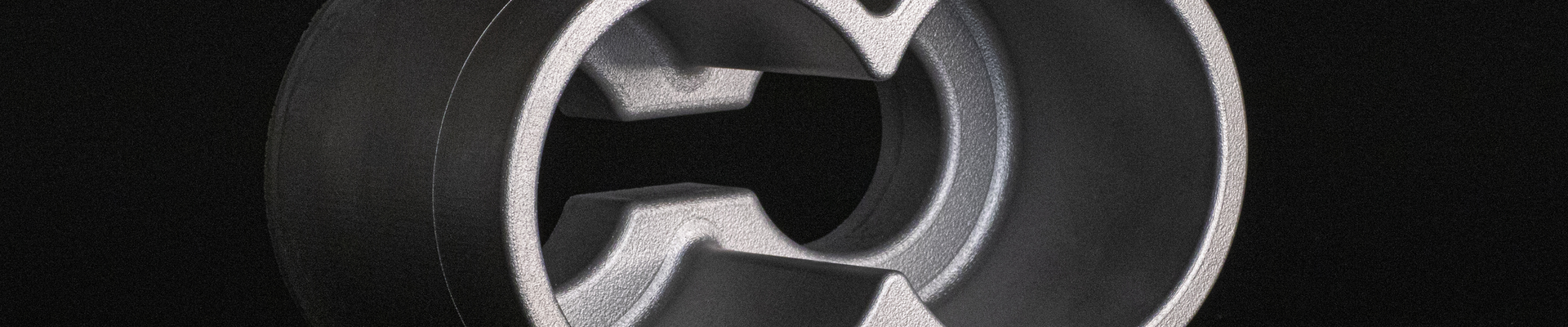
EOS ToolSteel CM55
Material Data Sheet
EOS ToolSteel CM55
EOS ToolSteel CM55 is a cobalt free ultra high strength steel for tooling and engineering solutions. Its alloying elements and moderate carbon content form a strong and stable structure for demanding applications. The properties of this steel make it suitable for cold- and hot-working tools. Producing mechanical engineering and powertrain components is well suited for this steel.
- Cobalt free
- High strength and hardness
- Stable for use in elevated temperatures
- Cold working tools
- Hot working tools
- Parts for mechanical engineering
- Powertrain components
The EOS Quality Triangle
EOS incorporates these TRLs into the following two categories:
- Premium products (TRL 7-9): offer highly validated data, proven capability and reproducible part properties.
- Core products (TRL 3 and 5): enable early customer access to newest technology still under development and are therefore less mature with less data.
All of the data stated in this material data sheet is produced according to EOS Quality Management System and international standards
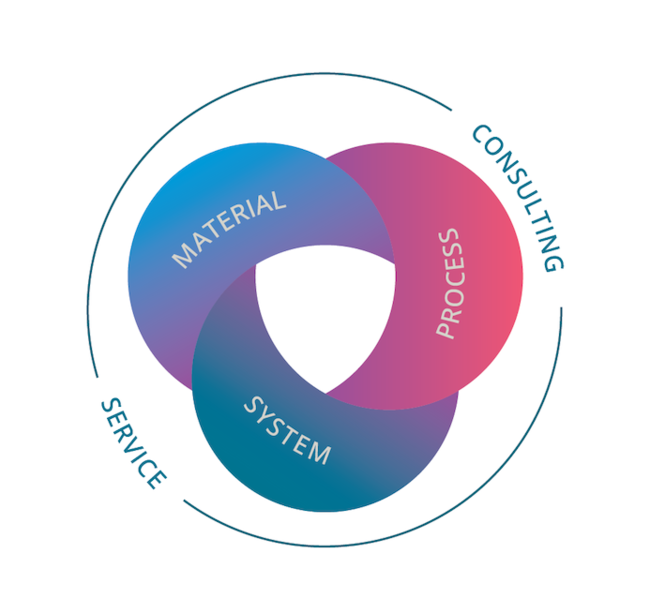
POWDER PROPERTIES
Powder Chemical Composition (wt.-%)
Element | Min. | Max. |
---|---|---|
Fe | Balance | |
Cr | 5 | 8 |
Ni | 5 | 8 |
Mo | 0.5 | 1.2 |
Al | 2 | 2.6 |
V | 0.1 | 0.25 |
C | 0.1 | 0.25 |
Powder Particle Size
GENERIC PARTICLE SIZE DISTRIBUTION | 15 - 63 μm |
---|
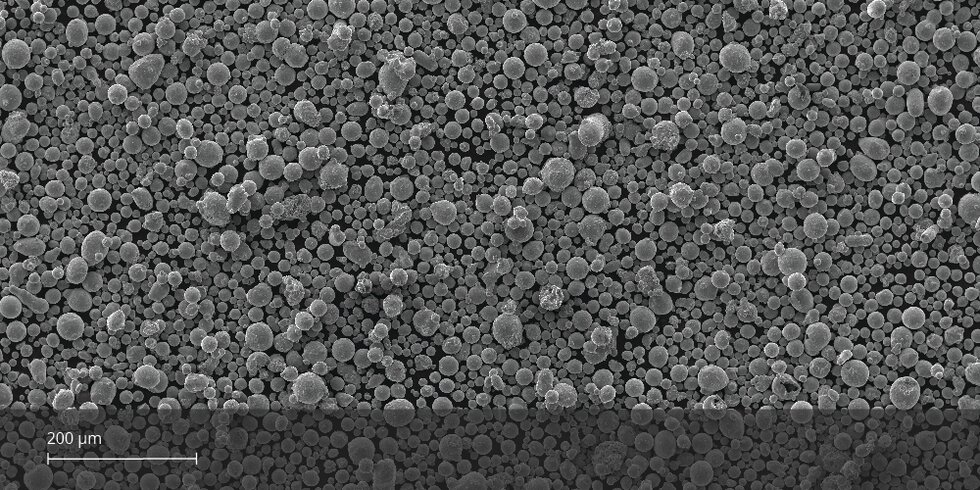
SEM micrograph of EOS ToolSteel CM55 powder
HEAT TREATMENT
EOS ToolSteel CM55 can be heat treated to different hardness levels by adjusting the aging temperature. Final state of use is achieved by a two step heat treatment. First step is hardening where a strong martensitic microstructure is formed. The final hardness and strength is obtained in an aging treatment where strengthening phases and precipitates form.
1. Hardening
2 hours in 950 ˚C measured from the part when thoroughly heated through. Rapid gas cooling or quenching in oil. Cooling to room temperature before aging treatment.
2. Aging
4 hours in 550 ˚C - 630 ˚C depending on the desired hardness. Hold time when parts have thoroughly heated through. Air cooling or equivalent cooling rate. Peak strength and hardness is achieved by aging at 550 ˚C, stated data in this document represents this state. For lower hardness and strength choose aging temperature according to the graph below.