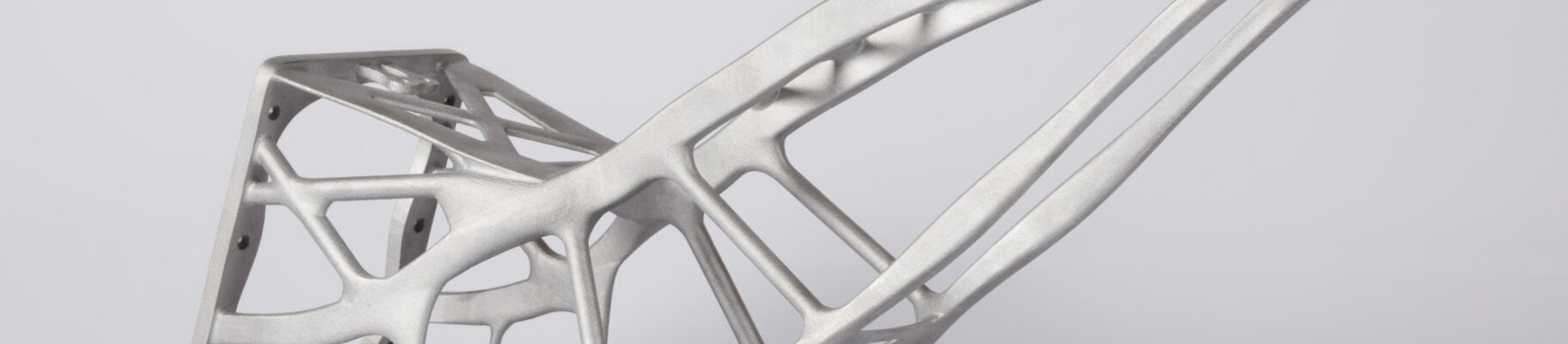
RUAG 3D 인공위성
RUAG의 센티널 위성을 위한 안테나 교체 - 전 세계 설치를 위한 인증 획득 | 혁신 사례
우주의 끝이 없다고 하면 많은 사람들이 할리우드 영화 스튜디오에서나 볼 수 있는 공상 과학 소설을 떠올립니다. 그러나 실제 현실에서는 우주에 필요한 기술을 개발하고 우주에 정착시키기 위한 강한 의지와 선명한 비전을 가지고 있습니다. 스위스 기술 기업 RUAG는 지구 위를 감시하는 센티널 위성을 건설하는 데 있어 이러한 비전을 제시했습니다. 여기에서도 환경 외에도 첨가제 비료가 중요한 역할을 했습니다.
"Es ist gewissermaßen die Quadratur des Kreises: 더 가볍고 동시에 견고한 항공기를 만드는 것이 우리의 목표입니다. 제품의 특성은 비행 및 주행에 필요한 강도를 요구하는 테스트를 통해 입증되었습니다. 향후 몇 년 동안 추가적으로 많은 이야기를 듣게 될 것입니다."
프랑크 모리오 | 구조 총괄 매니저 | RUAG
도움말
센티널 위성을 위한 매우 가볍고 견고한 안테나 보호 장치 제작
2016년 독일 항공우주연구센터(DLR)의 발표에 따르면 수송 중량 1kg당 세계 우주 탐사 임무 비용은 20.000유로 이상입니다. 각 부품의 무게가 1그램 감소할 때마다 전체 시작 비용이 감소하므로 시스템에 더 적은 동력이 필요하기 때문입니다. 따라서 각 그램의 각 부품에서 작동 시간을 절약해야 하며, 이는 빠르게 증가하기 때문입니다. 이 경우 스위스 콘체른 RUAG는 최적의 안테나 설계가 필요했습니다.
그러나 전원 최적화만으로는 충분하지 않습니다. 시동을 걸면 시계에 가해지는 충격이 상당하고 진동이 심합니다.
또한 시간당 수십 킬로미터에 달하는 엄청난 속도와 높은 G-크래프트로 인해 비행이 일반 여객기에서 기대하는 것처럼 급격하게 떨어지지 않습니다. 안정성과 견고성은 모든 기체에서 두 번째로 중요한 포인트입니다. 안타깝게도 이러한 요구 사항은 일반적으로 노트북의 필요성에 대한 요구 사항으로 널리 알려져 있습니다.
엔지니어들은 형태와 무게 사이의 적절한 타협점을 찾기 위해 복잡한 구조로 작업합니다.
RUAG 팀은 기존의 고정 방식이 한계에 부딪혔기 때문에 안테나 고정 구조에 대한 견고함과 무게의 최적의 조합을 찾고자 했습니다.
다행히도 첨가제 발효는 필요한 가공 자유도를 달성할 수 있는 완벽한 방법을 제공했습니다. 이미 높은 진동으로 인해 특별한 테스트가 필요했습니다. 현재로서는 규정상 수리가 불가능하다는 결론에 도달했습니다. 이는 또한 왜 그러한 부품의 인증이 더 길고 복잡한 프로세스인지 설명합니다. 모든 인증은 인증을 획득한 엔지니어를 위한 인증서입니다.
