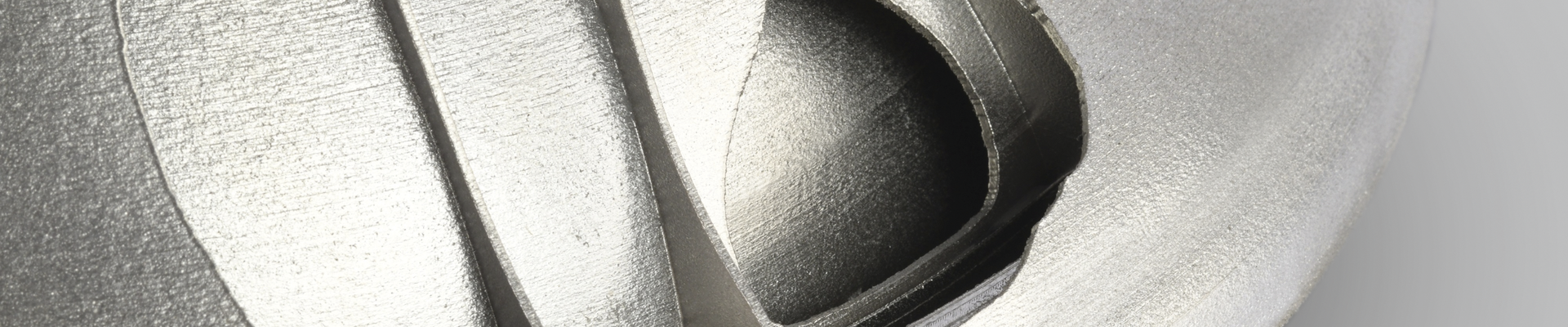
EOS NickelAlloy IN718
Material Data Sheet
EOS NickelAlloy IN718
High Temperature Strength and Corrosion Resistance
EOS NickelAlloy IN718 is a precipitation-hardening nickel-chromium alloy that is characterized by having good tensile, fatigue, creep and rupture strength at temperatures up to 700 °C (1290 °F). Parts built from EOS NickelAlloy IN718 can be easily post-hardened by precipitation-hardening heat treatments.
EOS NickelAlloy IN718 is a nickel alloy powder intended for manufacturing parts on EOS metal systems with EOS DMLS processes.
- Good tensile, fatigue, creep and rupture strength at temperatures up to 700 °C (1 290 °F)
- Parts are easily precipitation hardened
- Parts can be machined, spark-eroded, welded, micro shot-peened, polished and coated in both as-built and age-hardened states
- Available in 10 kg drum and 500 kg Big Bag packaging
- Gas turbine components
- Instrumentation parts
- Power industry parts
- Process industry parts
The EOS Quality Triangle
EOS incorporates these TRLs into the following two categories:
- Premium products (TRL 7-9): offer highly validated data, proven capability and reproducible part properties.
- Core products (TRL 3 and 5): enable early customer access to newest technology still under development and are therefore less mature with less data.
All of the data stated in this material data sheet is produced according to EOS Quality Management System and international standards
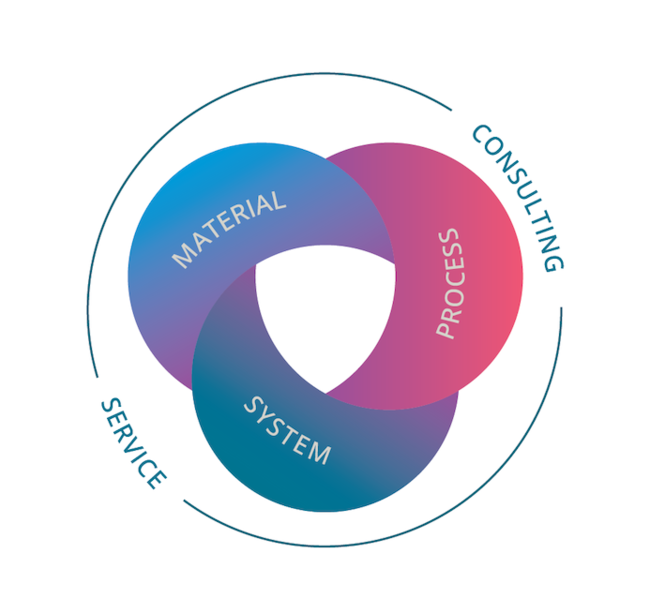
POWDER PROPERTIES
The chemical composition of EOS NickelAlloy IN718 is in compliance with UNS N07718, AMS 5662, AMS 5664, W.Nr 2.4668, DIN NiCr19Fe19NbMo3.
