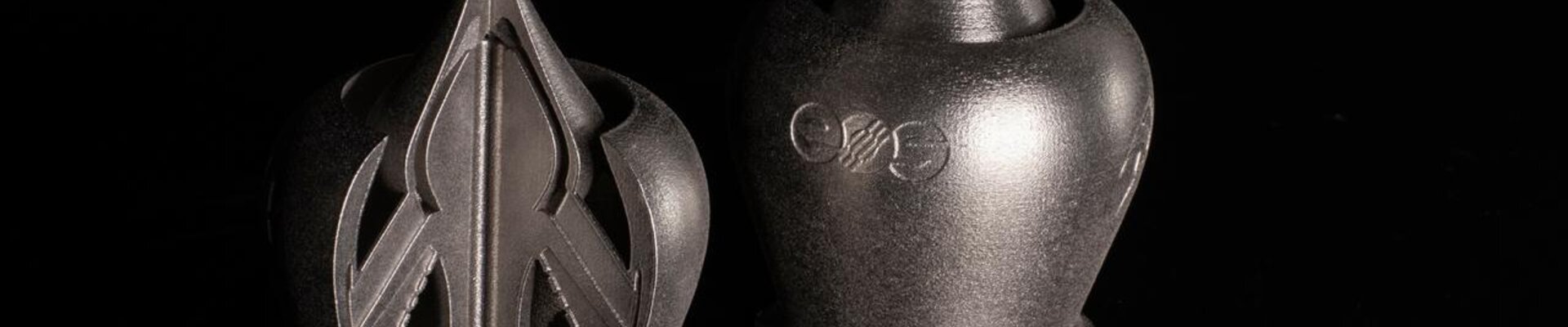
EOS NickelAlloy HAYNES® 282®
Material Data Sheet
EOS NickelAlloy HAYNES® 282®
EOS NickelAlloy HAYNES® 282® is a precipitation strengthened nickel-base superalloy with a unique combination of high temperature strength, thermal stability, and fabricability. HAYNES® 282® alloy was developed for high temperature structural applications and is manufactured under license from Haynes International Inc. EOS NickelAlloy HAYNES® 282® is a nickel alloy powder intended for manufacturing parts on EOS metal systems with EOS DMLS processes.
- Excellent strength at high temperature
- Good corrosion and oxidation resistance
- Easily fabricated and excellent weldability
- Aerospace and rocket engine components
- Turbomachinery and gas turbine parts
- Energy industry components
The EOS Quality Triangle
EOS incorporates these TRLs into the following two categories:
- Premium products (TRL 7-9): offer highly validated data, proven capability and reproducible part properties.
- Core products (TRL 3 and 5): enable early customer access to newest technology still under development and are therefore less mature with less data.
All of the data stated in this material data sheet is produced according to EOS Quality Management System and international standards
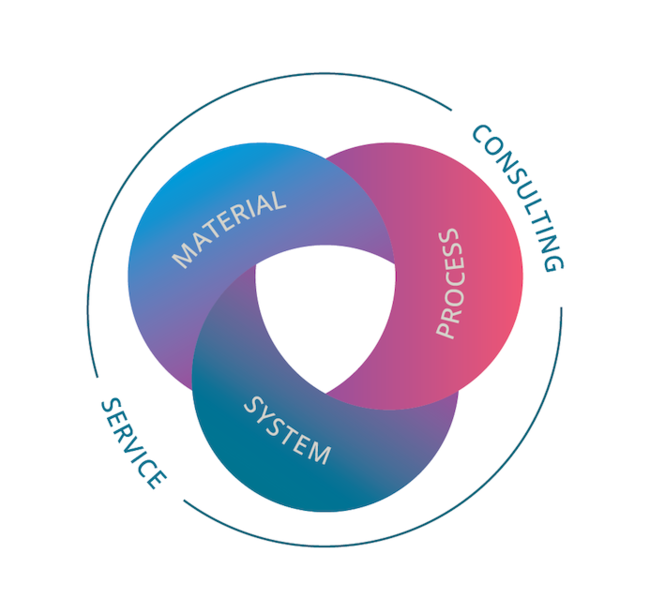
POWDER PROPERTIES
Powder composition is compliant with AMS5951 Rev. A Section 3.1 and UNS N07208.
Powder Chemical Composition (wt.-%)
Element | Min. | Max. |
---|---|---|
Cr | 18.5 | 20.5 |
Co | 9.0 | 11.0 |
Mo | 8.0 | 9.0 |
Ti | 1.9 | 2.3 |
Al | 1.38 | 1.65 |
C | 0.04 | 0.08 |
B | 0.003 | 0.01 |
Ni | Balance | |
Mn | 0.0 | 0.3 |
Si | 0.0 | 0.15 |
W | 0.0 | 0.5 |
Nb | 0.0 | 0.2 |
Ta | 0.0 | 0.1 |
Fe | 0.0 | 1.5 |
Cu | 0.0 | 0.1 |
S | 0.0 | 0.015 |
P | 0.0 | 0.015 |
Powder Particle Size
GENERIC PARTICLE SIZE DISTRIBUTION | 20 - 55 μm |
---|
HEAT TREATMENT
In as-built condition EOS NickelAlloy HAYNES® 282® has low strength and high ductility. Solution and aging heat treatments are required to produce the microstructure and strengthening phases for high temperature performance.
EOS has characterized two heat treatment options, which are described below. Heat treatment Option 1 is recommended for properties closest to wrought HAYNES® 282®.
Option 1: Recrystallization solution treatment + standard two-step aging
Option 2: Standard solution + standard two-step aging
Heat Treatment Option 1
This heat treatment results in a recrystallized microstructure with larger and more equiaxed grains than are typically found in DMLS materials. The resulting mechanical properties are isotropic, with high tensile ductility and good creep-rupture strength.
Solution treatment
Step 1: Hold at 1 250 °C (2 282 °F) for 2 hrs, followed by rapid cooling (110 °C/min (230 °F/min) or faster) to room temperature.
Aging treatment
Step 2: Hold at 1 010 °C (1 850 °F) for 2 hrs, followed by cooling equivalent to air cooling (approx 20 °C/min (68 °F/ min) or faster) to room temperature. Step 3: Hold at 788 °C (1 450 °F) for 8 hrs, followed by cooling equivalent to air cooling (approx 20 °C/min (68 °F/ min) or faster).
Heat Treatment Option 2: This heat treatment results in fine grains with high aspect ratio. Higher strength and more anisotropy may be expected relative to heat treatment Option 1.
Solution treatment
Step 1: Hold at 1 135 °C (2 075 °F) for 2 hrs, followed by rapid cooling (110 °C/min (230 °F/min) or faster) to room temperature.
Aging treatment
Step 2: Hold at 1 010 °C (1 850 °F) for 2 hrs, followed by cooling equivalent to air cooling (approx 20 °C/min (68 °F/ min) or faster) to room temperature.
Step 3: Hold at 788 °C (1 450 °F) for 8 hrs, followed by cooling equivalent to air cooling (approx 20 °C/min (68 °F/ min) or faster).