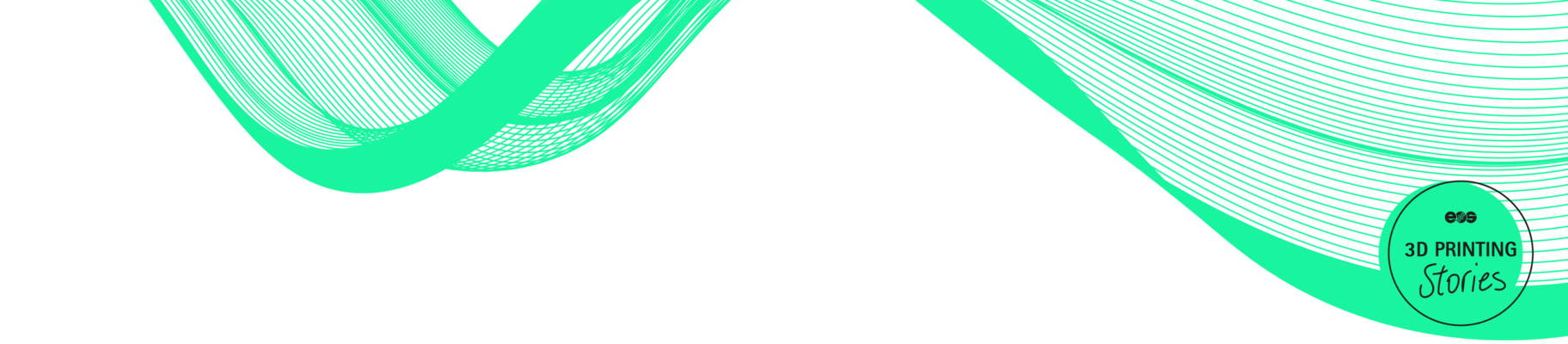
When 3D Printing Makes Life Better
The Berlin start-up LAEMON developed the first IoT-enabled jewelry bracelet with PROTIQ
February 01, 2024 | Reading time: 10 min
We live in a world in which people often feel unsafe when they are walking the streets (especially at night). This was the motivation for the founders of Not Just A Jewel, to implement a solution for non-violent self defense
Self defense with the first IoT-enabled jewelry bracelet
Susana Gomez, co-founder and managing director of Not Just a Jewel, explains: "We wanted to restore a bit of personal freedom in people’s everyday lives." This led to the creation of LAEMON, the first IoT-enabled jewelry bracelet to be able to raise the alarm whenever a situation calls for it. It integrates a loud alarm to deter the threat of attack plus a silent alarm that can be used to inform emergency contacts of the wearer’s location. The Berlin start-up developed its product with PROTIQ, a member of the EOS Contract Manufacturing Network for 3D printing. The evolution from prototype to material and color selection and on to realization of the first product batches was only economically viable thanks to additive manufacturing.
A jewelry bracelet that is rather clever: What is inside LAEMON?
Normally, a person can always be reached on their cellphone or located using tracking functions whenever they are out. However, this might not be possible in threatening situations, since an attacker could easily take the phone away. At its core, LAEMON has a tracking function that operates totally separately from a cellphone by informing emergency contacts or notifying a 24/7 emergency service center with a request for help. This is all possible thanks to a silent alarm that can be activated at the touch of a button. The device also has a loud alarm that can be activated to deter a potential assailant by pulling a small chain. “For us it was important that the alarm should be easy to trigger in a moment of panic or when the victim may be about to lose consciousness,” explains Gomez.
LAEMON's technical solution consists of both a GPS and a Bluetooth antenna and incorporates an eSIM that is NB IoT-enabled, i.e. it employs mobile telephony in the Internet of Things. The eSIM transmits data through the LTE network. If LTE is not available, a second frequency band is accessed as a fallback alternative. Users can manage up to three emergency contacts via an app (Android and iOS). The app can also be used to activate an emergency call center function, operated by partners in each region. “We are delighted to say that we will soon be ready for the market,” says Gomez."PROTIQ has been an important partner for us on our journey, and we still have some way to go together.” The fact is that if it weren't for 3D printing and the existence of a competent service provider like PROTIQ, LAEMON would never have made it this far.