복잡한 구조로 인해 무게와 안정성에 대한 모든 요구 사항을 충족하는 적층 가공을 통한 부품 제작
이러한 경우 전체 제품 세트는 특히 항공 및 우주 분야에서 중요한 역할을 합니다. "부가 가공을 통한 부품 제작의 엄청난 이점은 당연히 우리에게 큰 관심사였습니다."라고 RUAG의 구조물 총괄 매니저인 프랑크 모리오(Franck Mouriaux)는 설명합니다. "특히 디자인 자유도와 복잡한 구조물의 무게를 줄이는 데 도움이 되었습니다. 또한 기능을 통합할 수 있는 기능도 매우 유용합니다. 그러나 이제는 이러한 잠재적인 이점을 파악하고, 이를 최적으로 활용하고, 적절한 사용 권한을 얻는 것이 중요합니다. 아무리 간단한 도구라도 활용하지 못하면 아무 소용이 없습니다."
기본적인 특성 및 안정성 테스트는 안테나 구성의 출발점이 됩니다. 다음 단계에서는 재료 선택, 프로세스 정의 및 재료 특성을 고려한 첫 번째 기본 테스트를 포괄했습니다. 그 다음에는 부품의 위상 최적화를 위한 출발점으로 사용되는 첫 번째 테스트 구조가 구축되었습니다. 집중적인 작업과 Altair의 CAD 및 FEM 시스템, 그리고 설계 및 시공 시 EOS의 조언을 결합하여 이론적으로 완벽한 형태의 안테나 안테나를 완성할 수 있었습니다.

Die ca. 40cm 길이의 안테나 교체는 독일 Barleben의 citim GmbH( EOS M 400 )에서 제공했습니다. 400 x 400 x 400mm의 부피에서 하나의 패키지에 두 개의 안테나, 30개의 검침구 및 다양한 검침구를 설치할 수 있었습니다. 소요 시간은 약 80시간이 걸렸습니다. 매개변수로는 품질과 생산성에 최적화된 60µm의 칩 두께가 사용되었습니다.
사용된 알루미늄 소재 EOS 알루미늄 AlSi10Mg는 높은 견고성과 동적 충격에 대한 뛰어난 내구성으로 인해 고내구성을 자랑하며, 고내구성이 요구되는 작업 환경에서 사용하기에 적합합니다. 요구되는 특성을 파악하기 위해 프로젝트 전체 부피의 최대 80%까지 공기와 실내에서 광범위한 테스트를 수행했습니다. 테스트에는 자체적으로 제공된 구조가 사용되었습니다. 무엇보다도 개발자들은 컴퓨터 그래픽의 제한 사항을 조사했습니다. 또한 다양한 기계적 및 물리적 실험을 수행했습니다. 때로는 부품에 가해지는 하중이 하중 한계를 초과하여 결국에는 부품이 파손될 수 있었습니다.
"EOS는 혁신을 부가 가치 창출에 대한 큰 경험과 연결합니다. 이 시스템은 모든 시장과 모든 분야에 정말 흥미로운 가능성을 제공합니다."
안드레아스 베르카우(Dipl.-Ing.) | CEO | citim GmbH
결과
이러한 노력의 결과로 센티널 위성에 대한 새로운 안테나가 모든 기대치를 뛰어넘었습니다. 이 제품은 인증을 획득하여 전 세계에서 사용할 수 있게 되었습니다. 이 성능은 차량뿐만 아니라 유치원에서도 추가 비료의 적용으로 인해 더욱 주목받고 있습니다.
따라서 부품의 견고성에 대한 최소 요구 사항을 30% 이상 초과하여 난기류 속에서도 이상적인 안테나 위치에 도달하고 지구와의 기능 연결을 보장할 수 있는 잠금 장치에 대한 요구 사항을 충족해야 했습니다.
그 결과 최종 제품의 중량이 1.6kg에서 940g으로 40% 이상 감소하여 최종 제품의 무게가 크게 감소했습니다.
이 경우 혁신적인 기술을 도입하여 향상된 성능과 낮은 시스템 비용이라는 놀라운 조합을 달성할 수 있었습니다. "우리는 이 프로젝트의 결과에 매우 만족합니다. 우리는 프로세스를 통해 신대륙에 정착했고 안정적이고 가벼운 작업으로 사랑받고 있습니다."라고 항공 및 우주 산업 전문가인 Mouriaux는 말합니다.
"첨가제 가공을 통해 기본적인 운영 기술 요구 사항을 충족할 수 있음을 보여주었습니다. 다양한 구조적 장점과 부품 자체의 특성이 이를 확실히 입증했습니다. 저는 이 기술의 잠재력이 매우 크다고 생각합니다."
한 눈에 보는 결과
- 30% 스타라이트 - 최소 요구 사항 30% 초과 달성
- 40% 속도 감소
더 보기
- 인텔리전트: 구성 자유도를 통해 동일한 제품 배포 가능
- 인증: 포괄적인 테스트를 통해 항공 및 지상 분야의 요구 사항 확인
자세히 보기
EOS로 3D 프린팅의 선구자적인 3년을 경험해 보세요.