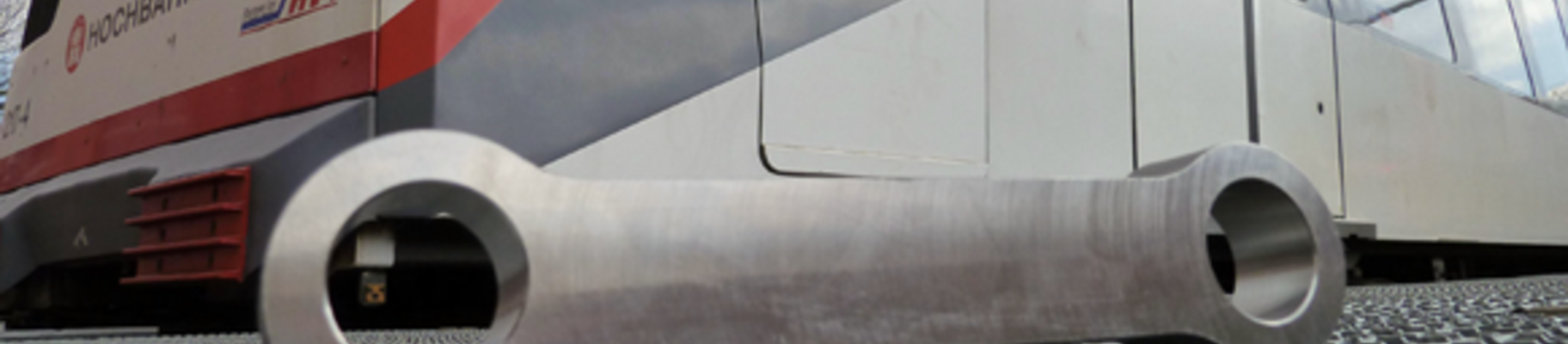
Rethinking the Railway: Stefanie Brickwede
The Multi-Million Dollar Power of AM
APRIL 17, 2025 | Reading time: 5 min
In a recent episode of the Additive Snack Podcast, host Fabian Alefeld welcomed back Stefanie Brickwede, a prominent figure driving AM adoption not only within Germany's national railway company, Deutsche Bahn (DB), but also across various sectors through the network she leads.
This discussion offered a fascinating look into a decade of AM implementation at DB, the strategic evolution from niche applications to a core manufacturing pillar, and the critical role of collaboration in accelerating progress.
Welcoming a Pioneer Back to the Podcast
Fabian Alefeld reintroduced Stefanie Brickwede, highlighting her dual roles as Head of Additive Manufacturing at Deutsche Bahn and Managing Director of the Mobility Goes Additive (MGA) network. Having last spoken a few years prior, this episode provided an update on the remarkable progress DB and MGA have made.
A Decade of Additive at Deutsche Bahn: From Obsolescence to Strategy
Stefanie shared that DB is celebrating its 10th anniversary of using AM this year. The journey began modestly, tackling the challenge of obsolescence. With trains often operating for 30, 40, or even 50 years, acquiring spare parts for older models becomes increasingly difficult and expensive. AM presented a perfect solution for producing these unavailable parts on demand. What started with just 10 parts has exploded: DB has now printed over 150,000 parts across 700 different use cases, utilizing 12 different AM technologies.
Interestingly, DB's initial approach was uniquely bottom-up. As primarily a maintainer rather than a constructor, DB lacked comprehensive CAD databases for its vast inventory. Instead of a typical top-down corporate initiative, Stefanie's team reached out directly to colleagues in maintenance workshops, asking enthusiastic individuals across the 200,000-employee company who were willing to join the AM effort.
This created a passionate, hierarchy-agnostic team that identified real-world needs directly from the ground level. Only later did DB start incorporating jigs, fixtures, and tooling – often considered low-hanging fruit – and developing more strategic, top-down approaches using improved databases and even AI to identify printable parts. Now, both bottom-up enthusiasm and top-down strategy work in tandem.
