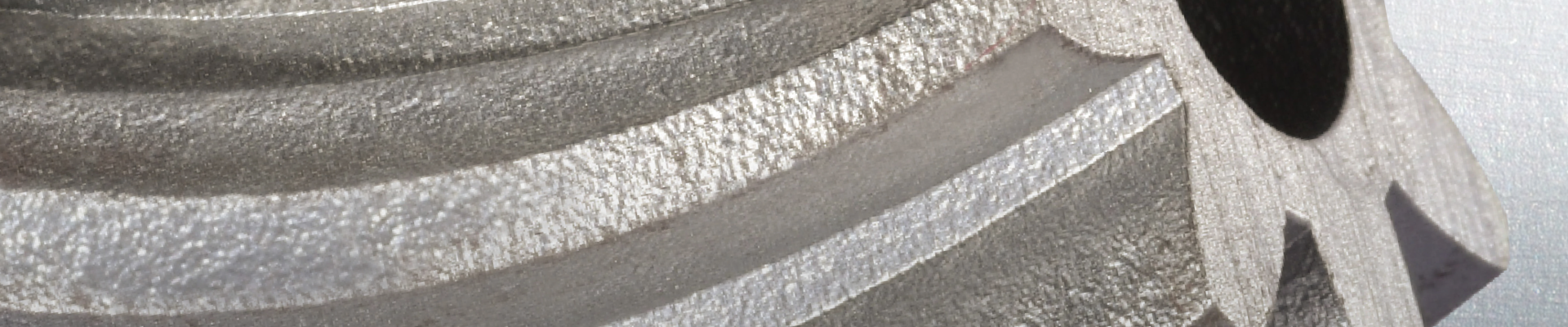
EOS CaseHardeningSteel 20MnCr5
Material Data Sheet
EOS CaseHardeningSteel 20MnCr5
Case hardening steel with good hardenability reaching good wear resistance due to high surface hardness after heat treatment.
- Good wear resistance
- Excellent surface hardness after carburizing
- Material according to EN-10084 alloy number 1.7147
- Carburizable to achieve surface hardness of 60 HRC
- Automotive and general engineering applications
- Gears, mechanical parts
The EOS Quality Triangle
EOS incorporates these TRLs into the following two categories:
- Premium products (TRL 7-9): offer highly validated data, proven capability and reproducible part properties.
- Core products (TRL 3 and 5): enable early customer access to newest technology still under development and are therefore less mature with less data.
All of the data stated in this material data sheet is produced according to EOS Quality Management System and international standards
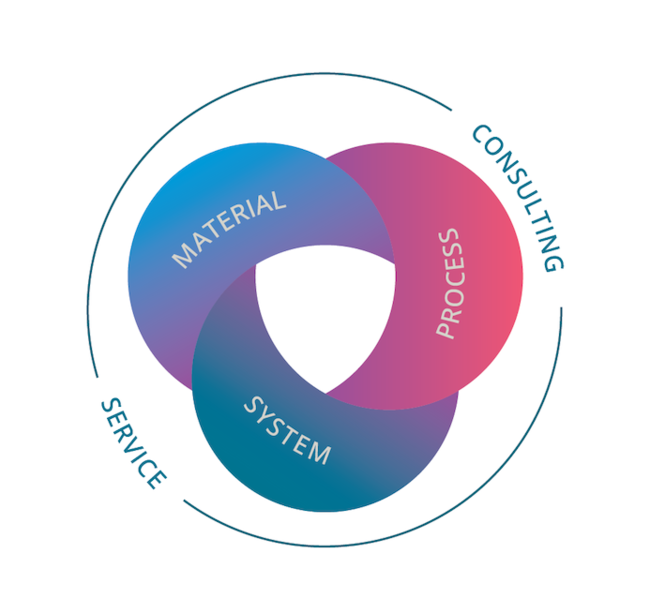
POWDER PROPERTIES
EOS CaseHardeningSteel 20MnCr5 powder material is in accordance with EN-10084 alloy number 1.7147.
Powder Chemical Composition (wt.-%)
Element | Min. | Max. |
---|---|---|
Fe | Balance | |
Mn | 1.1 | 1.4 |
Cr | 1 | 1.3 |
C | 0.17 | 0.22 |
Si | - | 0.4 |
S | - | 0.035 |
Powder Particle Size
GENERIC PARTICLE SIZE DISTRIBUTION | 15 - 55 μm |
---|
HEAT TREATMENT
Step 1
Hardening:
840 - 870 °C, hold time 30 min when thoroughly heated, water or oil quenching
Step 2
Tempering:
160 - 200 °C, hold time 2 h when thoroughly heated, air cooling
Optional softening:
Step 1: Hardening
Step 2: Tempering
Optional softening treatment:
Normalizing 870 °C, hold time 1 h when thoroughly heated, air cooling
Optional carburizing in carbon rich atmosphere:
Carburizing treatment 860-900 °C, cooling in air. Hardening and tempering to be performed after carburizing.
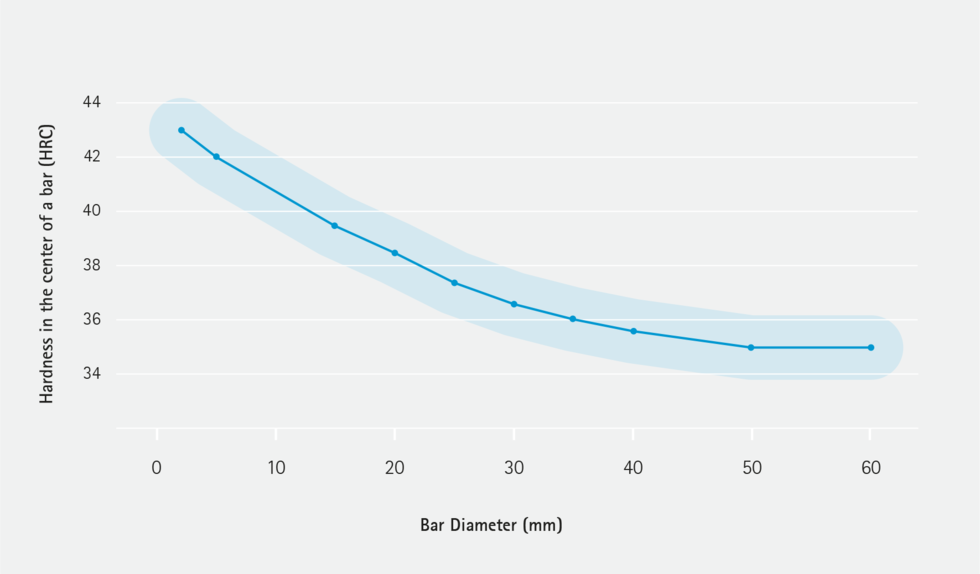