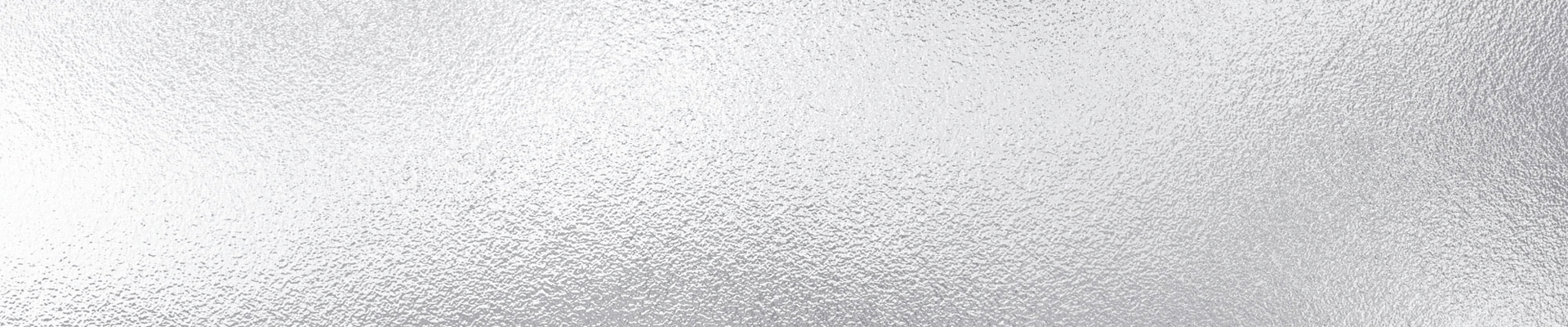
EOS Aluminium AlF357
Material Data Sheet
EOS Aluminium AlF357
Light Weight & Corrosion Resistance
EOS Aluminium AlF357 is an ideal material for applications requiring a combination of low weight and mechanical/thermal load endurance. It is a beryllium free derivative of the A357 (AlSi7Mg0.6) alloy. Parts built of EOS Aluminium AlF357 can be machined, shot-peened and polished in the as-built or heat treated state. For this product, a T6-like heat treatment may be utilized to enhance the overall mechanical properties.
- Light-weight
- Corrosion resistance
- High dynamic load bearing capacity
- Aerospace industry applications
- Defense and automotive industries
- Structural components requiring high strength
The EOS Quality Triangle
EOS incorporates these TRLs into the following two categories:
- Premium products (TRL 7-9): offer highly validated data, proven capability and reproducible part properties.
- Core products (TRL 3 and 5): enable early customer access to newest technology still under development and are therefore less mature with less data.
All of the data stated in this material data sheet is produced according to EOS Quality Management System and international standards
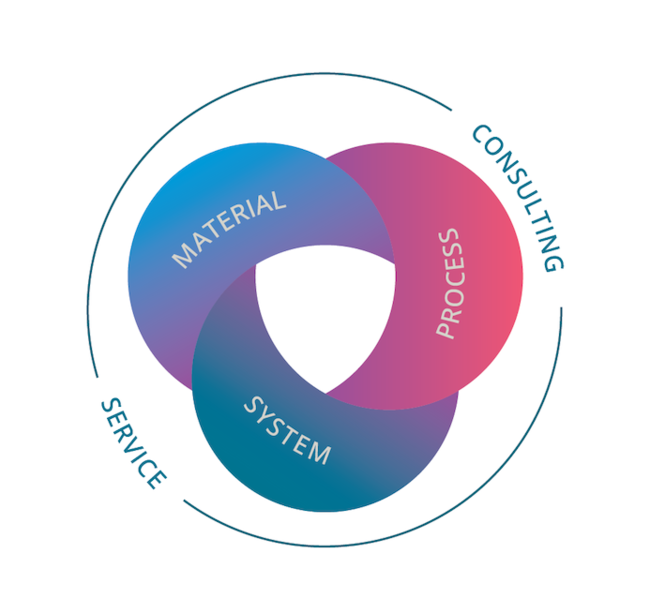
POWDER PROPERTIES
Chemical composition of the EOS Aluminium AlF357 powder is in compliance with SAE AMS 4289 standard.
Powder Chemical Composition (wt.-%)
Element | Min. | Max. |
---|---|---|
Al | Balance | |
Si | 6.5 | 7.5 |
Fe | - | 0.1 |
Cu | - | 0.2 |
Mn | - | 0.1 |
Mg | 0.4 | 0.7 |
Zn | - | 0.1 |
Ti | 0.04 | 0.2 |
Be | - | 0.002 |
Other Elements Each | - | 0.05 |
Other Elements Total | - | 0.15 |
Powder Particle Size
GENERIC PARTICLE SIZE DISTRIBUTION | 20 - 90 μm |
---|
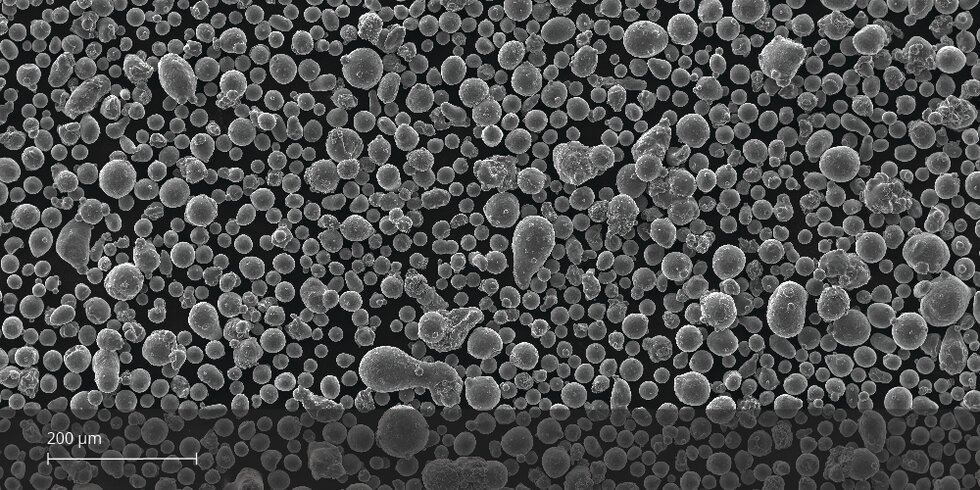
SEM micrograph of EOS Aluminium AlF357 powder
HEAT TREATMENT
Laser melting process comprises extremely fast melting and re-solidification. Due to the layerwise manufacturing method, the parts exhibit anisotropic properties depending on the building direction. Suitable heat treatments can be used to meet the needs of various applications, e.g. to reduce the anisotropy. Conventionally cast components of this type of aluminum alloy are often heat treated using a T6 cycle consisting of solution annealing, quenching and age hardening. A T6-like heat treatment has been specifically developed to increase the ductility and yield strength, and to reduce the anisotropy of the built parts, consisting of the following cycles:
Solution Annealing: 30 minutes at 540 °C (±6 °C) measured from the part, followed by instant quenching in water at room temperature.
Aging: 6 hours at 165 °C (±6 °C) measured from the part, followed by air cooling. This step is carried out with a maximum delay of 40 hours after the solution annealing. The mechanical properties for the heat treated condition have been attained through the described heat treatment procedure.