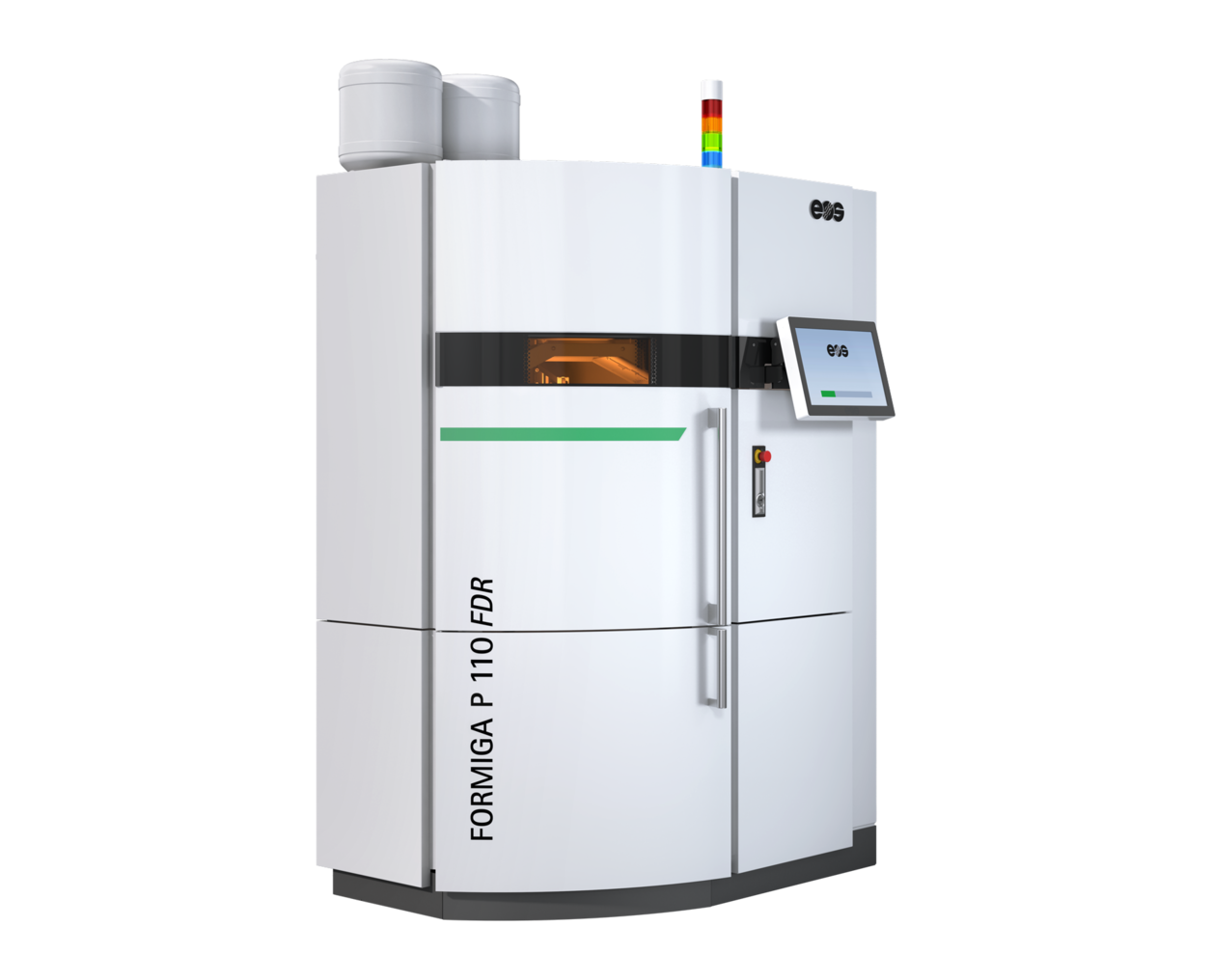
POLYMER SOLUTIONS
FORMIGA
P 110 FDR
- With a focus diameter twice as small as existing SLS technologies, the ultra-fine and precise laser beam produces parts with wall thicknesses of only 220 µm.
- The system ensures reproducible part properties throughout the defined build volume, for every build and from machine to machine.
- The smart temperature management and an improved exchange frame contribute to homogenous part quality.
- Parts are fully functional right after unpacking, leveraging the smooth surface finish created by the ultra-fine laser to save time in post-processing.
- Parts made with the biobased PA 11 material have high impact resistance and elongation at break. A carbon-neutral version is also available.
- Full integration into the IIoT environment with EOSCONNECT Core resulting in an entirely digital process chain from the CAD model, through ERP and MES connection, to the finished part.
- The system is user-friendly, requires low maintenance and minimal accessories.
FORMIGA P 110 FDR
The Next Big Thing for Small Parts: Maximum Detail Resolution Enables New Fields of Application
The reputable and reliable industrial 3D printer is now operating with a one-of-a-kind fine laser beam to produce delicate parts and ultra-smooth surfaces to enable new fields of applications. The system has both a small footprint and state-of-the-art workflow-based software to maximize your shop floor space while bringing your production to the next level.
