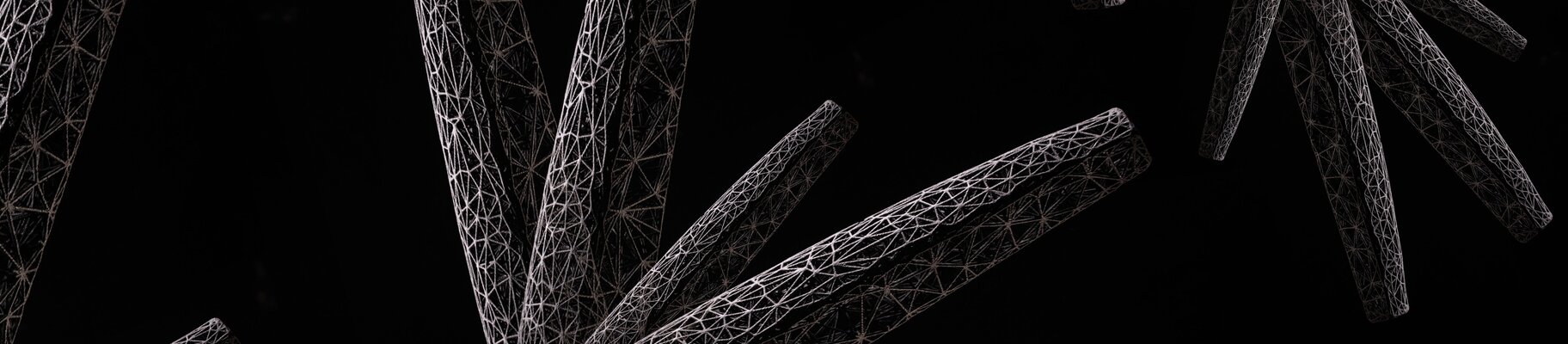
NextGen FA - L'impression 3D automatisée est une réussite totale
Le projet commun entre Premium AEROTEC, EOS et Daimler démontre un énorme potentiel pour la production de pièces de rechange et de composants de série.
____ Augsburg/Varel, Krailling, Stuttgart, 30. avril 2019
Ce qui a commencé comme une vision prometteuse en mai 2017 a maintenant trouvé une conclusion heureuse : le projet"NextGenAM" pour le développement d'une ligne de production pilote pour un processus automatisé de "fabrication additive" de nouvelle génération par les partenaires Premium AEROTEC, EOS et Daimler.
Le processus d'impression 3D, également connu sous le nom de "fabrication additive" (FA), est devenu de plus en plus intéressant en tant que processus complémentaire ou alternatif aux techniques de fabrication conventionnelles. La technologie est décrite comme "additive" en raison de la façon dont le processus implique l'application couche après couche d'un matériau mince, qui est ensuite durci par une source d'énergie. Outre les plastiques et les céramiques, il est également possible de produire des composants métalliques dans le cadre d'un processus d'impression 3D.
L'objectif du projet pilote était de développer une ligne de fabrication numérique de nouvelle génération capable de produire des composants en aluminium pour les secteurs de l'automobile et de l'aérospatiale de manière beaucoup plus rentable que ce qui est actuellement possible. Le succès de NextGenAM : en termes de processus de production global chez Premium AEROTEC, les coûts de fabrication ont pu être réduits de 50 % par rapport aux systèmes d'impression 3D existants.
"L'automatisation est l'un des principaux moteurs de notre stratégie, car elle permet d'intégrer nos systèmes dans des lignes de production automatisées telles que POLYLINE. C'est important pour réduire les coûts par pièce et garantir la qualité tout au long de la chaîne de production.
Permettre la fabrication en série est l'une des principales raisons pour lesquelles DyeMansion a été fondée, et c'est pour cela que nos systèmes sont conçus, pour porter le post-traitement à ce niveau. Le Powershot DUAL Performance a été conçu pour s'adapter à l'échelle, de sorte qu'il peut desservir dix imprimantes en production, voire plus, et rendre ainsi possible une usine de bout en bout. Ce qu'il faut retenir, c'est qu'une usine automatisée de bout en bout est possible grâce à l'impression 3D. Le succès du projet POLYLINE montre ce qui est possible et ce n'est que le début".
