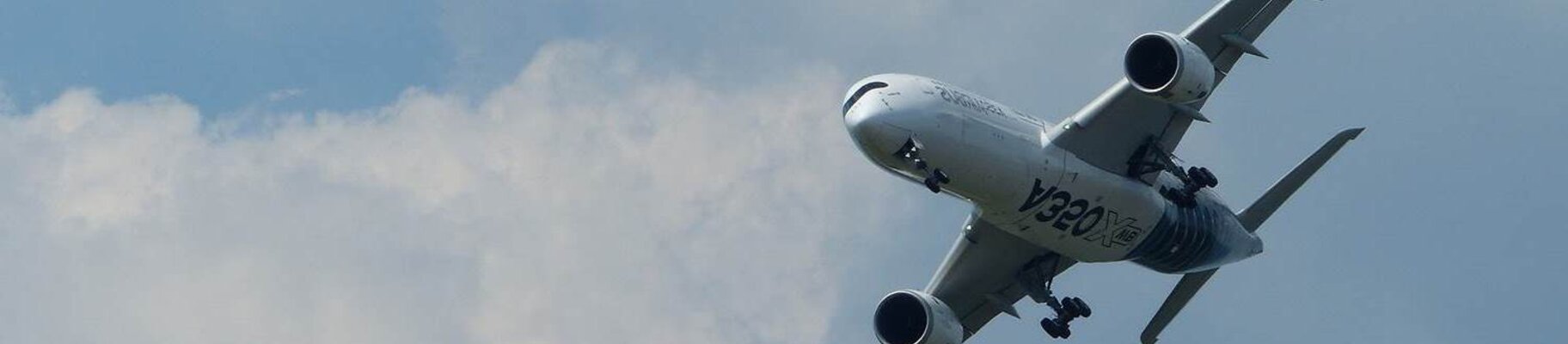
新型エアバスA350 XWB向けSogeti のハイテクアディティブ・マニュファクチャリング
A350 XWBのケーブルルーティング - 2週間でデザインからコンポーネントまで|成功事例
まったく新しい民間航空機が初めて空を飛ぶ瞬間は、常に特別なものであり、エアバスA350 XWBは特にそうでした。新しい時代に生きる者として、開発作業が革新的な素材と製造プロセスに焦点を当てることは当初から明らかでした - ゴールは世界で最も効率的な航空機を製作することでした。未来の技術として、アディティブ・マニュファクチャリングも開発中に考慮すべき可能性のひとつでした。パイロット・プロジェクトの一環として、Sogeti High Techの専門家は、旅客機の垂直尾翼のフロント・スパーにケーブル・マウントを記録的な速さで開発することに成功しました。初期のスケッチから製品完成まで、たった2週間を要しただけでした。EOSの技術と専門知識は、この開発プロセスにおいて極めて重要な役割を果たしました。
「既存の部品をわずか2週間で "AM-ready "にするということは、最初の試みで成功しなければならないということでした。EOSとの優れた積極的な協力関係が、この野心的なプロジェクトを可能にし、素晴らしい結果をもたらしました。」
Carlos Ribeiro Simoes|アディティブ・マニュファクチャリング・オファリング・リーダー|Sogeti High Tech
課題
アディティブ・マニュファクチャリングによる、A350の垂直安定板のカメラ用ケーブル配線マウントの時間的制約のある開発と製造
このプロジェクトでは特に、エアバスの最新モデル用のケーブル配線マウントの製作を含みました。このマウントは最終的に、垂直安定板に設置されたカメラの電源供給とデータ転送のために必要となりました。このカメラは乗客には外の景色を、パイロットには地上の方向を提供するものです。
製品要求文書では、量産に適した機能的に動作可能なコンポーネントが求められていました。このタスクは、Cap Gemini S.A.の完全子会社で、パリ証券取引所に上場しているSogeti High Techに任されました。
このケースで特に難しかったのは、リードタイムが2週間と短かったことです。開発全体をこの期間内に完了させなければなりませんでした:部品と現在の設置状況の分析から、トポロジー最適化のためのパラメータの検討とその適用、そして最終部品の設計と製造までを目的としたものでした。また、架台は後処理を避けるため、サポート構造をできるだけ少なくする必要がありました。
さらに、このコンポーネントの仕様では、スナップオンケーブルホルダーの統合、軽量化、その後の航空業界認証の厳しい要件への適合が求められました。
従来工法で製作された部品は、成形されたシートメタル部品と多数のリベット - トータルで30以上の部品 - で構成されていました。上部のプラグコネクターはプラスチック製で、マウントの他の部品とは材質が異なっていました。本プロジェクトの目的は、プラグコネクターも含めた単一部品からなる統合ソリューションを開発することであり、それによって製造と設置にかかる時間を大幅に短縮することでした。アディティブ・マニュファクチャリングの軽量化目標は、トポロジー最適化に基づくパラメータの検討によって決定されました。
ソリューション
部品点数を1点に絞り、EOS M 400で製造することで、製造時間を19時間に短縮
