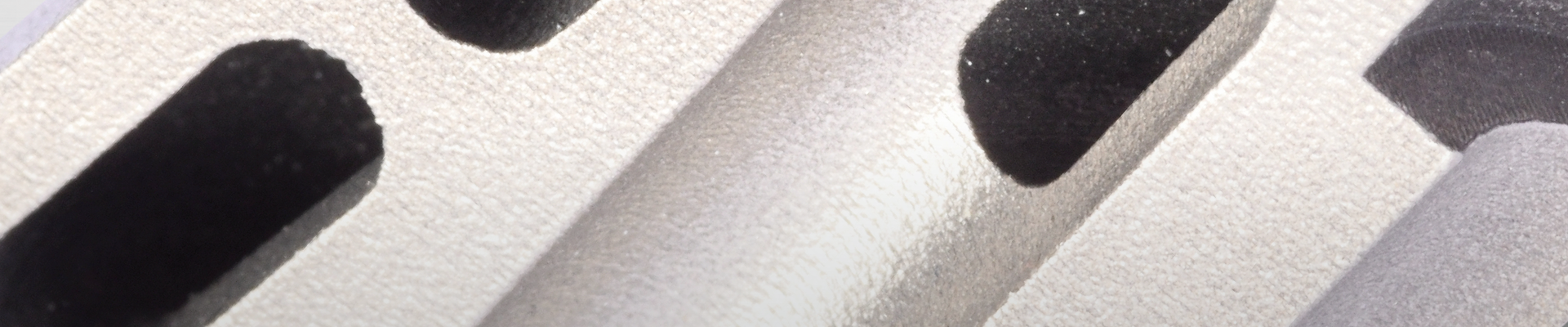
EOS MaragingSteel MS1
Material Data Sheet
EOS MaragingSteel MS1
Parts built in EOS MaragingSteel MS1 have a chemical composition corresponding to US classification 18% Ni Maraging 300, European 1.2709 and German X3NiCoMoTi 18-9-5. This kind of steel is characterized by having very good mechanical properties, and being easily heattreatable using a simple thermal age-hardening process to obtain excellent hardness and strength. Parts built from EOS MaragingSteel MS1 are easily machinable after the building process and can be easily post-hardened to more then 50 HRC by age-hardening at 490 °C (914 °F) for 6 hours. In both as-built and age-hardened states the parts can be machined, spark-eroded, welded, micro shot-peened, polished and coated if required. Due to the layerwise building method, the parts have a certain anisotropy, which can be reduced or removed by appropriate heat treatment.
- The parts are easily post-hardened to more than 50 HRC
- The parts can be machined, spark-eroded, welded, micro shot-peened, polished and coated
- Chemical composition corresponding to 18Ni300 and M300
- Injection molding tools & inserts
- Mechanical engineering parts
The EOS Quality Triangle
EOS incorporates these TRLs into the following two categories:
- Premium products (TRL 7-9): offer highly validated data, proven capability and reproducible part properties.
- Core products (TRL 3 and 5): enable early customer access to newest technology still under development and are therefore less mature with less data.
All of the data stated in this material data sheet is produced according to EOS Quality Management System and international standards
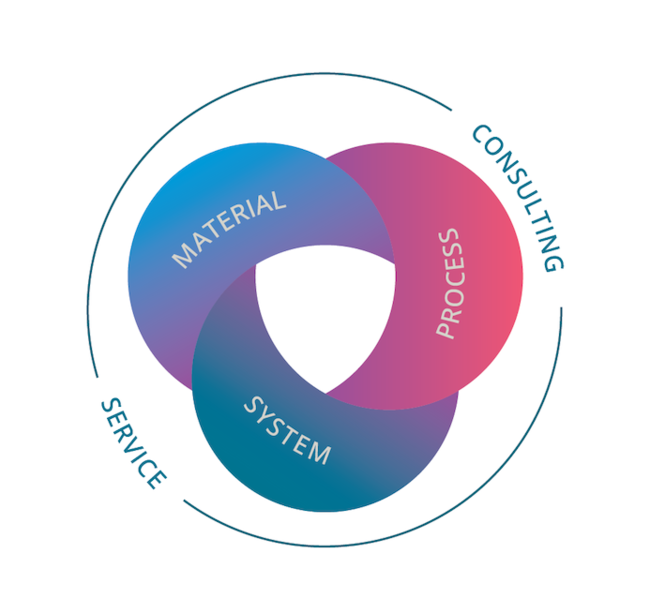
POWDER PROPERTIES
Parts built in EOS MaragingSteel MS1 have a chemical composition following US classification 18% Ni Maraging 300, European 1.2709 and German X3NiCoMoTi 18-9-5.
Powder Chemical Composition (wt.-%)
Element | Min. | Max. |
---|---|---|
Ni | 17 | 19 |
Co | 8.5 | 9.5 |
Mo | 4.5 | 5.2 |
Ti | 0.6 | 0.8 |
Al | 0.05 | 0.15 |
Cr | - | 0.5 |
Cu | - | 0.5 |
C | - | 0.03 |
Mn | - | 0.1 |
Si | - | 0.1 |
P | - | 0.01 |
S | - | 0.01 |
Powder Particle Size
GENERIC PARTICLE SIZE DISTRIBUTION | 15 - 65 μm |
---|

HEAT TREATMENT
Heat treatment procedure
Solution treatment at 940 °C (1724 °F) for 2 hours, air cooling + ageing at 490 °C for 6 hours, air cooling.