Powder Chemical Composition (wt.-%)
Element | Min. | Max. |
---|---|---|
Fe | Balance | |
Ni | 50 | 55 |
Cr | 17 | 21 |
Nb | 4.75 | 5.5 |
Mo | 2.8 | 3.3 |
Ti | 0.65 | 1.15 |
Al | 0.2 | 0.8 |
Co | - | 1 |
Cu | - | 0.3 |
Si | - | 0.35 |
Mn | - | 0.35 |
Ta | - | 0.05 |
C | - | 0.08 |
S | - | 0.015 |
P | - | 0.015 |
B | - | 0.006 |
Pb | - | 0.0005 |
Se | - | 0.002 |
Bi | - | 0.00003 |
Powder Particle Size
GENERIC PARTICLE SIZE DISTRIBUTION | 20 - 55 μm |
---|
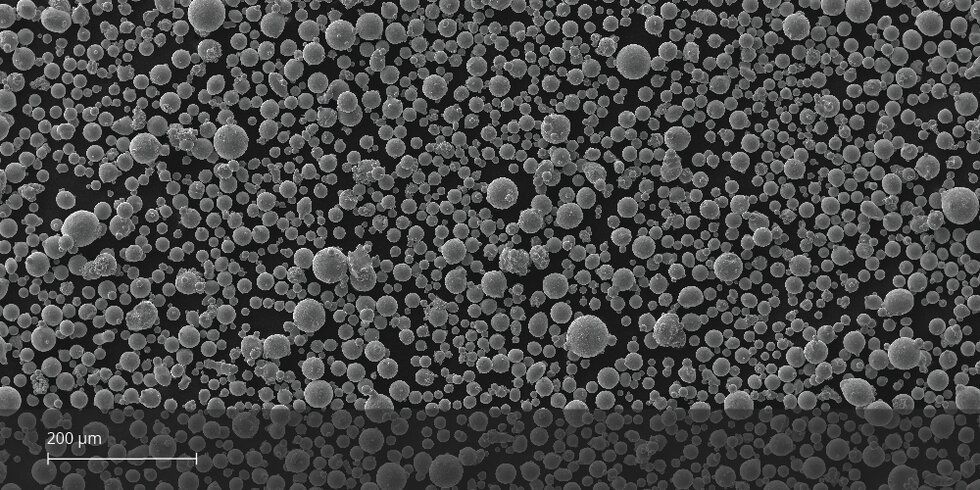
SEM micrograph of EOS NickelAlloy IN718 powder
HEAT TREATMENT
