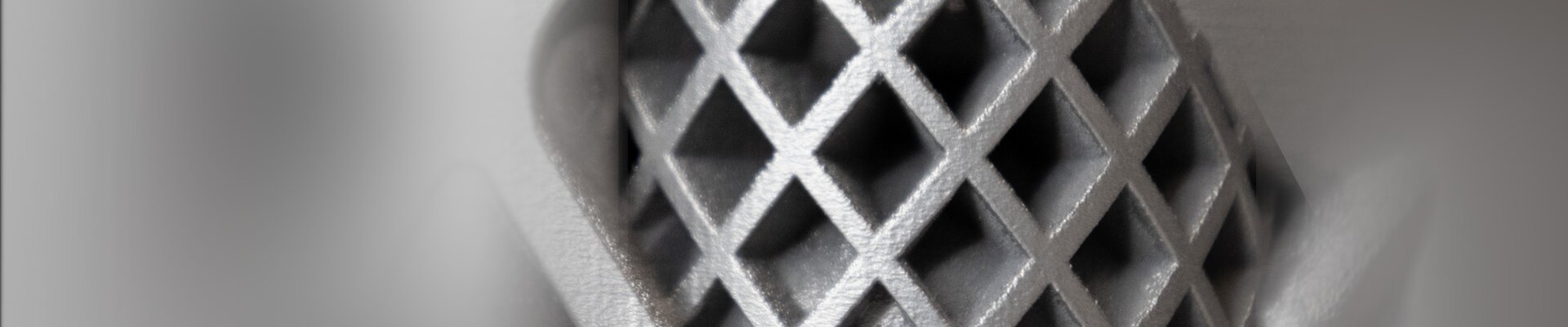
EOS NickelAlloy IN718 API
Material Data Sheet
EOS NickelAlloy IN718 API
IN718 Alloy According to Oil and Gas Industry Standard
EOS NickelAlloy IN718 API is a nickel-based alloy designed to meet the rigorous standard of the oil and gas industry. Parts printed using this alloy have high tensile ductility and excellent corrosion resistance.
- High impact toughness at low temperatures
- High tensile ductility
- Excellent corrosion resistance in typical oil and gas environments
- Available in 10 kg drum and 500 kg Big Bag packaging
- Piping, tubing, and manifolds for downhole applications
- Pumping, separation, and injection equipment
- Fixtures and fasteners
The EOS Quality Triangle
EOS incorporates these TRLs into the following two categories:
- Premium products (TRL 7-9): offer highly validated data, proven capability and reproducible part properties.
- Core products (TRL 3 and 5): enable early customer access to newest technology still under development and are therefore less mature with less data.
All of the data stated in this material data sheet is produced according to EOS Quality Management System and international standards
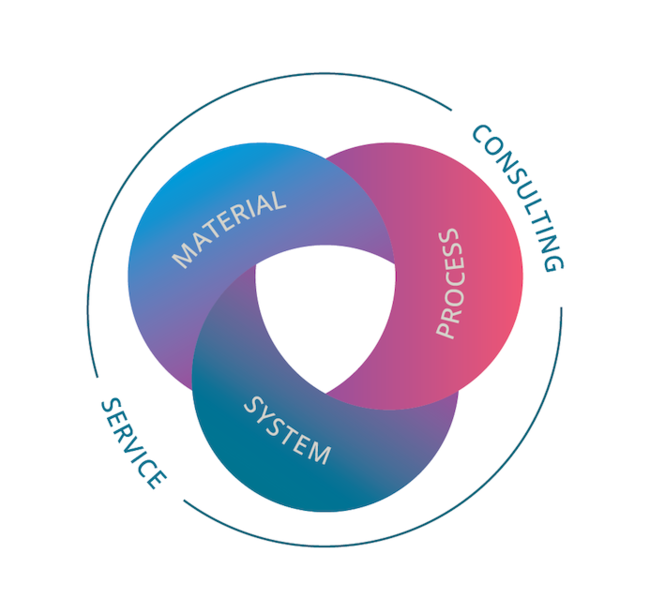
POWDER PROPERTIES
Powder and built part compositions meet the chemical composition requirements of API 6ACRA standard.
