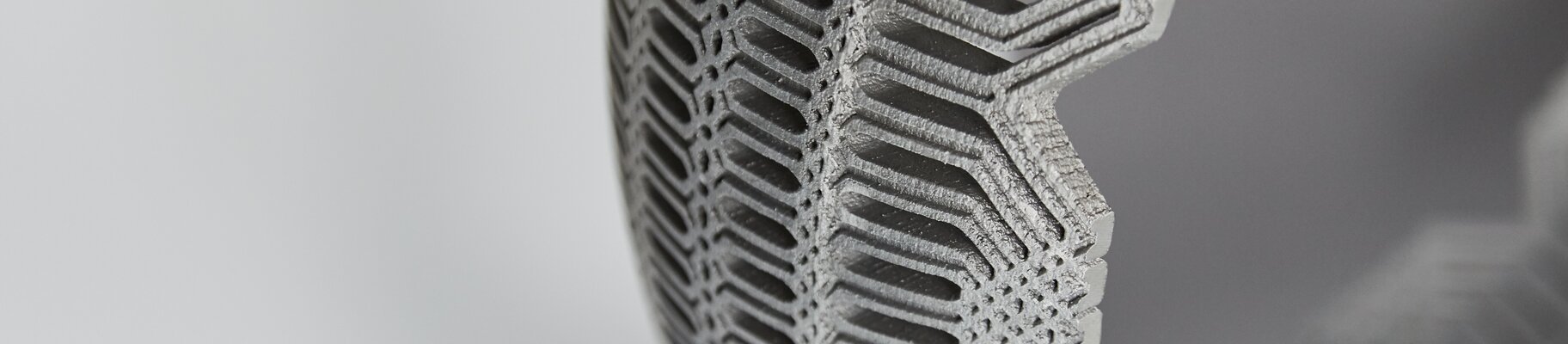
3D Printing in the Manufacturing Sector
Applications and Practical Examples
Best Practices for 3D Printing in Manufacturing & Production Environments
Cost pressure, regulatory requirements, increasing demands from customers, and much more. Companies in production and industry face a constantly expanding collection of challenges. At the same time, issues such as energy and resource efficiency are becoming increasingly important.
Additive manufacturing offers a broad spectrum of potential cost-efficient and sustainable advantages to companies in production and industry.
Industrial 3D printing opens new opportunities and provides solutions in many different ways, from part production to optimizing return on investment. At EOS, we offer custom solutions from a single source for technology and everything else you need for a safe and rapid transition.
More Efficiency in Cost, Functionality & Design
DMLS offers many advantages to companies in the electronics industry, including faster time to market, the manufacturing of prototypes, pilot and small production series parts, and swiftly implementing customer-specific solutions. Whether you need heat exchangers, housings, communication parts, drones, three-dimensional circuit boards or inductors – the diversity of possible additive manufacturing applications spans the entire industry.
At EOS, we’re ready to support your applications, from machines and peripherals to materials, to consulting services for the successful introduction, implementation and expansion of your additive manufacturing program. Our portfolio is built upon decades of market experience, expertise with industry-specific topics and collaboration with leading partners.
Advantages of 3D Printed Heat Exchangers
- Produce light-weight and space-efficient parts
- Realize highly complex cooling channels
- Avoid joints and achive excellent thermal conductivity
- Rapid product development
To show the video you have to accept marketing cookies.
Betatype
Betatype is a technology company specializing in design for 3D printing that constantly pushes the limits of additive manufacturing. By carefully balancing the stacking of cooling elements while also minimizing support structures, the available space was exploited optimally: 384 parts were manufactured in a single batch.
An optimized design and intelligent laser scanning paths reduced the production time from 444 hours to just 34 hours. This provided significant cost advantages to Betatype’s customers: the unit costs were reduced by 90%.

Conflux
Heat exchangers can be 3D-printed from high-quality thermally conductive alloys combining various advantageous properties such as flexible design, optimized heat transport properties and reduced size.
Additive manufacturing allowed Conflux to design internal geometries that radically increased the surface area in a given volume. This tripled the thermal heat rejection and at the same time the pressure drop is reduced by two-thirds. Additionally, a compact and new design with a 55 % reduction in length was realized.

TheSys
TheSys is an engineering service provider that develops cooling systems, air conditioning systems and heat exchangers. Together with EOS and AM Metals, they pushed the limits of feasibility to develop a state-of-the-art gaming CPU heat exchanger that was optimized for additive manufacturing in just a week of development.
With the flexible EOS M 290 metal manufacturing system, AM Metals GmbH manufactured a water-cooled heat exchanger that provides the same cooling capacity with just one fifth of the size. Compared to other leading gaming CPU coolers, it is also 76 % lighter.