EXPOSURE MODULE
LASERS
- 1 x
40 W
SOFTWARE
-
EOS SYSTEM SUITE EOS System Suite optimizes production by streamlining processes, integrating with MES and shop-floor IT systems, and generating detailed quality reports.
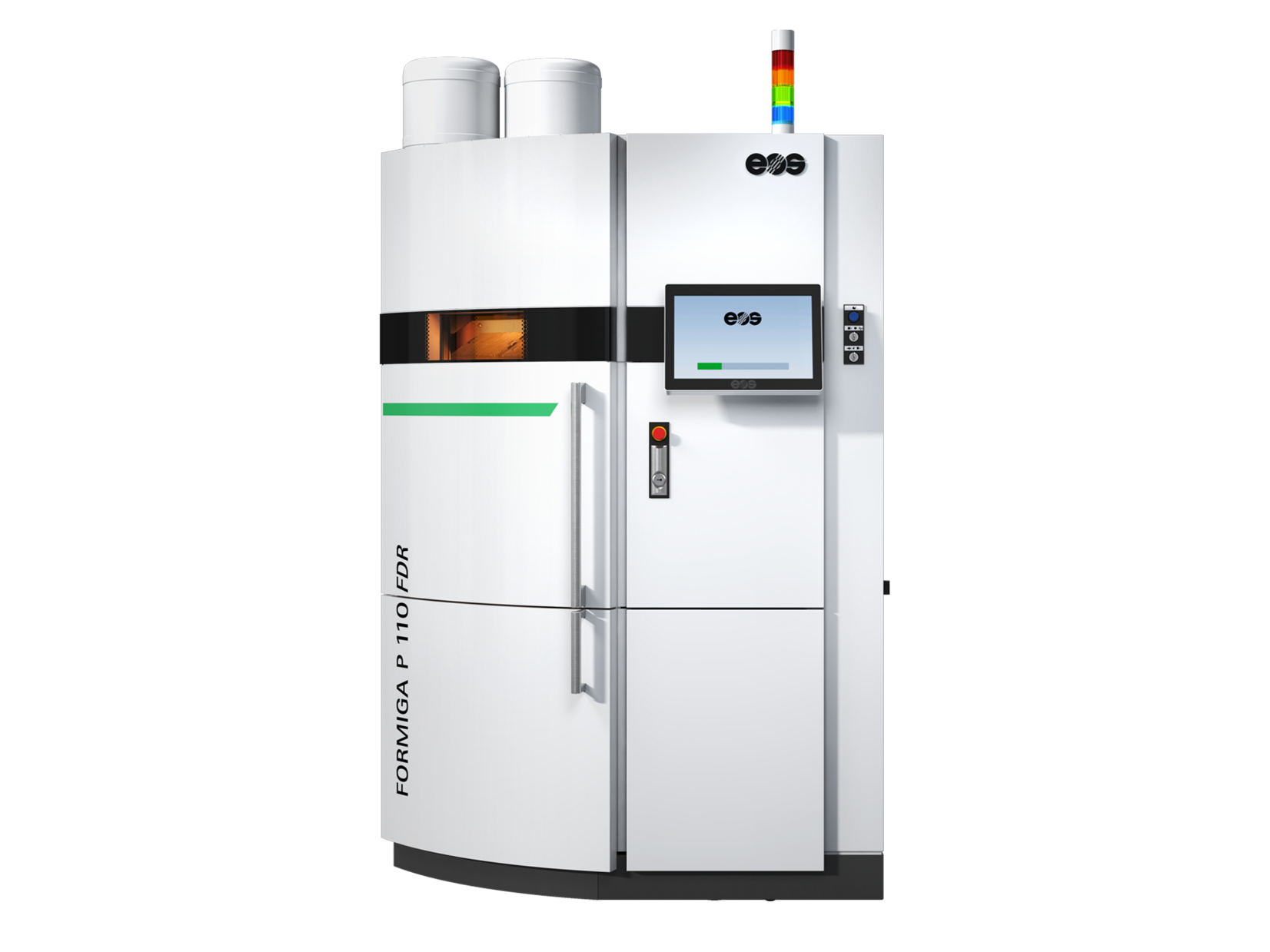
FORMIGA P 110 FDR
TECHNICAL DATA
BUILD VOLUME | 200 x 250 x 330 mm (7.9 x 9.8 x 13.0 in) |
LASER TYPE | CO; 1 x 40 W |
SCAN SPEED | up to 5.0 m/s (16.4 ft/s) |
POWER SUPPLY | 1 x 16 A |
POWER CONSUMPTION | max. 5.0 kW / typical 3.0 kW |
MATERIALS & PROCESSES
EOS has exceptional materials expertise and a comprehensive portfolio of highly developed materials for additive manufacturing. Our materials, systems and process parameters fit together optimally. With the right materials, you can realize the desired property profiles in the best possible way for your products
FORMIGA P 110 FDR
-
PA 1100
-
PA 1101
-
PA 1101 ClimateNeutral