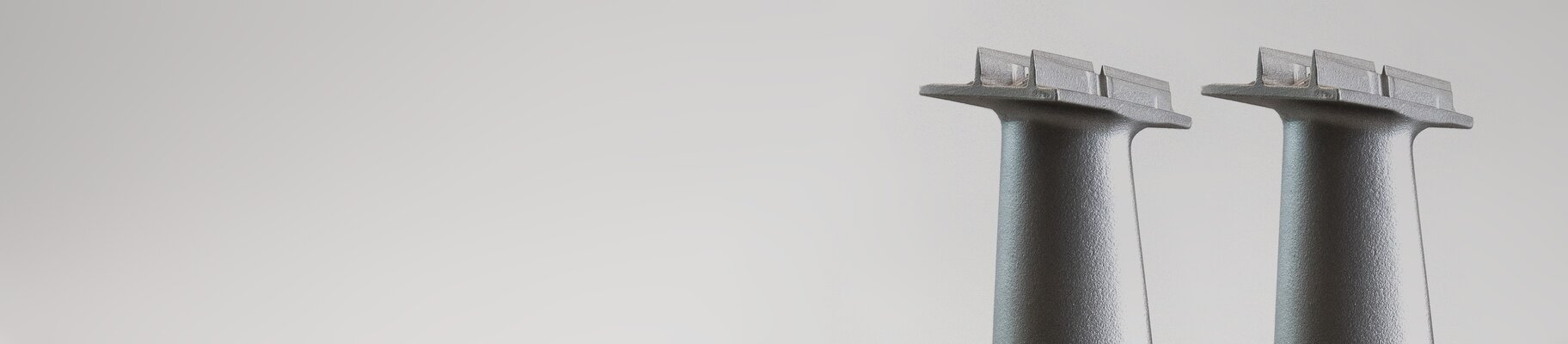
EOS NickelAlloy IN738: A New Era for Additive Gas Turbine Applications
NOVEMber 15, 2024 | Reading time: 5 min
As the global leader in industrial additive manufacturing (AM) technology, EOS is committed to staying at the forefront of innovation with groundbreaking materials that set new industry standards. One example of that is EOS NickelAlloy IN738.
This high performance superalloy is engineered for use in demanding high temperature and high stress applications in gas turbine engines.
The addition of IN738 marks a significant advancement in the EOS material portfolio, addressing some of the critical challenges faced by various applications across industries, including gas turbines.
Tackling the Challenges of Additive Manufacturing With Superalloys
Superalloys like IN738 have always been pivotal for industries requiring materials that can withstand extreme conditions. However, additively manufacturing these materials, particularly through Laser Powder Bed Fusion (LPBF), has presented unique challenges. Historically, superalloys in LPBF have been prone to issues like microcracking and poor creep performance, which have limited their broader adoption.
Microcracking, in particular, is a significant issue in LPBF AM due to the presence of minor elements used in strengthening grain boundaries at high temperatures. Removing these elements entirely to improve processability, however, leads to a severe compromise in the material’s high temperature capabilities, creating a challenging trade-off.
EOS NickelAlloy IN738: Optimized for Performance and Processability
At EOS, we have taken a pioneering approach to overcome these challenges by developing a modified version of the legacy IN738 alloy. Through extensive research and development, supported by CALPHAD-based solidification simulations, we have optimized the alloy composition to maintain the critical grain boundary strengthening elements while minimizing their detrimental effects on processability.
Our modified alloy shows a significant reduction in microcracking tendencies compared to the conventional IN738. This was achieved by carefully adjusting the composition of alloying elements, enabling the material to be processed via LPBF with a dense, crack-free microstructure. The solidification simulations played a crucial role in predicting and mitigating the risks associated with different compositions, allowing us to fine-tune the alloy before moving to the experimental phase.
Enhanced Performance in High Temperature Environments
The benefits of EOS NickelAlloy IN738 extend beyond its improved processability. In stress rupture tests, the modified IN738 demonstrated a 50% increase in rupture life compared to the conventional composition. This enhancement is critical for components like gas turbine blades, which operate under continuous high stress and temperature conditions. The alloy's remarkable yield strength means it offers better durability and reliability in service, considerably extending the part’s lifetime.
Moreover, the improved creep performance of IN738 allows for the production of cooling structures in turbine blades with more intricate designs and similar applications. These advanced designs are essential for improving the efficiency and longevity of turbines, especially as operating temperatures continue to rise. With IN738, our customers can design blades that require less cooling, thanks to the alloy's superior strength and stability at high temperatures, combined with more efficient cooling geometries only feasible by applying AM.

Benefits for the Aerospace and Energy Industries
For industries like aerospace and energy, where component efficiency and lifespan are paramount, EOS NickelAlloy IN738 offers several key advantages. The enhanced creep resistance of IN738 allows for extended component life cycles, meaning turbines can operate longer without the need for frequent part replacements. This not only improves the overall performance of the turbines but also significantly reduces maintenance costs.
Notably, current users of EOS NickelAlloy IN939, which has been widely used for similar applications, may find substantial benefits in upgrading to IN738. The superior high temperature performance and processability of IN738 provide a compelling reason for customers to consider making the switch to this new material for even greater efficiency and durability in their critical applications.

A Commitment to Innovation
EOS’s commitment to pushing the boundaries of what’s possible in AM is underscored by our ongoing investment in material innovation, with EOS NickelAlloy IN738 being one example among many. This application reflects our dedication to innovation and to providing our customers with cutting-edge materials that solve their most pressing challenges.
Looking ahead, we continue to explore further optimizations of IN738 for even more demanding applications. While our focus for this material remains on gas turbines, we see potential for this alloy in other high performance applications, such as marine turbochargers, where similar operating conditions prevail.
With the addition of EOS NickelAlloy IN738, EOS’s material portfolio stands as a testament to our unwavering commitment to advancing additive manufacturing technology. By addressing the longstanding challenges associated with superalloys in LPBF AM, we are empowering our customers in the aerospace and energy industries to achieve greater efficiency, reliability, and innovation in their operations.
If you’d like to learn more about EOS NickelAlloy IN738, its use cases and material qualities, you can learn more here.