Complex Design and Flexible Production
Having a stable housing protects the interior. Robust cases are often essential, especially for sensitive electronics. They need to be strong and properly sealed, while also fitting as closely as possible, and they need to be manufactured quickly enough to achieve short production cycles. However, with the injection molding process, manufacturing housings with these properties is only viable in very large series productions.
Industrial 3D printing offers a cost-efficient alternative for the small and medium series production of plastic housings. Whether made from materials with insulating or especially favorable dissipation properties, the additive manufacturing of housings is characterized by cost efficiency, design freedom and functional integration potential.
Whether you want to make prototypes, pilot series or small series productions of housings, additive manufacturing opens up a great deal of potential – not the least of which being lower production costs.
Advantages of 3D Printed Housings
- Integrate functionalities to reduce number of components
- Reduced time-to-market
- Economically attractive manufacturing process
- Produce stable end-use components
To show the video you have to accept marketing cookies.
3D Printed Camera Housing for Outdoor Use
The challenge was to manufacture a low number of units of a robust camera holder with a complex design. The housing needed to be flexible enough to hold six cameras. At the same time, the production process needed to be open to support later design iterations without causing issues.
Thanks to EOS technology, a product design was successfully realized that would previously have been impossible.
The partnership with Freedom360 allowed design changes to be made rapidly. Midwest Prototyping were able to implement cost-effective production in small quantities.
Canto
The developed underwater dive lamp is smaller, lighter and more robust than anything else on the market. Canto succeeded in solving this challenge with a FORMIGA P 110 Velocis using PA 2200 material.
The internal system of the additive manufactured lamp connection, which features a spring latching mechanism, is produced in a single piece. This allowed the number of assembly parts to be reduced from 3 to 1. Weighing just 580 grams, the lamp is setting new standards. As an added benefit, Canto Ing. GmbH were spared the need to manufacture an expensive injection molding tool, which would have cost up to € 35,000.

Reliable & Light, Flexible & Smart
Automation is moving forward, and all types of production and intralogistics processes are becoming increasingly networked thanks to digitalization. Robotics and gripping systems play a key role in this. But gripping technology in particular is constantly facing new challenges. Additive manufacturing makes it possible to address rapidly changing market trends in a targeted manner.
Robotics is no longer just viable for large corporations – SMEs can benefit too. The background: lighter gripping tools designed for smaller, more cost-efficient robots can be placed on the market. As a result, automation solutions require significantly less investment and pay for themselves more quickly. Besides lower costs, a lightweight gripper with the same load capacity supports faster movements and hence shorter cycle times – a central objective in the manufacturing world.
Advantages of 3D Printed Grippers
-
The gripper can be directly adapted to its product using design data
- The extensive design freedom makes it possible to incorporate safety elements and predetermined breaking points
- The method enables intelligent functionality to be integrated directly into the part, which makes sensor technology and process monitoring easier
- Parts are manufactured in a single piece, saving on assembly times
To show the video you have to accept marketing cookies.
Success Story
Tangible Success - Bronchial Gripper with Functional Base Plate
The Wittmann group was looking for a lightweight solution with a flexible membrane to control a pair of gripper tongs by compressed air. The solution needed to incorporate all pneumatic connections and channels directly into the plate itself. After simplifying the design, stable grippers on a functional plate were successfully manufactured in small series production on a FORMIGA P 100.
FESTO
Process safety plays a key role with gripping systems to avoid handling errors. However, grippers that are more flexible are also desirable, allowing them to handle different workpieces. Ideally, production should be monitored in real time to identify any faults or potential optimizations using the recorded data.
Additive manufacturing is the key to integrating additional functionality such as sensors, intelligent valves, or automatically customized suction cups. Hinges, air ducts and sensor mounts can be integrated directly into the design of the gripping system and realized during production. This also eliminates unnecessary assembly steps, reducing the manufacturing costs.

Trinckle & Kuhn-Stoff
Design work costs money and time. Another factor is that the necessary design and CAD expertise may not be easy to acquire. Using gripping systems as an example, trinckle and Kuhn-Stoff teamed up to investigate how an efficient development and design process can be automated without requiring in-depth knowledge of 3D design and CAD.


3D Printed Extraction Gripper
Success Story | SSI Schäfer
Individual special gripper from PA 2200 leads to reduction of set-up time and increase of production time while achieving a wheight reduction by more than 70%.

