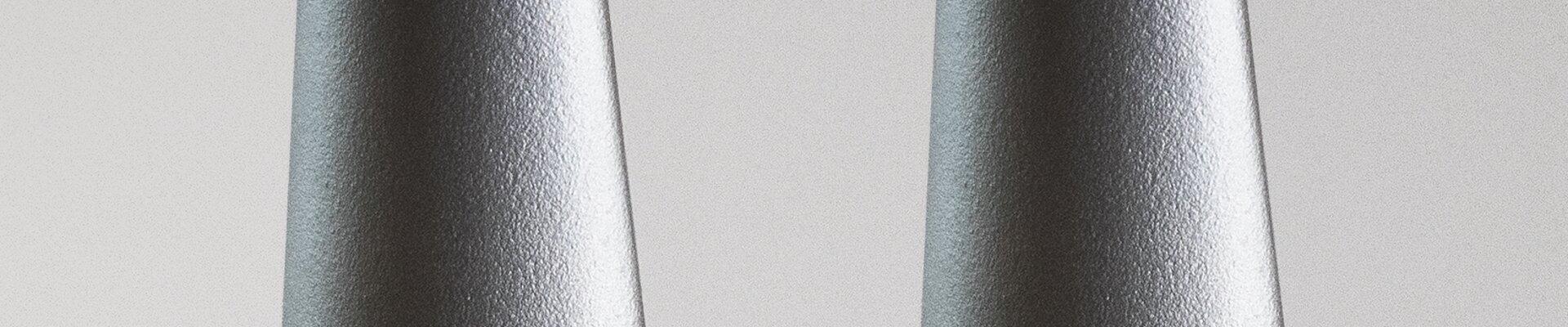
EOS NickelAlloy IN738
Material Data Sheet
EOS NickelAlloy IN738
Superalloy for use in high-stress and high-temperature applications
EOS NickelAlloy IN738 is a high strength nickel-base superalloy for use in high stress and high temperature applications. The composition of the powder has been modified to improve AM processability without compromising the superior strength and creep performance of the alloy. EOS NickelAlloy IN738 is suitable for use in high temperature structural components for various kinds of turbomachinery.
- High strength at high temperatures
- Excellent creep resistance
- Excellent oxidation resistance
- Gas turbine components
- Rocket engine turbo pumps
- Marine and automotive turbochargers
The EOS Quality Triangle
EOS incorporates these TRLs into the following two categories:
- Premium products (TRL 7-9): offer highly validated data, proven capability and reproducible part properties.
- Core products (TRL 3 and 5): enable early customer access to newest technology still under development and are therefore less mature with less data.
All of the data stated in this material data sheet is produced according to EOS Quality Management System and international standards
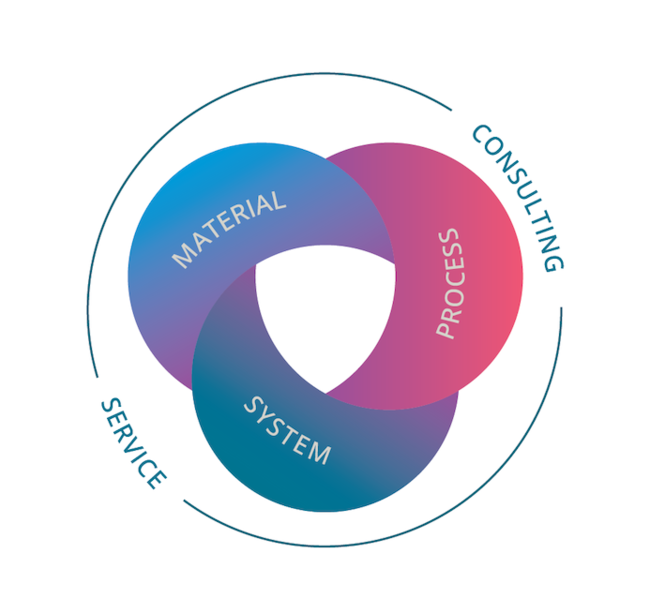
POWDER PROPERTIES
Powder and built part compositions are based on AMS 5410C.
Powder Particle Size
GENERIC PARTICLE SIZE DISTRIBUTION | 20 - 63 μm |
---|
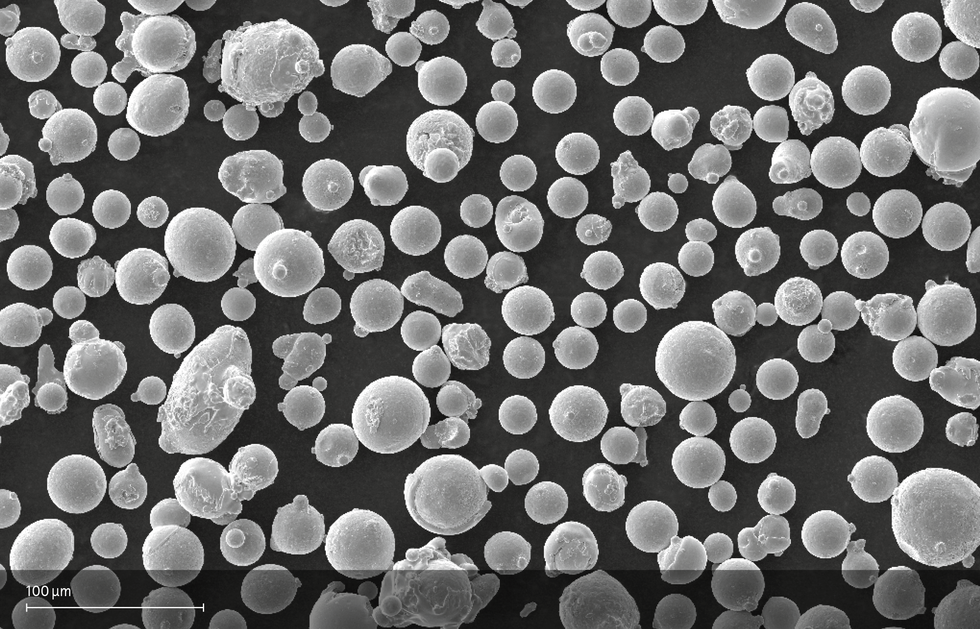
SEM micrograph of EOS NickelAlloy IN738 powder
HEAT TREATMENT
EOS NickelAlloy IN738 is susceptible to formation of macrocracks upon heat treatment, dependant on part geometry. Following are recommendations to mitigate the risk of macrocrack formation: (1) shot peening of parts prior to heat treatment; (2) a combined stress relieve and solution treatment plus HIP treatment using pre-pressurization. Detailed information on the heat treatment can be found in application note.