Measuring Success: From Parts Printed to Millions Saved
Stefanie amusingly recalled an early KPI discussion where her boss, formerly of Airbus, initially suggested measuring success by printing 20,000 parts in the first year – a target met with laughter given they had only printed 10 parts at the time.
While the number of parts (specifically real spare parts, prototypes, or tooling, not giveaways) was an early metric, the focus quickly shifted to quantifiable financial impact. Since 2019, AM has generated savings amounting to double-digit million Euros annually for DB.
These savings come from various streams: overcoming minimum order quantities, reducing lead times significantly (like the gear housing case discussed below), and preventing costly train standstills.
The most significant future potential, however, lies in digital warehousing. DB's physical warehouse for rolling stock alone holds parts worth €1.8 billion, 10% of which could already be printed today.
Tapping into this potential is DB's "Road to 100 Million" strategy, aiming to realize € 100 million in savings through on-demand manufacturing and reduced physical inventory. To drive this, DB now requires that for newly procured trains, 10% of the parts must be designed to be printable, a trend adopted by Dutch colleagues (NS).

Overcoming Hurdles: Acceptance, Qualification, and Standards
Stefanie highlighted the power of making the technology tangible – bringing physical metal printed parts to stakeholders helped open eyes. Communication, internal marketing, and even an employee competition (which served both to find applications and spread awareness) were key. The growing prevalence of home FDM printers also helped familiarize employees with the basic concepts of AM.
A major hurdle, particularly for critical components, is the lengthy certification process.
The printing itself is often not the bottleneck; qualification and testing take the most time. Recognizing this, DB and MGA actively worked with standardization bodies like the German Institute for Standardization (DIN) to create needed guidelines. A key result is the DIN 52920 standard, which helps assess a production site's capability to print critical parts reliably.
Stefanie stressed the need for harmonized European (EN) or international (ISO, ASTM) standards to facilitate broader adoption and simplify supplier integration, calling standards "hacking" truly "sexy" because it enables scaling.
Mobility Goes Additive: The Power of Networked Collaboration
Recognizing the need to learn from others and scale faster, DB initiated the MGA network nine years ago with just nine founding members. Today, MGA is a leading European AM network with nearly 150 member companies, including major rail operators, suppliers, machine producers, material providers, software companies, R&D institutes, and universities.
MGA fosters collaboration across the entire supply chain and multiple industries, including rail, aviation, automotive, aerospace, construction, defense, medical, and even lifestyle (fashion, jewelry, design). Working groups tackle common challenges like certification, material development, sustainability, and education.
Stefanie shared examples like a rapid workshop on copper printing organized within 14 days and the development of a needed flame-retardant powder (fulfilling high rail norms, previously limited to materials like Ultem 9085) through collaboration between Siemens and material provider Lehmann&Voss. This user-driven network bridges the gap between industry needs and supplier capabilities.
Success Story: Averting a Crisis with AM
A powerful example of AM's impact involved 50 cargo locomotives standing idle due to unobtainable gear housings. Traditional sourcing quoted minimum order quantities and a two-year lead time.
Facing a potential crisis discussed at the board level, Stefanie's team leveraged the MGA network, re-engineered the part, and used AM to print sand molds for casting the housings in the original material.
The entire process, from problem identification to delivering the first replacement housing, took only two months – a dramatic demonstration of AM's ability to ensure operational resilience.

The Road Ahead: Adaptive and Disruptive Growth
Stefanie emphasizes that AM offers both adaptive solutions (replacing parts like-for-like, making adoption easier for conservative industries) and disruptive potential (new designs, optimized parts). Both are needed. She advocates for the AM industry to step into the user's shoes, adapting to their needs rather than forcing users to adapt entirely to the technology.
Stefanie Brickwede's insights underscore the transformative power of AM when implemented strategically and collaboratively. Deutsche Bahn's decade-long journey provides a compelling blueprint for leveraging AM to enhance efficiency, resilience, and innovation, while MGA demonstrates the exponential value of cross-industry partnerships in overcoming shared challenges and accelerating the adoption of this game-changing technology.