A look at the prototype development process: Time pressure, material selection and coloration
The 3D printing specialists based in Blomberg (North Rhine-Westphalia) became aware of the LAEMON concept sometime between Christmas and New Year’s Eve 2022. Sales manager Stefan de Groot remembers it well: “When Susana Gomez approached me and presented the product, we knew straightaway that we would go with it, because it was obvious that LAEMON has an incredibly high emotional value. However, as the plan was to present the prototypes at the Fashion Week in mid-January, the time schedule was pretty tight.” The 3D data was readily available, but the material selection was still completely unclear. The expectation of Not Just A Jewel was that four or five attempts would be enough to harmonize the material and coloring. Yet thanks to its experience with additive manufacturing coupled with its good instinct, PROTIQ managed it even quicker.
A standard material in the form of Polyamid 12 was chosen for the housing components, as it has ideal mechanical properties and is also suitable for coating and dipping to achieve the desired coloring. The frame - the decorative casing that houses the technical components - and several other small parts were realized by de Groot using a copper material specially developed for this purpose on an EOS M 290. “Additive manufacturing gives copper a dense microstructure with no pores. This was important, because the casings are polished, and copper lends itself well to this process.” The bracelet itself is made from thermoplastic elastomer (TPU), which you could say was a stroke of luck, because following the build process, the bracelet is dipped and smoothed to create the coloration. This gives it a look that is not quite homogeneous and a feel that is reminiscent of leather. Gomez notes: “We were really thrilled by this, and indeed the first two LAEMON prototypes were a resounding success at the Fashion Week.”
A further round of optimizations took place at the end of February, this time focusing on colorations for several different variants. For this purpose, once the TPU bracelets had been made, they were dipped and chemically smoothed to examine the effect of the various colors. “We then took a RAL color fan and searched for suitable hues for the case,” de Groot explains. “It took a few attempts to get the violet hue right, but now it looks great.”
How 3D printing goes on a journey – And what path LAEMON has ahead of it
It is only thanks to additive manufacturing that projects like LAEMON are economically viable, which shows just how valuable the technology is when it comes to developing innovative products. Even a quantity as small as one unit is financially feasible, whereas with the classic casting process, the tool costs for all the components alone often represent a four-to-five-figure investment. Complex shapes such as the undercuts in the LAEMON frame can also be easily realized. Added to this is the rapid implementation plus the ability to modify colors and forms with no major effort. Susana Gomez says: “It was clear to us from the start that we could only move into the development stage with 3D printing. Our product also has S, M, L and XL models to accommodate different wrist sizes – so once everything else is in place, this will be no problem to realize.“
PROTIQ has been cooperating with EOS for a long time now and is also a member of the EOS Contract Manufacturing Network. The company uses ten EOS machines, including FORMIGA P 110 Velocis and EOS P 396 systems for plastics and EOS M 290 and AMCM M 290 systems for metal applications. “The machines run smoothly, the component quality is high, and the operation is simple - we are very satisfied with them, as are our customers,” concludes de Groot.
So where will LAEMON go from here? The prototype development has been concluded, the technology is mature, the app has been launched, and the search for investors for the certification phase is already underway. The plan is to be ready and to commence sales in time for the 2023 Christmas business period. For this reason, the cooperation with PROTIQ is set to continue, as the first batch has been set at 1,000 units, and after a positive market launch, batches of 2,000 to 3,000 units will follow. “Until then, we will definitely stay with 3D printing because of the ease of making modifications.” This is also good news for de Groot and his team, since LAEMON gives employees with children something else to smile about.
#3dprintingstories