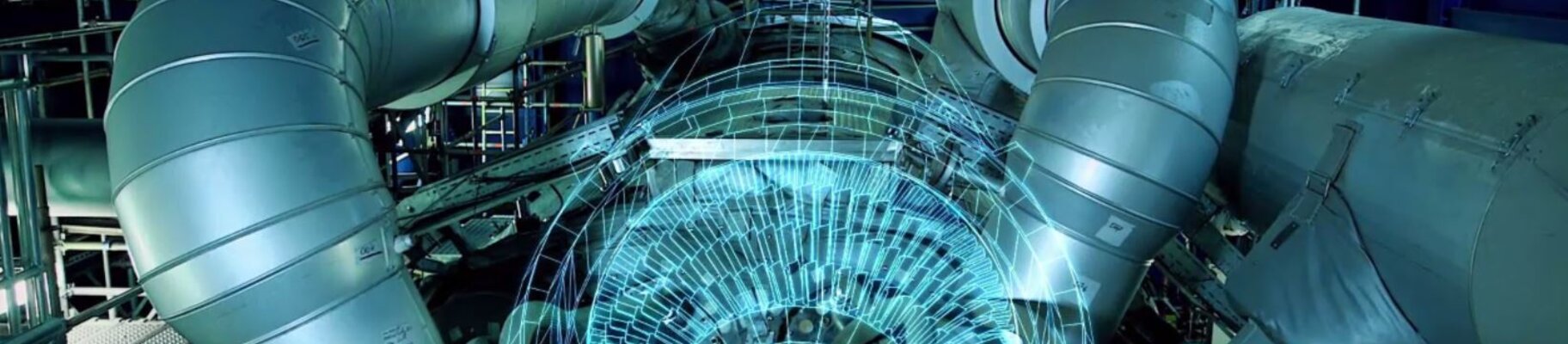
高性能産業用ガスタービンの3Dプリンティング
シーメンス|成功事例
スウェーデンに本社を置くSiemens ENERGY社は、産業用および石油・ガス用途の発電用ガスタービンを製造しています。シーメンスの産業用タービンの性能範囲は15~60MWです。シーメンスの子会社は、建設だけでなく、これらの卓越したエンジニアリングの長期サービスとメンテナンスも提供しています。メンテナンスコストの削減を支援するため、シーメンスはEOS技術と設備を活用したアディティブ・マニュファクチャリング技術の開発と導入に取り組んでいます。
「アディティブ・マニュファクチャリングは、統合された設計と製造の利用において、私たちに新たな次元を切り開きます。この技術によって、産業用ガスタービンの部品の製造と修理が、以前よりもはるかに迅速に行えるようになりました。同時に、部品の機能性と性能も向上しています。」
Dr. Vladimir Navrotsky|Siemens Energy Service|技術・イノベーション部門責任者|オイル&ガスおよび産業用アプリケーション
課題
ガスタービンは、空気流入口、コンプレッサー、燃焼器、タービン、高温ガス排出口で構成されてます。エンジンを通過する空気はコンプレッサーで圧縮される。燃焼室では、圧縮された空気が燃料と混合され、流れの運動エネルギーを増大させるために燃焼されます。タービンでは、流れの運動エネルギーが機械エネルギーに変換されます。この機械エネルギーは、ガスタービンのコンプレッサーと発電機(発電)、またはその他の駆動装置(パイプラインを通じてガス/オイルを圧送するコンプレッサーなど)を回転させるために使用されます。運転中、エンジンの高温ガス経路にある部品(ブレードやベーンなど)は、時には1,000℃を超える高温にさらされるため、ホットガス経路の構成部品が高水準で摩耗します。
これは、燃料と空気の混合気の点火が行われるバーナー先端部にも当てはまります。ここでは、消耗の影響がはっきりと見られ、測定することができます。メーカーは、バーナーの修理が必要となる所定の運転期間を設定するため、厳格なテストを実施しました。
従来の修理方法では、バーナー先端の大きな部分を事前に製作する必要がありました。
この事前に製作されたプレハブユニットは、所定の運転時間後にバーナーチップを交換する(古いものを切り取り、プレハブユニットを溶接する)ために使用されます。従来の修理手順では、多くのサブプロセスや検査が必要となり、時間がかかることがありました。修理手順の簡素化とスピードアップを図るため、シーメンスではアディティブ・マニュファクチャリング技術が導入されました。

ソリューション
このような作業を行うには、革新的なパートナーが必要です。シーメンスは、EOSにそれを見いだしました。EOSは、適切なアディティブ・マニュファクチャリング技術を持っているだけでなく、短期間で、社内のマシンの1つであるEOSINT M 280を金属加工用に個別に適合させることができました。

特に、800mmバーナーを搭載するために機械内部のスケールを拡大する必要がありました。メーカーは、カメラシステムや光学測定システムなどのハードウェア・コンポーネントも改良し、ソフトウェアにも対応する調整を行いました。EOSは、EOSINTシステムの大規模な改造を1年以内に実施しました。
当初から、このアプローチが利益をもたらすことは明らかでした。バーナーチップの大部分を交換するのではなく、シーメンスは損傷した材料だけを取り除くことから始めました。さらに、修理の際、旧型のバーナーを最新の設計に作り直すことができました。つまり、古いバージョンのバーナーを修理するだけでなく、改良することも可能になったのです。
結果
数値、データ、事実は、新しい修理プロセスの成功を明確に物語っています。 Siemens ENERGYは、中心的な課題である修理期間の短縮に大きな影響を与えることができるでしょう:事業者にとっても、タービンを迅速に運転に復帰させることは同様に重要です。これはまた、修理プロセスやメンテナンスに関するコスト削減の可能性を広げることにもなります。
シーメンスは、自社の修理プロセスを改善するだけでなく、顧客にも戦略的なメリットを提供できるようになりました:この新しいプロセスにより、専門家はコンポーネントを修理プロセスに組み込むことで、タービン技術を改善することができます。この新しいプロセスのおかげで、専門家はコンポーネントを修理工程に組み込むことで、タービン技術に改良を加えることができるのです。こうすることで、たとえタービンが長年使用されていたとしても、事業者は最新技術を利用することができます。
Siemens Energy Service、オイル&ガス、産業用アプリケーション部門の技術・イノベーション責任者であるDr. Vladimir Navrotskyは、次のように要約します:「この新しい修理技術によって、高精度の作業をより迅速に行うことができるようになります」。
このプロジェクトを重要な成果と捉えているのは、スウェーデンのシーメンス子会社だけではありません。「私たちの技術を修理分野に押し上げることに成功しました。私たちは、顧客固有の要件に合わせてシステムを迅速に変更できることを示しました。このケースでは、ハードウェアとソフトウェアの両方に対する修正が重要でした。最終的な結果だけでなく、それを達成するまでの道のりも含めて、関係者全員が満足して振り返ることができます」とEOSのStefan Oswaldは語っています。

結果の概要
- 革新的:古いバーナーバージョンも、最新の技術水準に素早く対応させることができる。
- 費用対効果:初期段階ですでにコスト削減の可能性が見られる
- 修理に要する時間を90%短縮
EOS成功事例
EOSの30年にわたる3Dプリンティングのパイオニアとしての卓越性をご覧ください。