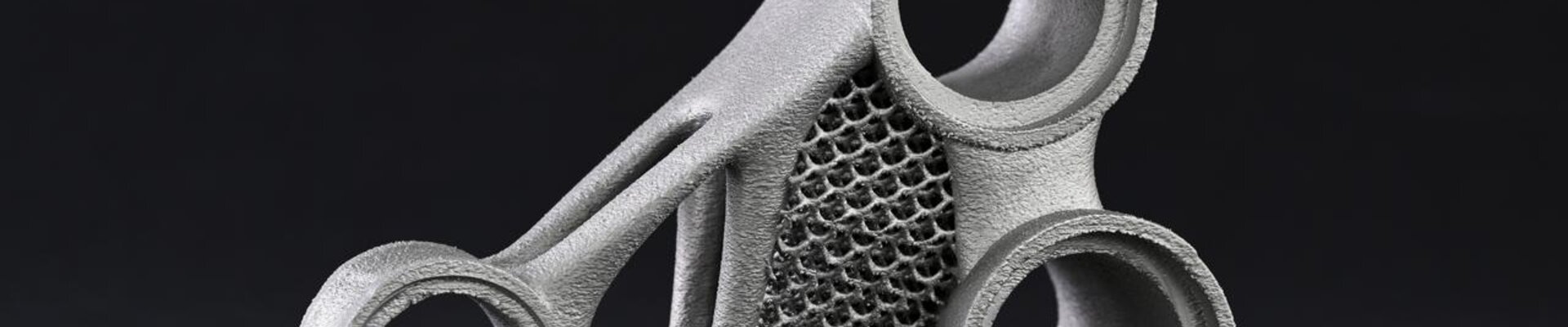
EOS Aluminium AlSi10Mg
Material Data Sheet
EOS Aluminium AlSi10Mg
Good Strength & Dynamic Load Bearing Capacity
EOS Aluminium AlSi10Mg is a widely used alloy that combines light weight and good mechanical properties. Different heat treatments can be applied to modify properties for example to increase ductility and conductivity. The material has good thermal and electrical conductivity especially after heat treatment. In addition, gas tight parts can be manufactured with EOS Aluminium AlSi10Mg.
- Good strength, hardness and dynamic properties
- High corrosion resistance
- Good thermal and electrical conductivity
- Properties can be modified with heat treatments
- General engineering components and parts subject to high loads
- Lightweight designs
- Aerospace and automotive components
- Substitution of cast AlSi10Mg parts
The EOS Quality Triangle
EOS incorporates these TRLs into the following two categories:
- Premium products (TRL 7-9): offer highly validated data, proven capability and reproducible part properties.
- Core products (TRL 3 and 5): enable early customer access to newest technology still under development and are therefore less mature with less data.
All of the data stated in this material data sheet is produced according to EOS Quality Management System and international standards
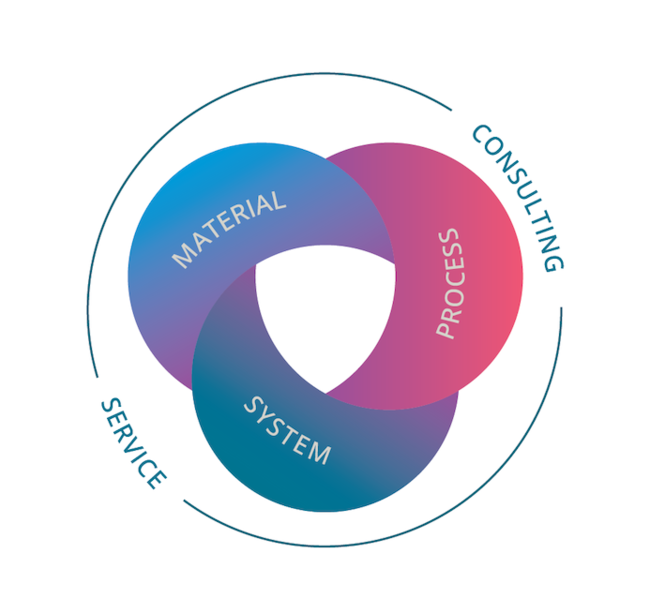
POWDER PROPERTIES
The chemical composition of the EOS Aluminium AlSi10Mg powder is in compliance with the DIN EN 1706 (EN AC—43000) and ASTM F3318 standard.
