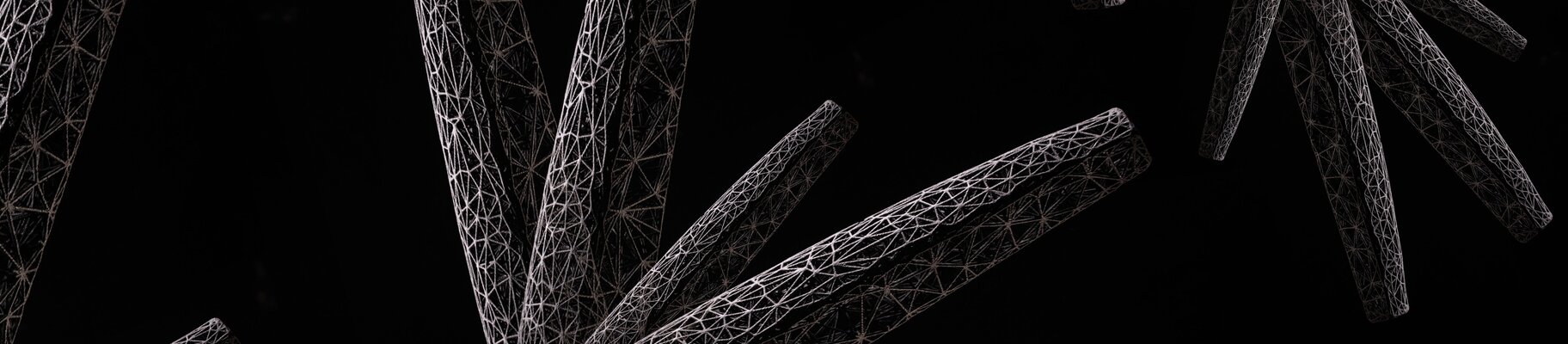
Lighthouse project launched for production of spare and series parts
German Federal Ministry of Education and Research funds POLYLINE with 10.7 Mio. Euro – Kick-off Meeting of the Consortium for the Automation of Additive Manufacturing in the Automotive Industry.
____ Krailling, Germany, May 5, 2020
The POLYLINE project brings together 15 industrial and research partners from Germany to develop a next-generation digitalized production line. This line will be used to produce plastic parts for the automotive industry. The aim is to complement conventional production techniques (e.g. machining, casting, etc.) with additive manufacturing (AM) in the form of high-throughput line production line systems. The project is funded by the German Federal Ministry of Education and Research with a total of 10.7 Mio. Euro. The project has a duration of three years. POLYLINE was officially launched with the kick-off meeting of all consortium partners on 4 March 2020 at EOS in Krailling near Munich.

Background of the POLYLINE project
Additive manufacturing can realize almost any geometry and even complex structures without significant additional effort - a big step towards mass production of individualized products. At present, however, both vertical and horizontal integration of additive manufacturing processes in conventional lines can only be implemented to a limited extent due to the lack of standards across process chains. This is due to AM-specific workflows (e.g. production time in the "batch process") and the generally low level of automation of the physical handling and transport processes.
On the other hand, the digital data chain along the horizontal process chain is not continuous at many interfaces, which currently leads to a lack of transparency, susceptibility to errors and limited monitoring along the process chain and makes integration into relevant production control systems more difficult. These obstacles limit the obviously high potential of additive manufacturing processes in existing series production and assembly lines.

From flexible solutions for prototyping
to scalable additive production chains
In order to achieve the project objective, the project aims at a digital and physical system breakthrough. To achieve this, it is important to record and document all central characteristic values and quality criteria (including identification, history and measured values) from the CAD model to the final part. The individual sub-processes of production - from process preparation to the selective laser-sintering process, cooling and unpacking as well as cleaning and post-processing - will be automated and integrated into the planned production line, in which all the technological elements of an SLS production chain will be fully linked for the first time.
POLYLINE uses a new solution approach that takes a holistic view and implements all required processes. The targeted production line is planned to be implemented with a high degree of maturity according to the requirements of the application partner. The use cases include customized components as well as serial components in large quantities.
In order to establish additive manufacturing as a real process alternative for series production, the German Federal Ministry of Education and Research is funding the project with a total of 10.7 Mio. Euro. The project is part of the funding measure "Line integration of additive manufacturing processes" as part of the funding program "Photonics Research Germany - Light with a Future". POLYLINE is led by EOS, the world's leading technology provider in industrial 3D printing of metals and plastics.