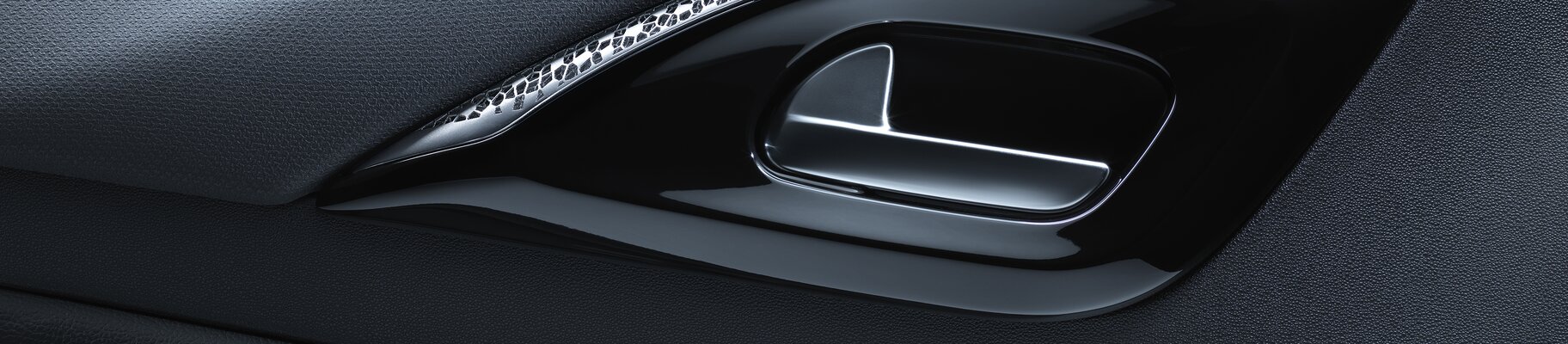
Fertigation additive pour les véhicules de grande taille
Spartacus3D - Histoire d'une réussite
DS 3 Dark Side Limited Edition - Fortschrittliche Innovation durch additive Fertigung
Dans le secteur de l'automobile, les offres limitées de modèles de réussite constituent un outil de marketing efficace. Cependant, les constructeurs automobiles cherchent toujours des moyens spécifiques pour s'affranchir de leurs concurrents dans leurs segments de marché. DS Automobiles, une marque du groupe PSA, s'est engagée il y a moins d'un an à créer une gamme de modèles uniques dans le segment haut de gamme. Dans ce segment, le modèle compact DS 3 est déjà bien connu et sera régulièrement proposé en version limitée. Pour l'édition Dark Side, DS Automobile a choisi d'améliorer l'apparence de la voiture et d'utiliser des pièces imprimées en 3D, afin de renforcer son engagement permanent en faveur de l'innovation. La fabrication additive a offert à l'équipe de conception de DS une grande liberté créative et a permis, grâce aux experts de Spartacus3D, qui ont travaillé avec la machineEOS M 290 , une mise en œuvre et une production très rapides et faciles.
"Il s'agissait, du début à la fin, d'un projet très intéressant, qui s'est avéré aussi passionnant qu'exigeant pour notre savoir-faire. Nous sommes ravis de constater que toutes ces voitures sont aujourd'hui en circulation dans le monde entier. Et au cours de l'ensemble du projet, nous nous sommes rendu compte que nous pouvions compter sur la disponibilité, la qualité et l'assistance d'EOS".
Charles de Forges | Directeur général | Spartacus3D