Dr Thomas Ehm, président du conseil d'administration de Premium AEROTEC
Production entièrement automatisée
Le secret réside dans une chaîne de production additive ingénieuse et évolutive, entièrement automatisée jusqu'au moment où les pièces imprimées sont mécaniquement sciées de la plate-forme de construction. Cela signifie qu'aucun travail manuel n'est nécessaire à aucun stade du processus, depuis la préparation des données et l'approvisionnement central en poudre jusqu'au processus de fabrication FA lui-même, en passant par le traitement thermique, l'assurance qualité et la séparation des composants de la plate-forme de fabrication. Le cœur technique du système est le système à quatre lasers EOS M 400-4 pour l'impression 3D industrielle de matériaux métalliques. Un système de transport sans conducteur et des robots assurent le déplacement sans heurts des pièces à chaque étape de la chaîne de production.
L'ensemble du processus de production se déroule sans personnel d'exploitation, à partir d'un centre de contrôle central et autonome. Le système repose sur la mise en réseau de toutes les machines utilisées. Les données relatives aux travaux de construction sont transmises au centre de contrôle, qui classe ensuite les différentes demandes de construction par ordre de priorité et les attribue à un système FA . Pendant le processus de construction, l'état de la fabrication peut également être consulté sur un appareil mobile, indépendamment du lieu. Une fois la chaîne de production terminée, les rapports de qualité sont renvoyés de manière centralisée au centre de contrôle. Toutes les données nécessaires à la production d'un "jumeau" numérique sont accessibles ici, ce qui permet notamment une traçabilité complète.
Capacité extensible
Une chaîne de données 3D continue avec une gestion intégrée de la qualité fait de ce système de production l'un des premiers exemples de la référence pour l'avenir, l'industrie 4.0. Le processus de fabrication est totalement évolutif : les lignes de production peuvent simplement être dupliquées pour étendre la capacité de l'usine. Cela laisse présager de nouvelles économies substantielles à l'avenir, au fur et à mesure que les chiffres augmentent. Aujourd'hui, l'installation pilote est déjà capable de fabriquer de manière automatisée des composants selon les normes de qualité de la production en série.
Des pièces pour Daimler sont déjà produites sur la nouvelle ligne technologique de Premium AEROTEC : l'unité de camions, par exemple, utilise déjà la première pièce de rechange fabriquée à Premium AEROTEC. Il s'agit d'un support pour un moteur diesel de camion.

Pièces de rechange pour camions et autobus
Le processus d'impression 3D est particulièrement utile dans le secteur des pièces de rechange car, en cas de problème d'outil, les pièces peu fréquentes peuvent souvent être reproduites de manière plus rentable qu'avec les processus conventionnels de moulage en sable ou sous pression. Les premières demandes de pièces de rechange d'autobus en aluminium imprimées en 3D sont actuellement examinées par le centre de compétence pour l'impression 3D de Daimler Buses. L'équipe d'analyse dans le domaine des voitures particulières est également en train d'étudier les applications potentielles appropriées.
Opportunités pour les plus petites séries et le développement avancé
"La fabrication additive est également adaptée à la production de petites séries de nouveaux véhicules (éditions limitées). Le développement systématique de pièces spécialement conçues pour l'impression 3D permet de réduire davantage les coûts de production et d'optimiser la qualité. L'impression 3D est également particulièrement utile lors du développement préliminaire des véhicules. Les faibles quantités requises peuvent souvent être produites de manière plus rentable et plus rapide avec la fabrication additive qu'avec les processus de production conventionnels".
Jasmin Eichler, responsable des technologies futures chez Daimler AG
Et cela vaut aussi bien pour les véhicules à moteur à combustion que pour les voitures électriques. L'impression 3D est également parfaitement adaptée, par exemple, à la production des plaques de base intégrées qui supportent les conduites de refroidissement des batteries des véhicules électriques...
Qualité élevée des produits en standard
La haute qualité des produits est la norme dans l'installation pilote : il est également prévu d'utiliser un alliage aluminium/magnésium/scandium à haute résistance (également connu sous le nom de Scalmalloy®) pour des pièces utilisées dans les secteurs de l'aviation et de l'aérospatiale.
