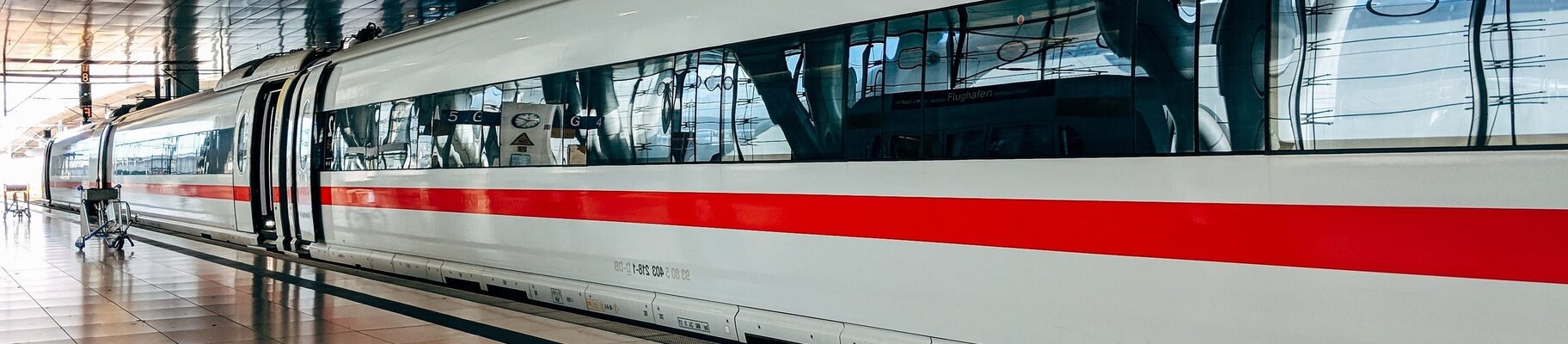
The Fast Track to 3D Printed Custom Train Parts With Additive Manufacturing by EOS
Hasenauer & Hesser | Success Story
Deutsche Bahn Chooses Additive Manufacturing to Maintain Its Trains
The fleet of third-generation ICE trains operated by Deutsche Bahn features just under 160 units from various production series. Every single one of them still looks and feels modern, thanks to their stylish design and regularly refurbished interiors. Despite this, the transportation industry views anything built before 1996 as a youngtimer. As with automobiles from this period, finding spare parts for these trains can be tricky. Yet Deutsche Bahn remains unfazed, armed with industrial 3D printing technology by EOS.

"The enormous advantage of additive manufacturing is that we can always manufacture replacement parts that are as good as new, allowing us to keep our trains properly maintained for decades. We do not have to compromise on quality or performance. The cost is also lower than custom molds."
Florens Lichte | Head of 3D Printing | DB Fahrzeuginstandhaltung GmbH
Challenge
Third-generation ICE trains are somewhat daunting. With an unladen weight ranging from 270 tons to well over 400 tons travelling speed of 140 to 190 miles per hour, the sheer variety of components aboard each train is easily overlooked. The smallest components are often the most difficult. Whereas standard commercial screws are easy to replace, many other small custom-made products cannot simply be reordered from the manufacturer if they wear out or fail. For some parts, production has been discontinued; for others, the manufacturers are insolvent. Only a few copies of each part are typically required. High tool costs and minimum purchase limits make them uneconomical to manufacture using conventional methods.
A batch of 160 units is tiny compared to industrial-sized orders. By comparison, hundreds of thousands of medium-sized vehicles are manufactured annually; even for aircraft, yearly production numbers can reach several thousand for successful short- and medium-haul models.
Although this certainly demonstrates the sustainability of trains as a means of transportation, the small production scales complicate the production and warehouse logistics of spare parts. Similar problems are encountered with many other specially made components. In the specific example considered here, replacement parts were needed for some very delicate fluorescent tube fixtures for display lights inside the electronic onboard information system of ICE-3 and ICE-T trains. The monitors display information about the speed, time of day, and upcoming station to passengers.
Over time, standard wear-and-tear and brittleness gradually weaken the 9.4 x 0.4 x 0.3 inch injection-molded parts, meaning that they need to be replaced every 10 to 15 years. Rail vehicles are designed to have a service life of over 25 years, but it is not uncommon for a train to remain in service for 40 to 50 years, or even longer in exceptional cases. Despite this, the supplier decided to discontinue these parts. Around 40 units are needed per year. The maintenance company entrusted with this responsibility, the Electronikzentralwerk (EZW) in Munich/Germany, embarked upon a search for alternatives or partners who might have answers. This search led their railway technology experts straight to additive manufacturing and the possibilities that it offers.

Solution
Additive manufacturing technology is the perfect solution, given the small batch sizes involved. It does not require extensive preparatory work, e.g. to set up the manufacturing tools. “Based on our experience, we would expect a solution based on an equivalent aluminum mold and manual unloading to cost several thousands of euros, even before handling and set-up costs for each order, and yearly storage and maintenance costs for the molds. Furthermore, the molds would take around three months to make, and the first samples would require yet another month after that," explains Florens Lichte, Head of 3D Printing at DB Fahrzeuginstandhaltung GmbH.
If a company wishes to additively manufacture a component, they do not need to acquire their own industrial 3D printers or develop their own expertise—the business model of contract manufacturers benefits everyone. This was the path chosen by Deutsche Bahn. Their logistics company has now collaborated with Hasenauer & Hesser GmbH successfully on multiple occasions. But the devil was in the detail, reveals Hans-Jörg Hesser, Managing Director at Hasenauer & Hesser GmbH: “Our primary objective was to preserve the component's functionality. To do this, the specifications of the component had to be re-engineered and adapted to the layered manufacturing process. 3D printing is usually easy, but this project demanded massive experience. The component used in the ICE trains is long, narrow, and thin walled. Because of this, it warps incredibly easily. Positioning the parts within the building chamber was essential, especially since we wanted to make over 200 fixtures at the same time for this order."

"We have over 10 years of additive manufacturing experience and we've been using EOS systems for as long as we can remember. We are delighted with the component quality and system reliability. They allow us to deliver first-class spare parts to our customers in good time."
Hans-Jörg Hesser | Managing Director | Hasenauer & Hesser GmbH
Results
The fixtures were built with the FORMIGA P 110. Since neither 3D CAD data nor design drawings were available, the re-engineering step incurred expenses in the lower four-digit range. The manufacturing costs were then over 80 % lower than those of injection molding. The project required a total of one month, from start to first delivery, meaning that the 3D printed parts were available four times more quickly. Any follow-up orders could potentially be completed within 24 hours. Employees from EZW Munich themselves tested the printed parts on-site for form, fit, and function. The results were highly convincing: the additively remanufactured fixtures met every single one of the client's requirements. “The parts were a perfect fit and did not warp. We have already fitted at least 20 units," adds Florens Lichte.
However, Mr. Lichte and his colleagues in Germany had more to worry about than just passing the functional tests. Any plastics intended for use in the railway industry must satisfy the fire protection requirements defined in EN 45545-2 / DIN 5510-2 (for existing vehicles). Different sets of requirements exist with additional exceptions in some cases depending on each component's size as well as its weight, location within the vehicle, and distance from other components. The EOS material PA 2210 FR selected for this project needed to be subjected to extensive fire testing to ensure that it meets the specific requirements of its purpose of application. These new parts not only keep passengers updated, they keep them safe as they hurtle along the tracks at breakneck speeds.
The Results at a Glance
- 75 % Reduction of production time
- 80 % Reduction of production costs
EOS Success Stories
Explore three decades of pioneering 3D printing excellence with EOS