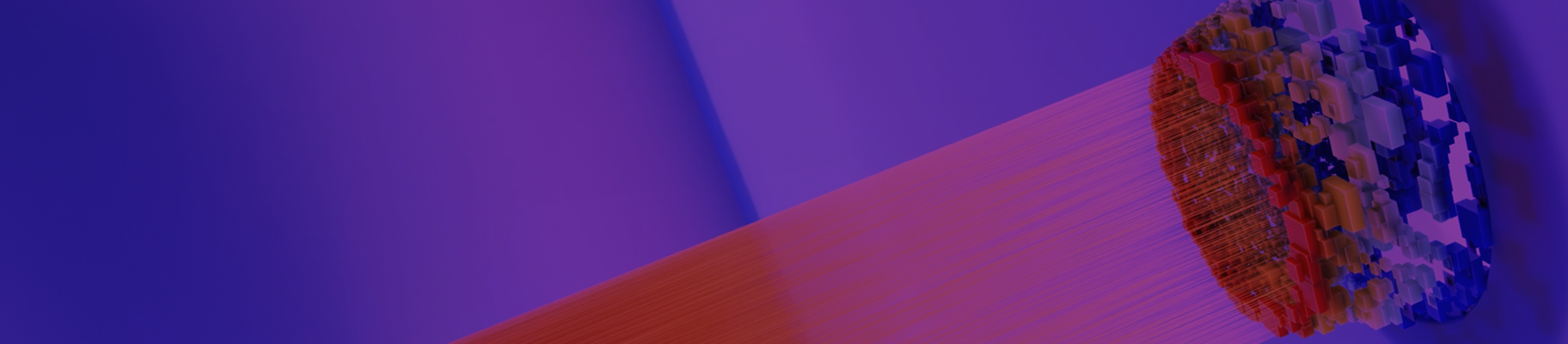
Entering the Next Era of Additive Manufacturing With Beam Shaping
APRIL 15, 2025 | Reading time: 5 min
The metal additive manufacturing (AM) industry is approaching a new phase — one where productivity and efficiency gains are no longer constrained by traditional Gaussian beam profiles. Instead, dynamic beam shaping technology, powered by nLIGHT AFX laser innovation, will break barriers and redefine what’s possible.
For AM manufacturers using EOS and AMCM metal solutions, this innovation isn’t just a technical improvement — it’s a competitive advantage. Beam shaping delivers increased productivity, enhanced process stability, and expanded material capabilities. But how does it work, and why does it matter? Let’s explore.
The Beam Shaping Revolution: More Than Just More Lasers
The industry has long pursued higher productivity by increasing the number of lasers in AM systems. While this boosts build rates, it also raises operational costs and maintenance complexity. But beam shaping provides an alternative approach, enhancing laser efficiency and expanding process windows without increasing cost of ownership.
At EOS, we’re approaching this challenge with EOS Metal Solutions powered by nLIGHT AFX lasers, enabling:
- Up to 2x faster build rates without compromising part quality, thanks to seven switchable beam profiles enabling higher throughput.
- Unmatched laser flexibility, with spot sizes ranging from approximately 85µm Gaussian profiles up to 250µm ring profiles, allowing for precise control over energy distribution.

Rather than relying solely on more lasers, EOS is focusing on smarter laser utilization — distributing heat more evenly to create a more stable melt pool, reduce spatter, and enable better material processability. This adaptive approach ensures that manufacturers can scale productivity while maintaining consistency and quality, a critical factor in aerospace, defense, and industrial tooling applications.

Key Advantages of Beam Shaping in Metal AM
- Higher productivity without sacrificing quality: Studies have confirmed that beam shaping delivers tangible productivity gains. Research on Inconel 718 demonstrated a 23% increase in build rate compared to Gaussian beams, while processing 316L stainless steel was accelerated by a factor of two due to larger hatch distances and higher scanning speeds.
- Improved process stability and reduced spatter: One of the biggest challenges in Powder Bed Fusion-Laser Beam (PBF-LB) AM is spatter generation, which contaminates powder beds and shortens filter life. A study at Fraunhofer IAPT found that using a ring-shaped beam profile reduced soot and spatter by 75%, resulting in cleaner builds and lower material waste.
- Processing hard-to-weld materials: Beam shaping enables the processing of previously difficult materials, including nickel-based superalloys, tool steels, select aluminum alloys, and refractory metals. This paves the way for new applications in aerospace, defense, and industrial tooling, where advanced material properties are critical.
- Consistent part quality and reduced post-processing: By stabilizing the melt pool, beam shaping minimizes part-to-part variability and enables better microstructure control. A Technical University of Munich study on 316L stainless steel found that a ring beam profile significantly expanded the process window, allowing for greater flexibility while maintaining high-density parts. This also means fewer post-processing steps, which directly lowers production costs.
- Cost efficiency through extended powder and filter life: As EOS found out during its own research on IN718, beam shaping reduced powder loss by up to 70% and decreased condensate formation by 60%, directly improving material utilization and reducing maintenance cycles. For EOS customers, this means lower consumable costs, less downtime, and more efficient use of high-value metal powders — delivering a faster return on investment.
Why It Matters for EOS Customers
For manufacturers using EOS and AMCM metal solutions, integrating beam shaping technology means faster production cycles, improved material efficiency, and lower overall costs — without the need for costly multi-laser systems.
"With the cutting-edge power of nLIGHT AFX Lasers, EOS Metal Solutions is redefining the future of additive manufacturing. We are pushing the boundaries of material innovation, significantly enhancing production speed and achieving levels of precision that were once thought impossible".
Sebastian Becker, Head of Product Management Metal at EOS
Moreover, seamless integration is a key benefit for EOS customers. Beam shaping is designed to work within existing EOS workflows, meaning it can be implemented without extensive requalification.
This ensures an easy transition to higher productivity and better part quality while leveraging your existing knowledge and infrastructure.
See Beam Shaping in Action – Download the Whitepaper
The EOS Whitepaper on Beam Shaping in Additive Manufacturing provides in-depth insights, best practices, and research-backed results on this game-changing technology. Whether you’re looking to improve productivity, process stability, or material capabilities, beam shaping is the next evolution in AM.
Download the whitepaper today and discover how EOS Metal Solutions powered by nLIGHT AFX lasers can transform your AM processes.