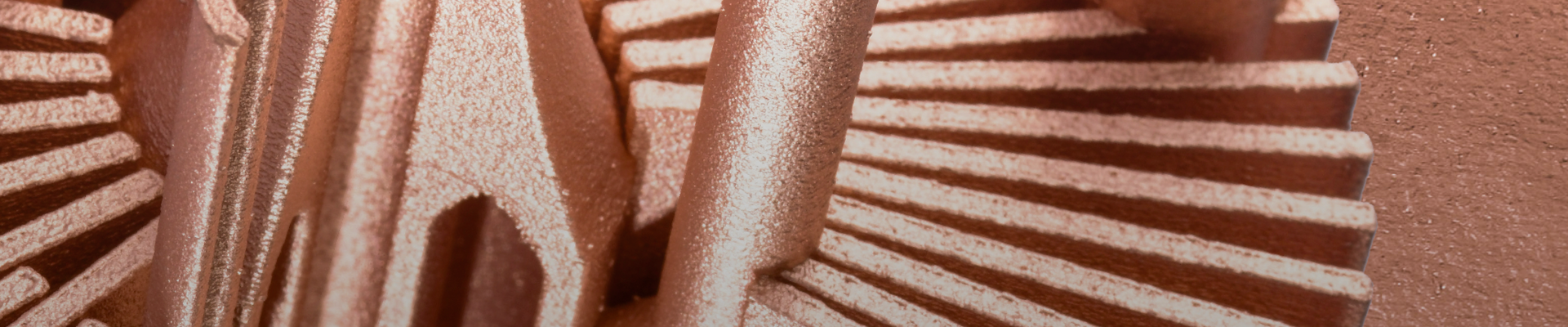
METAL SOLUTIONS
EOS CopperAlloy CuCrZr
Material Data Sheet
EOS CopperAlloy CuCrZr
EOS CopperAlloy CuCrZr has a favorable combination of electrical and thermal conductivity accompanied with good mechanical properties. This alloy reaches its good properties during heat treatment.
- High productivity 12 mm3/s with 80 µm layer thickness
- Moderate to high conductivity in heat treated condition together with good mechanical properties
- Chemical composition corresponds to C18150 and CW106C
- Available in 10 kg drum and 400 kg Big Bag packaging
- Rocket engine parts
- Heat exchangers
- Induction coils
The EOS Quality Triangle
EOS uses an approach that is unique in the AM industry, taking each of the three central technical elements of the production process into account: the system, the material and the process. The data resulting from each combination is assigned a Technology Readiness Level (TRL) which makes the expected performance and production capability of the solution transparent.
EOS incorporates these TRLs into the following two categories:
All of the data stated in this material data sheet is produced according to EOS Quality Management System and international standards
EOS incorporates these TRLs into the following two categories:
- Premium products (TRL 7-9): offer highly validated data, proven capability and reproducible part properties.
- Core products (TRL 3 and 5): enable early customer access to newest technology still under development and are therefore less mature with less data.
All of the data stated in this material data sheet is produced according to EOS Quality Management System and international standards
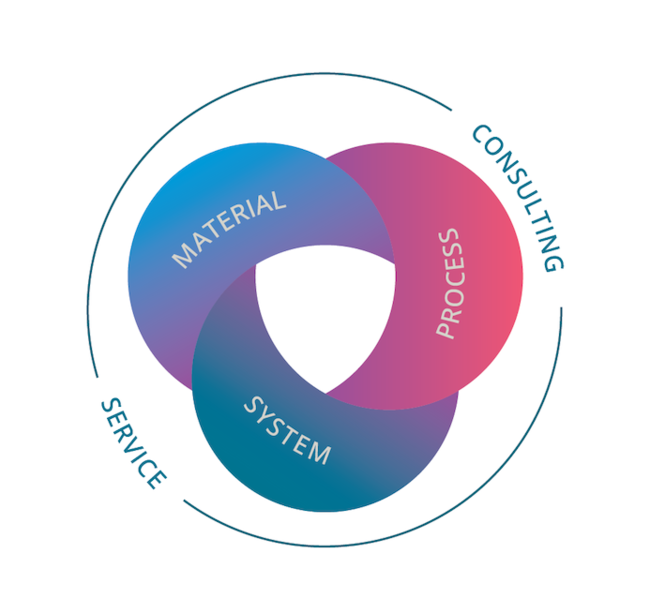
POWDER PROPERTIES
Powder Chemical Composition (wt.-%)
Element | Min. | Max. |
---|---|---|
Cu | Balance | |
Cr | 0.45 | 1.15 |
Zr | 0.05 | 0.25 |
Fe | - | 0.08 |
Si | - | 0.01 |
Powder Particle Size
GENERIC PARTICLE SIZE DISTRIBUTION | 15 - 45 μm |
---|
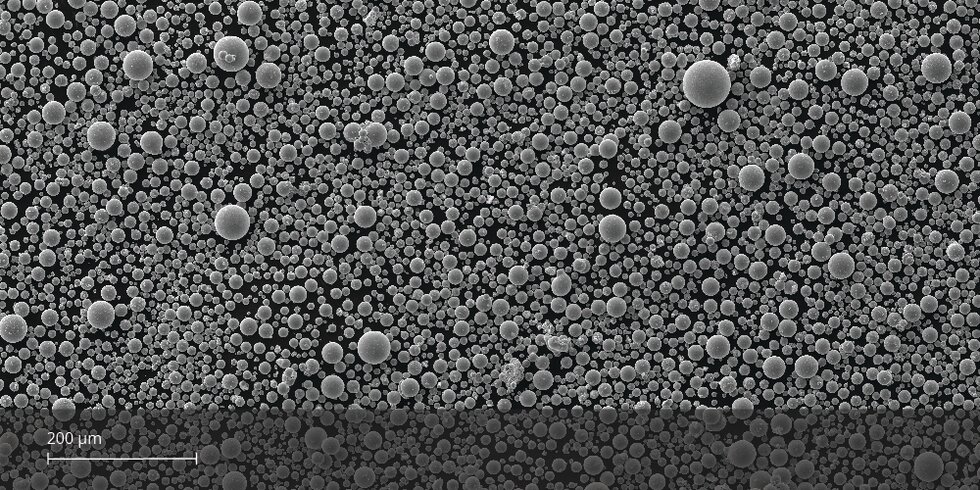
HEAT TREATMENT
CuCrZr can be heat treated to reach different mechanical properties and conductivity values.
Conductivity optimized heat treatement:
Ageing: 3 h at 550 °C under inert gas flow/atmosphere. Slow cooling in inert gas until temperature is below 100 °C
Tensile optimized heat treatment:
Ageing: 1h hold in 490°C under inert gas flow/atmosphere.
Slow cooling in inert gas until temperature is under 100°C