Powder Chemical Composition (wt.-%)
Element | Min. | Max. |
---|---|---|
Fe | Balance | |
Ni | 50.0 | 55.0 |
Cr | 17.0 | 21.0 |
Nb + Ta | 4.87 | 5.2 |
Mo | 2.8 | 3.3 |
Ti | 0.8 | 1.15 |
Al | 0.4 | 0.6 |
C | - | 0.045 |
Co | - | 1.0 |
Mn | - | 0.35 |
Si | - | 0.35 |
P | - | 0.01 |
S | - | 0.01 |
B | - | 0.006 |
Cu | - | 0.23 |
Pb | - | 0.001 |
Se | - | 0.0005 |
Bi | - | 0.00005 |
Ca | - | 0.003 |
Mg | - | 0.006 |
Powder Particle Size
GENERIC PARTICLE SIZE DISTRIBUTION | 20 - 55 μm |
---|
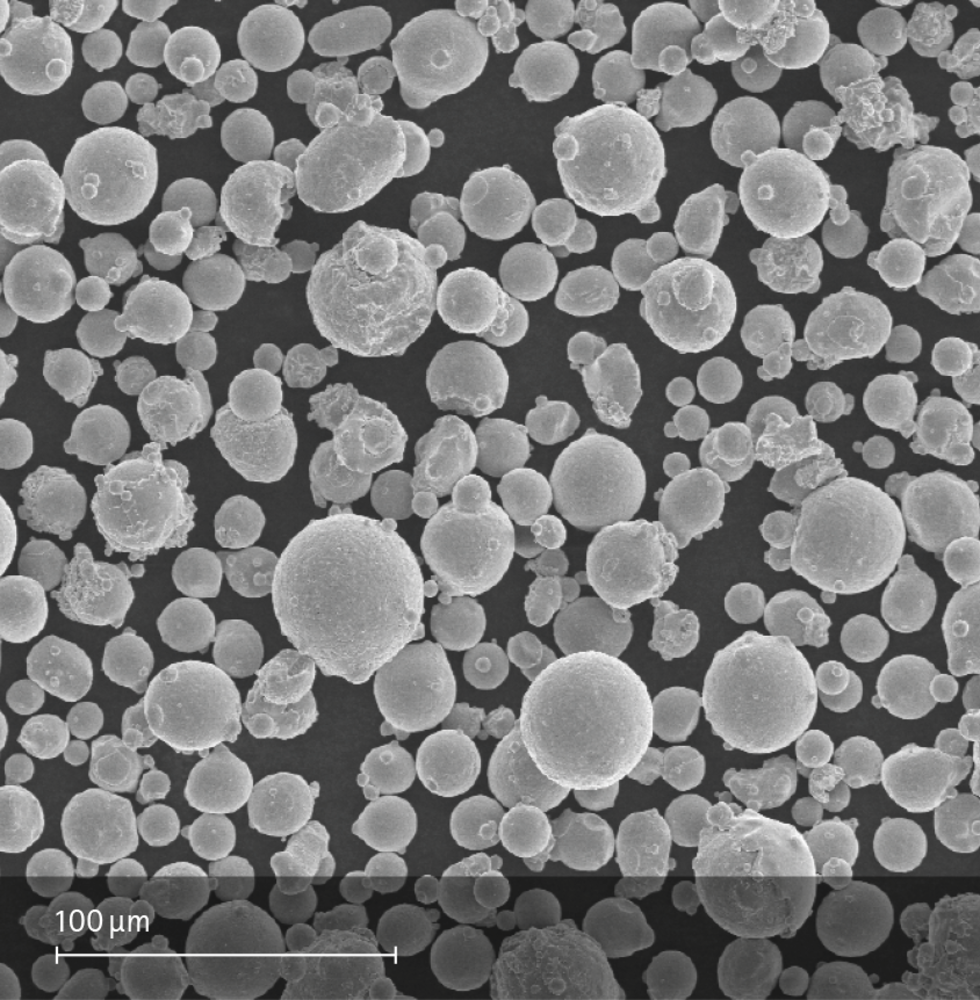
HEAT TREATMENT
Heat treatment includes solution treatment, rapid quenching and aging steps. Developed according to data from: (i) standard "API 6ACRA, Age-hardened Nickel-based Alloys for Oil and Gas Drilling and Production Equipment (Houston, TX: American Petroleum Institute, 2015)", (ii) literature and (iii) test runs made at EOS. Detailed information on the heat treatment is available in the application notes.
Step 1:
Solution Treatment: 1060 °C ±10 °C, 120 min.
Quenching: forced Ar-gas quenching with rate 130 °C/min (1060-300 °C).
Step 2:
Aging: 815 °C ± 5 °C, 360 min. Forced Ar-gas cooling with rate ~25 °C/min (815-300 °C).