Powder Chemical Composition (wt.-%)
Element | Min. | Max. |
---|---|---|
Al | Balance | |
Si | 9 | 11 |
Fe | - | 0.55 |
Cu | - | 0.05 |
Mn | - | 0.45 |
Mg | 0.2 | 0.45 |
Ni | - | 0.05 |
Zn | - | 0.1 |
Pb | - | 0.03 |
Sn | - | 0.05 |
Ti | - | 0.15 |
Powder Particle Size
GENERIC PARTICLE SIZE DISTRIBUTION | 25 - 70 μm |
---|
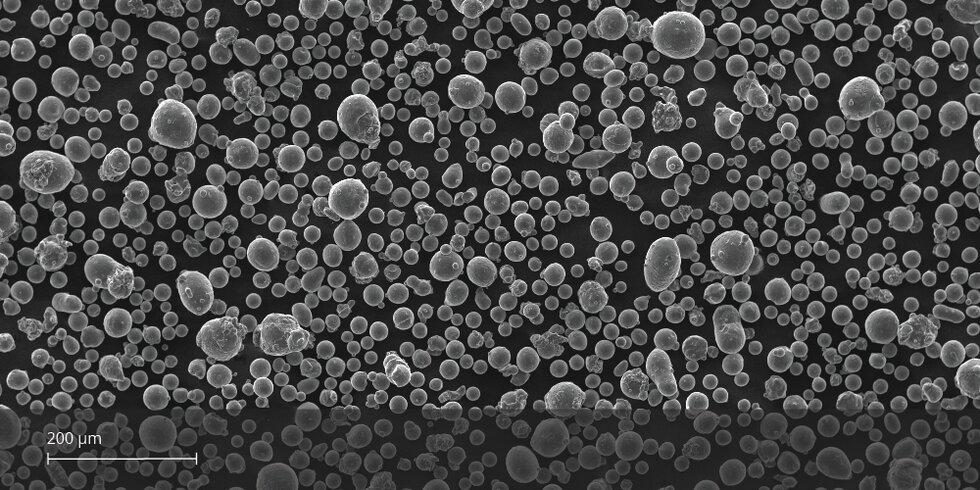
SEM micrograph of EOS Aluminium AlSi10Mg powder
HEAT TREATMENT
EOS T6 Heat Treatment
EOS has developed an AM optimized heat treatment procedure that is 40% shorter than conventional T6 heat treatment procedures.
Solution annealing 30 min @ 530 °C, water quench. Artificial aging 6 h @ 165 °C, cooling in air. Parts to preheated oven. Maximum overheating 5 °C. Delay between SA and quenching maximum 30 s. Oven type & configuration may have impact on the mechanical properties. For complex and massive parts uniform heating and cooling needs to be arranged.
EOS T6 treatment is recommended to obtain controlled mechanical properties and lower variation in mechanical values (for example in long build jobs if heat transfer from parts is limited by low amount of support and after stress relief heat treatment). An increase in porosity due to heat treatment is possible. A more detailed description of heat treatment is available upon request.
Solution Annealing
30 minutes in 530 °C followed by immediate quenching to water.
Aging
Artificial aging of 6 hours in 165 °C followed by cooling in air.
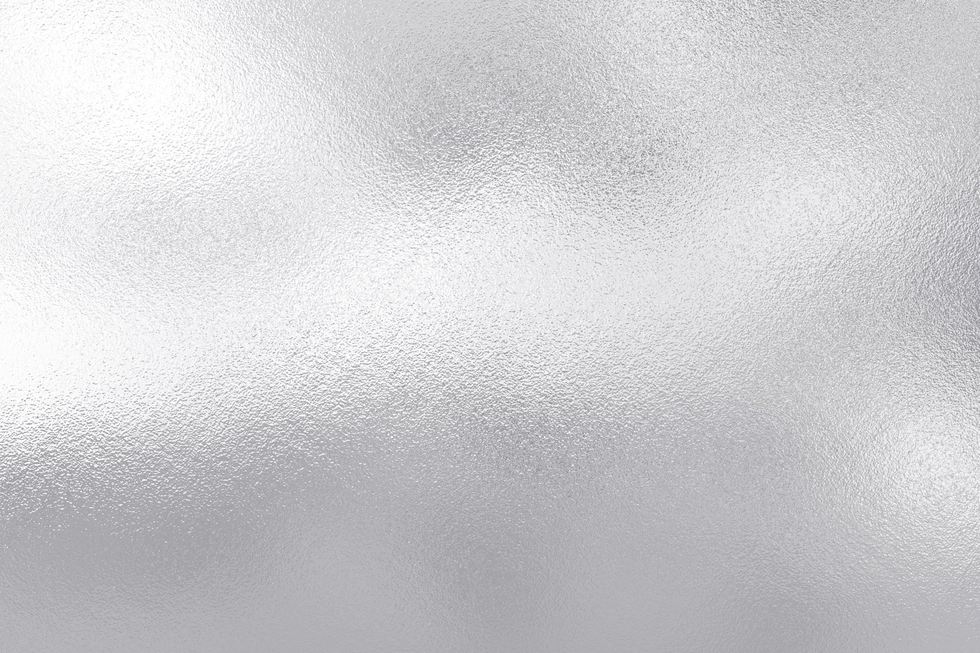