End-of-Arm for Smarter Packaging
Success Story | Anubis 3D
An innovative, industrial, 3D printed end-of-arm enables Langen Group to lighten the load on their customer’s robotic packaging line.

Polyamide Robotic Hand
Success Story | ASS Maschinenbau
Manufacture of a lightweight robotic hand with integrated air channels from polyamide using the EOSINT P 396.
Additive Part Manufacturing for Turbomachinery
Turbomachinery is indispensable for energy generation. Its high-performance parts feature complex, high-tech designs that need to be more and more robust and powerful as the demand for energy increases. In addition, turbomachinery parts need to be resistant and reliable – even at temperatures beyond the melting point.
The 3D metal printing (DMLS) offers the right technological foundations for implementing an optimized cooling strategy, among other things. Parts can be designed and made to transport and apply energy with increasingly precise focus. Innovative repair processes, for example, are revolutionizing the efficiency of turbomachinery parts by building at worn areas directly on the original part.
Advantages of 3D Printed Turbine Parts

Improve Part Performance
Additive manufacturing allows you to manufacture complex parts with integrated functionality. Lower part costs and shorter lead times can also be achieved by reducing the rejection rate.

Accelerate Development
Directly from CAD data: faster design optimizations and shorter development cycles become possible by building prototypes with 3D printing

Optimize Maintenance
Reduced costs thanks to the ability to repair parts with complex cooling channels, less downtime.

Improve Spare Parts Logistics
Spare parts on request: even small batch sizes can be manufactured cost-efficiency, reducing storage costs.
SUCCESS STORY
Material Solutions & Siemens - Innovative Project Outstanding Results
The collaboration between Siemens, Material Solutions and EOS demonstrates that 3D metal printing is a reliable and proven technology viable even for “moving” applications, without any compromise. In focus: developing a new turbine blade. The part was developed together with Siemens NX, built on EOS systems and produced by Material Solutions.
- Performance increased to 13 000 rpm
- 75 % shorter development time & 50 % quicker lead time
- Can be used with ambient temperatures of up to 1 250 °C
Blades, fuel injectors, burners and combustion chambers, cladding, seals and housings: when manufacturing parts for the energy sector, functional integration and heat resistance are the decisive factors of longevity and process selection. For these factors, industrial 3D printing opens up opportunities beyond the reach of conventional manufacturing processes. The applications range from 3D-printed turbine blades to innovative repair solutions. Find out more on this page about how we’ve broken new ground in turbomachinery together with our customers.
To show the video you have to accept marketing cookies.
SUCCESS STORY
Siemens - Burner Fronts with Functional Integration
Siemens relies on an EOS system to manufacture burner fronts featuring functional integration – redesigned with Siemens NX and manufactured in series on an EOS M 400-4 from EOS NickelAlloy HX.
The part is manufactured as a single piece and no longer has 13 different components Since less material is used, the part is considerably lighter. The lead time is reduced from 26 weeks to 3 weeks. Reduced heating of the metal extends the service life of the part
To show the video you have to accept marketing cookies.
SUCCESS STORY
Siemens - Optimized Maintenance Management Based on 3D Printing
Downtime caused by repairs and maintenance work is a huge cost factor in large-scale energy generation plants. Especially for parts with high complexity and integrated channels, the hybrid repair process based on DMLS opens up unique opportunities to save time and costs. How does it work? Areas that experience wear are reconstructed directly on the original part. This has far-reaching advantages:
- No additional welding steps are required
- Improved quality of the connection between the reconstructed area and the original part
- The alignment of internal structures is preserved
To show the video you have to accept marketing cookies.
A Demanding Task and a Smart Solution
Thanks to a customized EOS system, Siemens found success with a precise and fast maintenance process for burner tips subject to high thermal stress in gas turbines. The repairs are performed by building directly onto the worn material, saving time and cost.
- Repair times were reduced by 90 %
- Repair process became significantly more streamlined
- Technical improvements can be incorporated during repairs
Euro-K
The new burner is able to use gaseous and liquid fuels equally effectively. The new, optimized geometry also allows the use of liquid fuels that are classified as difficult to burn, such as fusel oils that are created from the distillation of alcohol. Another positive effect is that the burner’s innovative design allowed the size of the combustion chamber to be reduced by 20%.

Everything You Need for Turbomachinery Parts From a Single Source
We offer robust systems with repeatable part quality and a wide portfolio of materials, capable of handling diverse applications, including those involving high temperatures. To complement this, we also offer tools and software for comprehensive quality monitoring and a consulting department to take care of your needs.