7(3):82. https://doi.org/10.3390/jmmp7030082.
Yağmur, A, Pääkkönen, I, Miles, A. The Hitchhiker’s Guide to Smart Fusion. 2023. https://3d.eos.info/eguide-smart-fusion
Kürnsteiner P, Wilms MB, Weisheit A, Gault B, Jägle EA, Raabe D. High-strength Damascus steel by additive manufacturing. Nature 2020;582(7813):515–9. https://doi.org/10.1038/s41586-020-2409-3.
Mohr G, Altenburg SJ, Hilgenberg K. Effects of inter layer time and build height on resulting properties of 316L stainless steel processed by laser powder bed fusion. Addit Manuf 2020;32:101080. https://doi.org/10.1016/j.addma.2020.101080
Bartels D, Albert ME, Nahr F, Schmidt M. On the influence of volumetric energy density and inter-layer time on the material properties of case-hardening steels. Alloys 2023;2(3):168–83. https://doi.org/10.3390/alloys2030013.