Heat treatment procedure conform to Aerospace Material Specification AMS 2774 and AMS 5662. As manufactured microstructure for additively manufactured IN718 consists of gamma phase (γ). Heat treatment for IN718 is required to produce desired microstructure and part properties (gamma double prime precipitates, γ“). Heat treatment is also used to relieve stresses
Step 1: Solution Annealing: hold at 954 °C (1 750 °F ) for 1 hour per 25 mm (0.98 inch) of thickness, air (/argon) cool
Step 2: Ageing Treatment: hold at 718 °C (1 325 °F ) 8 hours, furnace cool to 621 °C (1 150 °F ) and hold at 621 °C (1 150 °F ) for total precipitation time of 18 hours, air (/argon) cool
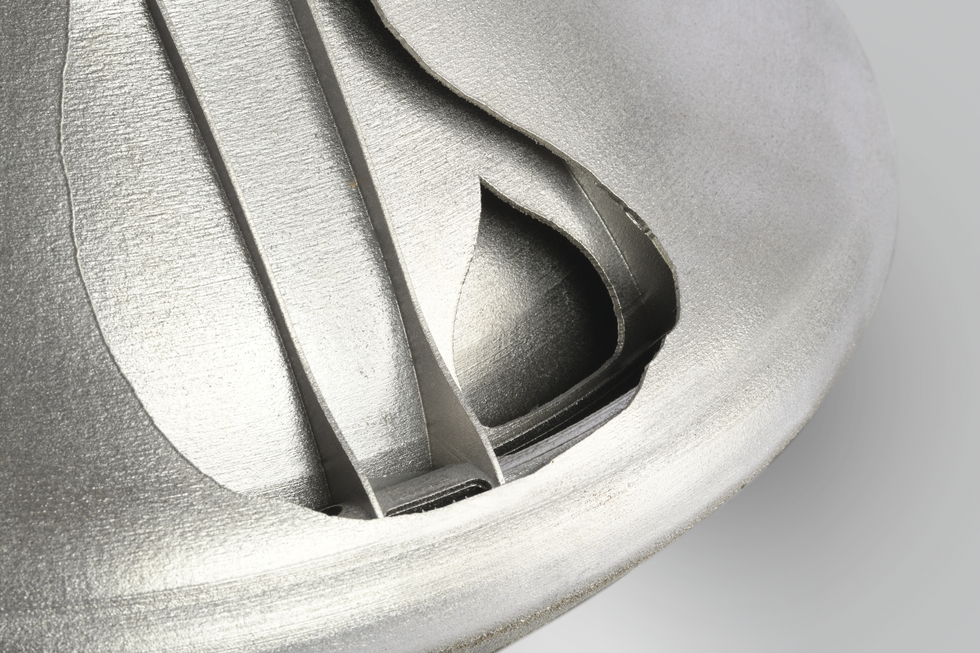
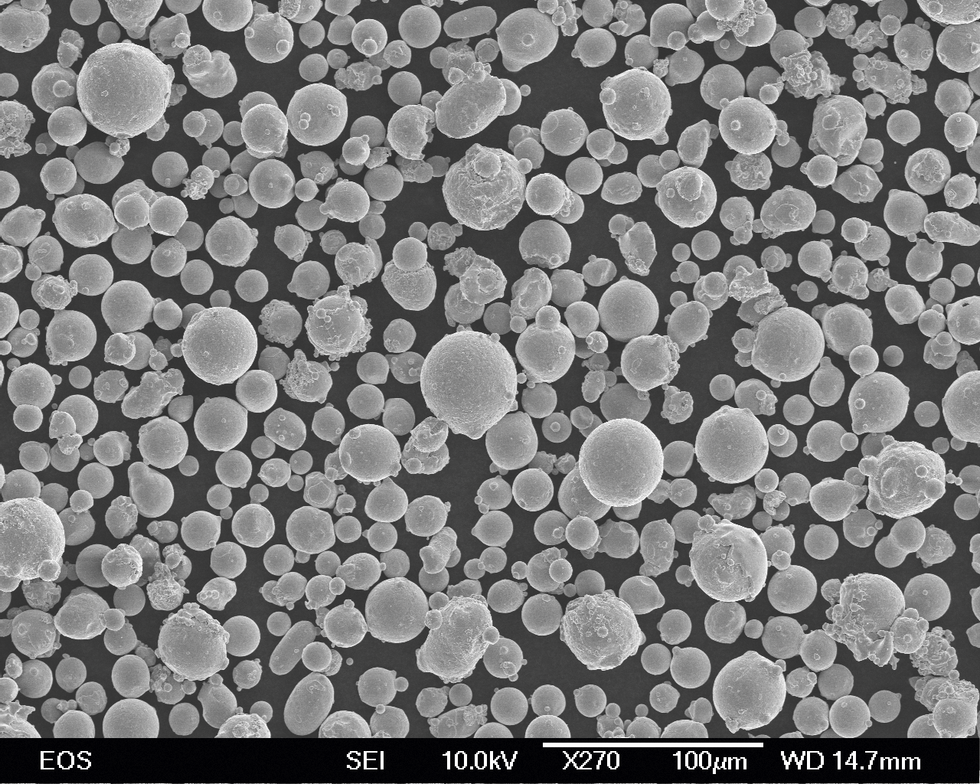