Herausforderung
Fabrication d'un revêtement à haute résistance pour la DS 3, en série limitée, avec un design original et une durée de mise sur le marché plus courte
Le projet a débuté lorsque l'équipe de design de DS a proposé des améliorations innovantes pour l'intérieur de la DS 3 Limited Edition. Les accessoires sont destinés à renforcer la position dominante du constructeur automobile en matière d'innovation et à générer les plus hauts niveaux de qualité des segments haut de gamme. Dès le début, les concepteurs se sont attachés à exploiter le potentiel de la fertilisation additive et à présenter une première mondiale dans ce domaine. La fertilisation additive offre de nouvelles possibilités de conception.
DS Automobiles propose chaque année plusieurs éditions limitées de la DS 3, de sorte que ces nouvelles options représentent une nouveauté inédite pour l'équipe. L'équipe de conception a également opté pour le titane, un matériau qui confère une touche luxueuse, qui est très résistant et qui permet un traitement simple et efficace.
Alors que la trousse 3D est souvent utilisée pour le prototypage dans le secteur de l'automobile, la production en série avec une finition additive est de plus en plus rare, en particulier dans le cas des pièces métalliques. C'est pourquoi DS Automobiles a dû trouver un partenaire qui, outre ses connaissances dans le domaine de la fertilisation additive, possède également d'excellentes compétences en matière de production, afin de répondre aux exigences de l'entreprise. L'objectif était de mettre sur le marché environ 700 véhicules automobiles dans le monde entier. Le projet comportait également une longue période de développement, qui s'inscrivait dans le cadre de la planification de la production des véhicules, ainsi que des critères très stricts en ce qui concerne la mise sur le marché.
Chaque version limitée a un prix différent, de sorte que tous les éléments supplémentaires ajoutés au budget global doivent être pris en compte. La phase d'étude s'est achevée par le choix de deux éléments : la barre d'arrêt et la barre d'arrêt.
Spartacus3D, une société sœur du groupe französischen Materialtransformationsgruppe Farinia, a répondu à toutes ces exigences : L'entreprise, qui utilise la technologie 3D depuis plus de dix ans, possède une connaissance approfondie de la fabrication additive, ce qui lui permet d'intégrer dans la production les éléments proposés par l'équipe DS. Avec le site EOS M 290 et l'EOS Titanium Ti64, Spartacus3D a obtenu toutes les fonctions nécessaires pour répondre aux exigences de DS Automobiles en matière de conception et de qualité, ainsi que les capacités de production et de traitement nécessaires pour que le projet soit mené à bien sans délai.
Solution
Sérienfertigung der Teile auf einer EOS M 290 in EOS Titanium Ti64
L'équipe de conception de DS a eu recours à un design paramétrique innovant, afin que les revêtements intérieurs du châssis et le détail des composants électroniques soient intégrés dans un modèle de titre très performant, ce qui a renforcé l'innovation et la qualité de DS Automobiles.
Pour trouver le meilleur compromis entre la qualité, le coût et le design, de nombreuses itérations entre l'équipe de conception de DS et Spartacus3D ont été nécessaires. L'élaboration de plusieurs prototypes a également été nécessaire, ce qui, dans le cadre d'une production additionnelle, est particulièrement facile à réaliser.
Dans le cadre de ce processus, l'équipe de conception de DS a également examiné la surface des produits et s'est efforcée d'obtenir une surface mate attrayante, obtenue par polissage manuel. L'équipe chargée de la qualité a adopté des critères de qualité génériques pour la formation, la qualité de la couche supérieure (notamment la porosité et le glaçage) et les caractéristiques techniques. Parallèlement à cela, Spartacus3D a également travaillé à l'optimisation de la production des produits. Pour réduire les coûts, Spartacus3D a dû non seulement mettre au point la meilleure configuration et la meilleure structure, mais aussi mettre au point une stratégie solide en matière de laser. Il est notoire que Titan a obtenu, au cours de l'opération d'abattage, un certain nombre d'effets, et que la longue durée d'utilisation de l'appareil a été un excellent candidat pour une transformation maximale. L'utilisation d'un système d'assistance en cas de panne n'était pas possible du point de vue financier ; des paramètres spécifiques ont donc été utilisés pour réduire ce risque. D'autres possibilités de réduire les coûts consistent à réduire le nombre de fichiers par charge ou à réduire le nombre d'exemplaires, le prix de vente, la durée de traitement, etc.

Les connaissances de Spartacus3D dans le domaine de la fertilisation additive étaient à chaque étape du processus d'une valeur inestimable, de la construction à l'optimisation des véhicules en 3D, ce qui a conduit à un développement de la production plus rapide et à une mise sur le marché plus rapide. La sélection des matériaux optimaux a permis d'améliorer la stabilité et de garantir une qualité maximale de la teinte après le traitement. "C'est un privilège d'être partenaire de DS Automobiles pour ce projet très innovant. Cette marque est depuis des années synonyme d'élégance et de savoir-faire dans l'industrie automobile française. Cela signifie également que nos réalisations sont appréciées et que Spartacus3D est en mesure de fournir des solutions robustes pour la production en série. Avec les systèmes DMLS que nous avons dans notre atelier, nous savions que nous devions être en mesure de produire les meilleures pièces", déclare Charles de Forges, directeur général de Spartacus3D.
Résultats
Grâce au savoir-faire de Spartacus3D en matière de fabrication de disques 3D, il a été possible de mettre au point une stratégie de production additive optimisée pour les besoins des équipes de conception de DS. L'outil paramétrique permet d'exploiter pleinement le potentiel de la technologie EOS : Le schéma de fonctionnement très complexe des deux appareils a pu être modifié rapidement de l'un à l'autre grâce à la fertilisation additionnelle et a été optimisé de manière à ce que plusieurs éléments puissent être mis en œuvre simultanément. Par ailleurs, les coûts de production ont été réduits au minimum.
Le matériau, EOS Titanium Ti64, a également permis un traitement de surface qui a conféré à la surface des ponts en türgriff et à l'haleine de la chaussure une surface brillante et un aspect très brillant. Le résultat peut être assimilé à de l'art, avec un design élégant et raffiné et une structure très aboutie, l'élégance, l'innovation et l'exclusivité de la marque françoise étant parfaitement respectées - tout ce qui fait la force de DS Automobiles.
Il y avait environ 10 unités de production pour environ 2 000 articles - 3 pièces dans chaque voiture -, pour lesquelles environ 2 000 heures de travail étaient prévues. L'ensemble du projet a été mené à bien en moins de deux semaines, de la validation des modèles par l'équipe de conception de DS à la livraison des produits finis.
DS Automobiles s'est mis en tête de trouver une solution originale dans le domaine de l'automobile, tout en s'efforçant de surmonter les obstacles liés à la conception traditionnelle, car la DS 3 Dark Side a été rejetée par ses clients. Grâce à l'expertise de Spartacus3D et aux possibilités offertes par les solutions de fertilisation complémentaires d'EOS, l'équipe de conception de la DS a pu mener à bien un projet complexe en très peu de temps.

Le résultat d'un coup d'œil
- Coût : Production de 200 pièces par lot sans altération de la qualité
- Präzise : Amélioration du paramètre de processus pour la vérification des formes du tablier de 30 cm de long dans le cadre de la construction d'un bâtiment en saillie
- Rapidement : moins d'une heure de production par élément
- Freiheit im Design : dreidimensionales, filigranes Titangewebe erfüllt die Anforderungen von DS Automobiles an Innovation and Premium-Exklusivität
Les succès d'EOS
Découvrez trois ans de travail de pionnier dans le domaine de l'impression 3D avec EOS