Pour le secteur automobile, on utilise un alliage d'aluminium classique (AlSi10Mg), dont les propriétés matérielles ont été continuellement améliorées au cours du projet pilote. La résistance du matériau et la qualité de la finition, entre autres, ont été considérablement améliorées par rapport à ce qu'elles étaient il y a deux ans, au début de la coopération.
Perspectives : L'impression 3D, une méthode de production qui offre de bonnes perspectives
Maintenant que tous les contrôles de qualité ont été passés avec des résultats aussi prometteurs, les préparatifs sont en cours pour un audit conforme aux exigences de la norme industrielle stricte VDA 6.3. Il s'agit de l'une des conditions préalables à la fourniture par Daimler de composants de série par des fournisseurs d'impression à façon. L'automatisation de l'ensemble de la chaîne de production FA permettra à l'avenir de fabriquer des lots plus importants en série, avec la même fiabilité, la même fonctionnalité, la même durabilité et la même rentabilité que les composants fabriqués de manière conventionnelle. Les composants des nouveaux véhicules peuvent être optimisés pour l'impression 3D dès la phase de conception, ce qui promet de nouveaux avantages en termes de coûts. L'impression 3D offre également des avantages en termes de poids, ce qui est particulièrement intéressant pour les véhicules électriques. En ce qui concerne les pièces de rechange, l'impression 3D présente l'avantage, à l'avenir, de réduire les coûts d'entreposage, car les pièces peuvent être produites "à la demande". Cette vision de l'avenir est également connue chez Daimler sous le nom de "stock numérique", c'est-à-dire la disponibilité centralisée des données de fabrication numériques pour permettre la production décentralisée de pièces de rechange à l'aide de l'impression 3D.
Comme vous pouvez le constater, l'impression 3D est en passe de s'imposer dans les secteurs de l'automobile et de l'aérospatiale comme une méthode de production supplémentaire, très polyvalente et relativement jeune.

Partenaires du projet
Premium AEROTEC
Premium AEROTEC est le premier équipementier au monde à fournir des composants imprimés en 3D à base d'alliages de titane pour la production en série d'avions Airbus. L'entreprise est un acteur mondial du secteur de l'aviation. Son cœur de métier est le développement et la fabrication de structures aéronautiques en métal et en matériaux composites à base de fibres de carbone. L'entreprise possède des sites en Allemagne à Augsbourg, Brême, Hambourg, Nordenham et Varel. Premium AEROTEC a assumé ici la responsabilité de l'ensemble du processus de production du projet commun.
______________
EOS
EOS est le premier fournisseur mondial de technologies dans le domaine de l'impression 3D industrielle de métaux et de polymères. Créée en 1989, cette entreprise indépendante est pionnière et innovante en matière de solutions globales de fabrication additive. Son portefeuille de produits, composé de systèmes EOS, de matériaux et de paramètres de processus, offre à ses clients des avantages concurrentiels décisifs en termes de qualité des produits et de viabilité économique à long terme de leurs processus de fabrication. Dans le cadre du projet commun, EOS a fourni l'ensemble de la technologie d'impression 3D et les solutions logicielles associées, ainsi que le centre de contrôle permettant de relier et de gérer la chaîne de production.
______________
Daimler
Daimler a apporté au projet son expérience en matière de production à grande échelle. Les unités de recherche et de développement avancé ont travaillé en étroite collaboration. Parmi les aspects abordés figuraient les échantillons de composants, la robustesse informatique et la numérisation des données relatives aux composants pour l'ensemble du processus de production. Les essais des échantillons de composants ont également été pris en charge par le constructeur automobile, tout comme la production d'un cahier des charges de fabrication normalisé pour l'impression en 3D. Daimler était en outre responsable du suivi de la validation et de la certification conformément à la norme VDA 6.3 en ce qui concerne la production en série.
Téléchargements
-
Support pour un moteur diesel de camion, fabriqué dans le cadre du projet NextGenAM.
JPG 2,74 MB -
Au centre de la chaîne de production pilote se trouve le système à quatre lasers EOS M 400-4 pour l'impression 3D industrielle de matériaux métalliques.
JPG 881,07 kB