Sogeti High Techは、この新しい部品のために、付加的に製造する部品を設計するための試行錯誤の開発プロセスに従いました。このプロジェクトは、新しい製造プロセスに関して、従来工法で製造された既存の部品の分析から始め、非常に良好な結果が得られました。この部品の機能性、素材、以前の複雑な構造は、EOSのパウダーベッドベースの3Dプリンティング技術の理想的な候補となりました。この技術が提供する設計の自由度により、複雑な構造を1つのピースで製造することができ、機能的な統合をおろそかにすることなく、軽量化設計ができました。
この解析によって、いわゆるデザインスペース(ケーブル配線マウントが占める可能性のあるスペース)を定義することができました。材料には、薄肉で複雑な構造に最適なアルミニウム合金AlSi10Mgが選ばれました。外部領域とのインターフェースはそのままで、デザインスペースを形成しないため、変更は必要ありませんでした。定義された荷重は、パラメータ検討におけるトポロジー最適化の境界条件とされ、新しい設計の基準としました。
トポロジーの最適化計算にはCAEソフトウェアが使用されるのが通例ですが、今回の再設計には、自由曲面を持つ構造物の設計に特化したソリューションが使用されました。Sogeti High Techは、設計そのものを行いました。2週間というリードタイムに間に合わせるため、EOSはソフトウェアEOSPRINTを使用して、トポロジー最適化の結果から製作時間と最適化されたパラメータを計算しました。これにより、製造プロセスの可能性と限界、およびサポート構造を避ける必要性を考慮しながら、製造部品にCAEを導入しました。
「卓越したハードウェアに加え、EOSは付加製造部品を実現するための包括的な専門知識-私共が非常に高く評価しているもの- も提供しています。」
Carlos Ribeiro Simoes|アディティブ・マニュファクチャリング・オファリング・リーダー|Sogeti High Tech
結果
Sogeti社とEOS社の協力により、DMLS技術による設計の自由度を十分に活用しながら、同時にその制約も考慮した、アディティブ・マニュファクチャリングに最適化されたコンポーネントを開発することができました。これにより、ケーブル配線用のプラグコネクタを設計に組み込むことができ、構造を最適化するために特定の重要な部分に局所的な補強を組み込むことができました。部品内の開口部と支柱をサポートレスの形状にすることで、労力、ひいては後処理コストを最小限に抑えることができます。
さらに、マウントは必要なときにいつでも極めて迅速に製造できます。層厚90μmのEOS M 400で製造する場合、従来は70日を要していたものが、わずか19時間で済みます。
これは、90%をはるかに超える生産時間の短縮に相当します。この主な理由は、多くの個別の工程と、以前は30個あった部品が、今では1回の造形で製造できる中心的な部品にまとめられたからです。さらに、個々の部品は、高価になりがちな組み立てや在庫を持つ必要がなくなりました。部品アセンブリ全体の保管も、より簡単になりました。
ソゲティは製造だけでなく、開発においても膨大な時間を節約することができました。最初のスケッチから完成部品までの全工程に要した時間はわずか2週間です。これは驚異的なリードタイムであると同時に、この設計は重量効率の大きな向上も意味します。
既存工法で製作された従来のケーブルマウントが452グラムに対し、付加的に製作されたものが317グラムの重量です - 航空業界では、燃料消費を最小限に抑えるため、1グラム1グラムを重要視していることはよく知られています。顧客であるエアバスは、この結果に十二分に満足しています。
結果の要約
- -29 単一部品の機能統合
- -生産時間を90%短縮
- -135グラムの軽量化
もっと見る
EOSの30年にわたる3Dプリンティングのパイオニアとしての卓越性をご覧ください。